Efficiency factor: pumps offer oil & gas a boost
25 Jul 2016
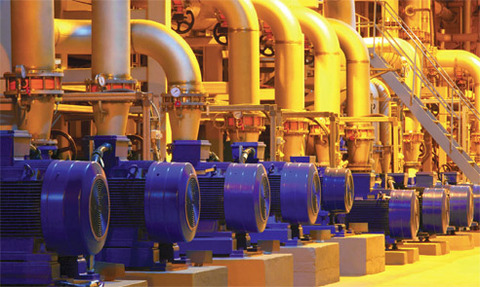
As the oil and gas industry struggles through the hardship of depressed oil prices, Dermot Martin investigates whether energy efficient pumps can offer the sector some respite.
The energy used by pumps worldwide is staggering. Danish pump manufacturer Grundfos says pumps account for roughly 10% of the energy consumed globally, while the British Pump Manufacturers’ Association (BPMA) claims pumping systems account for closer to 20% of the world’s electrical energy demand.
Whichever figure is most accurate, it’s clear pumps are highly energy intensive. Fortunately, the majority of pumps manufacturers are driven by a desire to design and integrate kit that is reliable and increasingly more efficient.
And in highly competitive markets, any edge in design or innovation can give a manufacturer a commercial advantage.
This is particularly true within the oil and gas industry which relies heavily on pumps to get product out the ground.
Many of these units have already been in operation for years. The production impact of taking them out of service, for either replacement or some level of improvement in energy use, outweighs any potential cost saving by such undertakings
Steve Schofield, director and chief executive of the BPMA
However, even though the price of oil and gas has fallen sharply over the last two years, pump experts argue that efficiency is not always top of the industry’s agenda.
“For heavy-duty ‘front-end’ pumps, serviceability and reliability is probably of greater concern than energy efficiency,” says Steve Schofield, director and chief executive of the BPMA.
“Many of these units have already been in operation for years. The production impact of taking them out of service, for either replacement or some level of improvement in energy use, outweighs any potential cost saving by such undertakings.”
He adds that because the entire oil and gas industry is a significant consumer of electrical energy, there is also a need for pumps of all specifications and sizes right across its operations — not just at the well-head.
Diagnostic solutions
Despite the offshore sector’s focus, energy savings can be made by monitoring the efficiency of downstream pumps and valves.
Typically, pump failures in refineries can cause production losses of up to 0.2%, and pump repairs consume up to 7% of an average maintenance budget.
In a 250,000-barrels-a-day refinery, monitoring solutions can reduce maintenance costs and production losses by up to 30% annually and deliver savings of up to $1 million (£675,000) a year, experts suggest.
Pre-engineered pump health monitoring solutions deliver diagnostic information to predict issues and take corrective action to reduce downtime and maintenance costs
Alcino Beirao, performance excellence consultant, Emerson Process Management
Alcino Beirao, who is a performance excellence consultant with Emerson Process Management, says: “All operators wish to avoid slowdowns and shutdowns by gaining real-time insight into pump health that enables them to take corrective action.
“Pre-engineered pump health monitoring solutions deliver diagnostic information to predict issues and take corrective action to reduce downtime and maintenance costs.”
Beirao cites the example of the Emerson pump health monitoring solution for providing real-time monitoring of essential pumps.
“We are talking about providing diagnostic data that is trended, chronicled, and analysed to alert operators to potential issues that contribute to failures before they arise,” he says.
Beirao says the monitoring solution enables operators to choose which pumps to monitor.
“For example, if pumps have previously experienced cavitation, differential pressure and vibration detection — sensors can be integrated. Protection can [also] be expanded to include leak detection or for visibility on seal failures.”
Beirao says it is important to understand that pump failures have serious knock-on effects for safety and environmental incidents as well.
“[This] can attract negative publicity, agency audits, remediation costs, and in some cases hefty fines,” he warns.
Motor concern
Meanwhile, plant operators also have to understand broader considerations.
Christoph Pauly, technical spokesman for pumps and valves at KSB, says: “There’s been much discussion lately about energy efficient motors and how they can contribute to pump efficiency.
“But unless the most appropriate pump is selected for the application, then correctly setup and operated, the efficiency of the motor will have little influence.”
He says if maintenance intervals can be extended without impacting on the performance of the pump, then the pump will deliver an improved working life and reduce costs.
However, he says not all factors that influence efficiency are in the hands of the pump manufacturer.
There’s been much discussion lately about energy efficient motors and how they can contribute to pump efficiency
Christoph Pauly, technical spokesman for pumps and valves at KSB
He therefore urges customers to supply a comprehensive profile and in-depth analysis of the application before choosing the pump. In situations where a large number of smaller-powered pumps are required, however, carrying out such in-depth analysis can be impractical.
It is a conundrum KSB is well aware of, Pauly says. “End-users can be reluctant to consider looking at an alternative proposal. There are devices such as KSB’s pump meter which is useful for measuring the suction pressure, discharge pressure, differential pressure and head pressure, providing a pump curve to illustrate the operating range and producing a load profile of the pump.
“It helps the supplier and the customer to deduce if the pump is operating efficiently or not.”
Meanwhile, another factor to consider is the efficiency of hydraulic parts. These have to be matched exactly to the performance required. For example, oversized impellers are notorious energy wasters.
Trimming the outside of the impeller diameter to the exact flow rate required of the system can yield energy savings of up to 10% and contribute to reduced maintenance costs and longer service life.
Complete control?
Controlling pump speed can offer even greater savings potential, with solutions available to control the speed of the pump exactly to the output that is needed, say experts.
Variable speed drives, for example, provide dynamic pressure compensation, which will facilitate extra savings under low-flow conditions. They have the potential to reduce power consumption by up to 60%, and Pauly says some units can also be retrofitted to existing equipment
Valves: independent intelligence
Power management company Eaton has developed a mobile valve, which features independent monitoring. Eaton says the valve has been designed to offer manufacturers “nearly endless possibilities” to differentiate machine capabilities.
The CAN-enabled electrohydraulic mobile valve also features on-board electronics and software algorithms, which, the company says, offers “a valuable solution in the industry standards for intelligence, capabilities, dynamics and control”.
“Eaton’s new CMA Advanced Mobile Valve with independent metering dramatically streamlines and simplifies everything, from design and setup to operation and optimisation, says Andreas Kling, product marketing manager at Eaton.
“Mobile equipment manufacturers are looking for products that enhance productivity and efficiency, maintain a competitive cost structure and provide real-time data,” Kling adds.
The valve is available with rated flow of 90 or 200 litres per minute. Independent metering on the valve also allows each spool to control its own work port for consistent speed and better control on services, which transition between passive and over-running states, Eaton says.