On the meter: smart ways to control energy output
30 Aug 2016 by Louisa Hearn
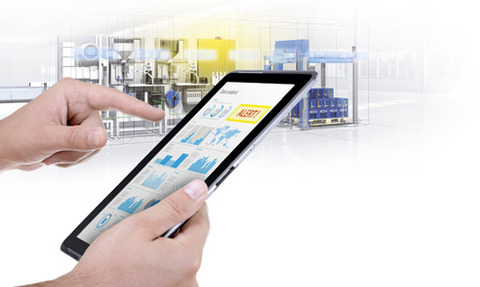
Smart energy savings can be found in the smallest of spaces, writes Louisa Hearn.
Rising energy bills, taxes and environmental laws have all played their part in pushing energy efficiency onto the corporate ‘must-do’ list.
As initiatives such as the Environment Agency’s Energy Savings Opportunity Scheme (ESOS) take hold, energy usage audits are also soon to become the norm within the UK’s industrial sector.
But while many companies have been slow to develop advanced energy management strategies, experts say the benefits to the bottom line can be immense.
According to EEF, the manufacturers’ organisation, energy affordability is now a concern for over eight in 10 manufacturers (83%), while energy spend represents more than 6% of total turnover for over a quarter of UK manufacturing companies.
It says technologies offering energy metering and monitoring can provide relief to plant operators by gathering crucial information about how processes are performing, leading to simple energysaving activities such as reducing waste and avoiding peak tariffs.
Data calls
James Wyse, national sustainability lead at EEF, says the issue of how to better manage energy costs has risen up the corporate radar, driven by “higher energy costs, legislation and compliance”.
To meet this need, the EFF has recently introduced a new service to help manufacturers improve sustainability through carbon and energy management.
Pressure from the supply chain means many larger companies now “expect suppliers to demonstrate that they are addressing environmental responsibilities, including energy management,” says Wyse.
Metering is often an area that gets overlooked but is a very important starting point on the journey, Wyse adds.
“We quite often find that companies have half hourly data for electricity but only estimates for natural gas.
“Sometimes companies are being charged for electrical meters they are not even using. They need to understand what they are using, because only then can they begin to take control.”
For those wanting to better understand their energy usage, metering can offer the scientific data to demonstrate it, he adds.
Sometimes companies are being charged for electrical meters they are not even using. They need to understand what they are using, because only then can they begin to take control
James Wyse, national sustainability lead at EEF
And sub-metering equipment for individual production lines can deliver even greater insights, by allowing operators to start benchmarking their performance.
Metering can also help companies to identify energy waste such as that caused by leaking compressors. Other energy saving measures can include investing in more controls on the running of machinery, he says.
“Some machinery can be controlled from a laptop and will respond to peak demands and productivity.”
Another solution is to install a variable speed drive (VSD) to older machinery and compressors, which Wyse says can “save 25% of energy use”.
For companies looking to roll out a comprehensive energy management strategy, he points to the internationally recognised standard ISO 50001, which is beginning to make inroads.
Bottom line
Dan Rossek, marketing manager at Omron, says a strong factor pushing businesses to consider adopting standards such as ISO 50001 are the unnecessary costs of being inefficient.
“Companies are being taxed on energy consumption, so it is a real cost to them, which means any cuts are important to the bottom line,” he says.
In addition, they also want to be seen “as an ecologically-minded company, which influences the message they take to market”.
While every company will measure energy use across the whole business, Rossek says only 20% measure down to the plant or component level.
To fully understand and optimise energy consumption, he says operators must be able to monitor and benchmark energy usage.
“This entails more than looking around the shop floor for obvious energy saving opportunities, such as turning off the heating and lighting when the plant is running unmanned processes, or ensuring equipment isn’t running if it doesn’t need to be.”
The big change is that while companies are keen on monitoring overall energy, we are now seeing a move to monitoring a component at the machine or line level for improvements in energy usage
Dan Rossek, marketing manager at Omron
And while installing variable speed drives, for example, can help to reduce energy consumption from motors and compressors, it isn’t the end of the story, he adds.
“Deriving the maximum value from these energy saving measures, and uncovering others to implement, depends on effective monitoring of a whole range of electrical loads, energy supplies and other energy consumers, such as compressed air and pneumatic systems.”
Ethernet-based network technologies can make it easier to transfer data from the plant floor into business level visualisation systems, but data must also be collected and interpreted, he adds.
To serve this need, Omron has developed a series of multi-circuit smart power monitors for areas such as temperature, motion, heat and compressed air and electricity. Rossek says these can be retrofitted to existing production lines and processes or designed into new equipment.
On the monitor
When used in conjunction with its KM-Manager software, users can also collect data, display it on a PC and perform trend analysis with graphs of energy and other data, he says.
“The big change is that while companies are keen on monitoring overall energy, we are now seeing a move to monitoring a component at the machine or line level for improvements in energy usage,” says Rossek.
“Monitoring overall consumption of a machine only gives a snapshot. Operators now want to see energy consumption by individual conveyers, but it can be costly to add a device to every single element on every machine.”
He says this was the reasoning behind the development of multi-loop systems, because they can provide operators with multiple monitoring points on a single controller.
Green guides
The rising demand to trim costs and raise plant efficiency has spawned a series of new guides for energyintensive industries.
Hot off the press is the Energy Institute’s (EI) peer reviewed Guide to Energy Management.
As the second part of the EI’s Energy Essentials collection, the guide is a free download designed to offer foundation-level understanding of energy topics to non-experts.
The EI says it outlines the main drivers for managing energy, and how to introduce and implement energy management within an organisation. International standards, such as ISO 50001, and the associated ‘Plan-Do- Check-Act’ framework, and other key terms and concepts are also explained.
Martin Maeso, EI’s knowledge director, says organisations that manage energy use efficiently also enjoy improved productivity and reduced asset maintenance.
ExxonMobil and Ener-G have also recently jointly launched an Energy Efficiency Guide for manufacturers.
The companies recommend adopting an integrated energy strategy that includes smart metering and control, energy audits, decentralised energy generation such as combined heat and power (CHP), and switching to energy-efficient lubricants.
The guide also summarises the financial help available for implementing energy efficient measures such as CHP and offers guidance on compliance.
“Industrial energy bills can be reduced by as much as one fifth through simple, cost-effective measures to cut wastage,” says Chris Marsland, technical director for Ener-G.
“The latest research shows that inefficient energy production is costing the UK £9.5 billion per year, whereas decentralised energy production using CHP can achieve cost savings of up to 40% over electricity sourced from the grid and heat generated by on-site boilers.”
Both guides are available online.