Water for reuse: how filtration is cleaning up
18 Jul 2016
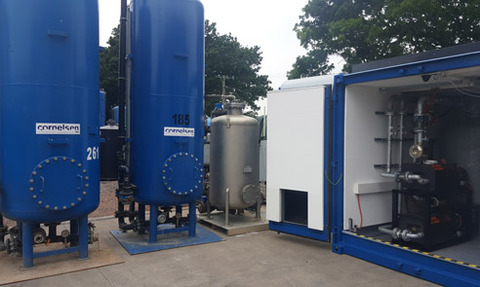
For small-scale operations, filtration can offer an efficient way of handling process water for reuse, writes Michelle Knott.
The world’s unquenchable thirst for fresh water is likely to become a huge challenge for the process industries, with global demand forecast to grow by 40% within the next 20 years.
“Water is a key resource and the cost of filtering, treating and distributing it is not cheap,” says Matthew Ingram, development engineer with Cornelsen UK, a distributor for international filtration group, Amiad.
“It is perhaps not as stressed here [in the UK] as in some regions yet…but it is a limited resource and one we are in general using too much of.”
According to the collaborative think-tank, the 2030 Water Resources Group, a third of the world’s population will experience water scarcity to the point where it will affect the production of staple foods.
Water is a key resource and the cost of filtering, treating and distributing it is not cheap
Matthew Ingram, development engineer, Cornelsen UK
This is clearly unsustainable. Even in less water-stressed regions, the cost of water and waste treatment is driving many industries to consider their options for reuse and recycling.
“Groundwater levels in general across the UK are lowering. London already has to import water from Wales. Action now has to be better than leaving it too late,” says Ingram.
All-singing, all-dancing on-site water treatment is probably only ever going to be an option for the biggest operations, but filtration can provide a cost-effective option for cleaning up process water for reuse in more modest applications.
“Most industrial processes have scope for some water recycling,” says Ingram. In the food industry, water from a hygiene application such as salad washing could be filtered to remove particles and then be used for non-critical washdown.
“This would be a very simple filtration application but could potentially halve the client’s water bill and sewerage bill. Similar possibilities exist in many industries; generally if there is water involved in reasonable quantity, it can be re-used. The viability is easily established early on in the enquiry.”
New potential
Steve Cupples, founder of recent start-up Ex-Tech, has been working in filtration for 35 years. He agrees that there are huge potential benefits to reusing process water. “If you can reuse water just once you can cut your bills by 50%. So even if you’re only using 8-10m3/h, you can still invest £20,000 and it will pay for itself in a year. And, in fact, many processes can reuse water many times.”
Cupples is currently working to develop a system that aims to improve on existing filtration technology. Discussions are underway with potential partners for the proposed technology, dubbed the X-Flow-OV.
The new system will build on existing technology that uses a flatbed filter and maintains turbulence at the surface to deter bio-fouling by holding any filtered contamination in suspension above the filter media bed. This leads to lower pressure drops (and hence lower power consumption), longer filtration and shorter backwash cycles.
Cornelsen also offers a system using a similar approach, courtesy of the company’s recent deal with Amiad. According to Ingram, the Dual Vortex Filter (DWF) removes solids down to sub-micron levels and offers a reduced bacteria count, thanks to a filtration efficiency of up to 99%. The company also claims that short backwash times and low backwash volumes reduce process water losses by up to 95%.
If you can reuse water just once you can cut your bills by 50%…And, in fact, many processes can reuse water many times
Steve Cupples, founder of Ex-Tech
But how can a process operator decide which type of filtration or water treatment system is right for their application? “We would look to recycle to the minimum required specification as this will be the most economical for the client. Further filtration is then possible, until the point where R/O [reverse osmosis] is producing what is known as ‘dead water’ – effectively just H2O.”
He also says that the right system depends on the type of contamination. “Contaminants can really be regarded as particulate or chemical. Particulates are, as the name implies, particles and of these there is ‘deformable and non-deformable’.
“These two brackets will determine the most appropriate filter for us to use to remove them,” says Ingram.
If the contamination is chemical, it may require treatment solutions beyond the scope of straightforward filtration.
Maintenance and accessibility are the other big considerations. “Can they shut down the process to clean a filter and how often will they be cleaning it? Can they cope with that within their workload?” asks Ingram. “These are the obvious questions to decide on auto cleaning or manual. Semi-automatic may offer a halfway house.”
Different stages
Whatever the complexities of choosing the right solution, one thing is certain: get it right and the rewards can be compelling.
For example, filtration and water treatment company Culligan recently helped one OEM customer devise a customised solution capable of reducing the amount of water used by liquid filling stations in the food industry. It says the resulting system can recover between 95% and 100% of the dispensed water.
The filtration station can treat 40, 70 or 100l/min of water contaminated with oil and grease and/or hydrogen peroxide (from cleaning operations). This means that the largest, 100l/min, version can save up to 22 million litres per year (assuming 4,000h/ year of operation).
The system comprises three stages of filtration, followed by UV disinfection to neutralise any microbial contamination. A coalescence filter removes oil and grease, a mechanical filter tackles particles down to 20 micron, and a carbon filter removes any hydrogen peroxide. Disinfection is followed by a further mechanical filter, a chiller, and carbon dioxide injection to control the pH.
The right filtration and water treatment system can be the key to unlocking growth
Jim Baker, business development director, Culligan UK
“We’re obviously working with companies all the time to devise systems that help them optimise their water consumption using appropriate filtration and water treatment systems,” says Jim Baker, business development director with Culligan UK. He argues that in some cases, high water consumption can have business-limited implications.
“One of our clients wants to expand but they’ve only got a small water main to their site and it can’t deliver the extra water they need. They must recycle their effluent or the water company says it will cost them £250,000 to put in a bigger main and could take a year. In a situation like that, the right filtration and water treatment system can be the key to unlocking growth.”
Making membranes
A new form of 3D printing developed by US researchers may offer a faster method for developing and testing improvements in polymer membrane prototypes.
Commonly used in water purification, food processing, and in energy applications such as fuel cells, these polymer ‘ion exchange’ membranes are structured as thin sheets.
However, the use of 3D patterns on top of the membrane surface is now being explored to solve issues such as fouling.
The manual creation of these patterns can be very time intensive, and limited in scope. To solve this issue, researchers from Penn State developed a custom 3D photolithographic printing process.
A paper published in the American Chemical Society’s journal ACS Applied Materials and Interfaces describes the process designed to speed development of new membrane patterns.
“We thought if we could use 3D printing to fabricate our customsynthesised ion exchange membranes, we could make any sort of pattern and we could make it quickly,” said Michael Hickner, associate professor of materials science and engineering at Penn State.