Viewpoint: sniffing out a solution to foul food smells
4 Oct 2016
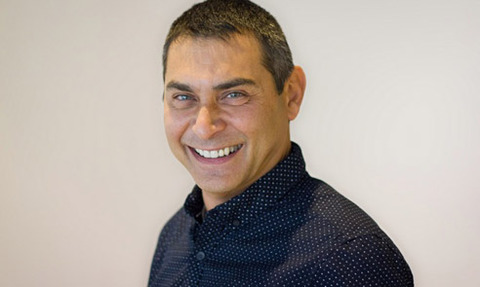
Foul odours caused by poor wastewater management can result in a variety of problems for food and beverage companies, explains NCH Europe’s Bernard Daymon.
Imagine that you’re showing a potential client around your food processing plant and they stumble across an area where there is an unsavoury smell. You know it’s not your produce – but they don’t.
Even if they did know that the smell was resulting from organic particulates decomposing inside your grease traps and drains, it could be enough to stop them making a purchase.
That scenario hints at just one reason why proper effluent management is vital for businesses in the UK food and drink processing industry.
Poor effluent management can also have a variety of other negative ramifications for food and beverage manufacturers, including blockages, increased costs and possible fines. Given the amount of sugars, fats, gums, milk, proteins and particles of food making their way into wastewater systems, it’s hardly surprising that there are challenges to overcome.
Poor effluent management can also have a variety of other negative ramifications for food and beverage manufacturers, including blockages, increased costs and possible fines
All these contaminants, along with high levels of biochemical oxygen demand, cause blockages, foul odours and overloads at wastewater plants.
These issues cost businesses money as a result of plant downtime, charges and fines from government or local authorities.
At times of high business activity, there is great pressure on effluent disposal, which can be detrimental to a business if this is not effectively managed.
Current wastewater legislation governs the disposal of all water used in production, washing and cooling facilities. Any business that intends to dispose of effluent is legally required to hold a licence to do so, as well as paying an annual fee, as determined by the levels of contamination in the water.
Many solutions to these issues don’t really help. For instance, trying to clear a grease trap by pumping will not prevent the build up of fats, oils and greases (FOGs) in the drain line. In addition, many biological products used to tackle effluent are dormant, meaning they require many hours to become active; others simply liquefy the waste and move the problem on.
Playing by the rules
This issue is becoming so prevalent that governments and local authorities are introducing stringent requirements regarding waste emitted by businesses into municipal sewers. This is due to the high levels of FOGs and dangerous chemical build-up in sewers that cost local authorities a lot of money to remove before they cause damage to the environment.
However, all of these issues can be easily addressed with live bacteria systems. Using this approach, naturally occurring bacteria is delivered directly into drains, grease traps and lift stations by computer-controlled microbial fermentation units that are installed onsite.
However, all of these issues can be easily addressed with live bacteria systems
The bacteria, which are active as soon as they hit the water, have the ability to easily break down complex carbohydrates, proteins, animal and cooking fats, oils and grease. Drain lines and grease traps can become easily clogged, in turn trapping decomposing waste and causing foul smells.
Filtration technology can also be slow to implement, meaning problems may take much longer to be resolved, resulting in increased odours and potential fines.
Meanwhile, live bacteria systems can be easily integrated with existing wastewater treatment equipment and can function effectively in space-restricted locations.
Such systems can be automatically and remotely controlled, reducing the need for constant surveillance and additional labour costs. It is, however, important to ensure that the bacteria have full National Sanitation Foundation approval for use in and around food processing areas to meet regulatory requirements.
By using an environmentally friendly answer to effluent management, food and drink manufacturers can save money, reduce charges, stop blockages and eliminate the bad smell left by inefficient alternatives.
- Bernard Daymon is chief executive of NCH Europe.