Waste & environment: the growing importance of emissions monitoring
1 Nov 2016
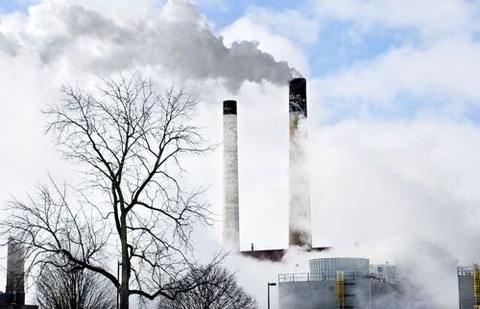
Tracking rogue emissions from industrial processes is becoming an increasingly high-tech endeavour, writes Louisa Hearn.
Falling foul of legal emission limits for airborne pollutants can soon add up to some hefty fines for those in heavy industry.
This means monitoring flue gases before they hit the atmosphere has become a necessary and often expensive procedure.
The common byproducts of core processes include the likes of NOx, CO, CO2, SO2 and Total Organic Carbons (TOCs), which are part of a growing list now subject to regulatory scrutiny.
From an environmental perspective, extensive monitoring and control of emissions can be easily justified. But from an industrial perspective, it often saddles companies with substantial extra cost for zero gain to the bottom line.
“In the emissions arena, no one is buying equipment to make money. They have to monitor their emissions or they will be fined,” says Dwain Waguespack, strategic accounts director at Emerson’s Rosemount division.
Anything that brings down cost has significant impact, especially for large plants that have to monitor emissions but need the highest accuracy and the lowest cost
Dwain Waguespack, accounts director at Emerson’s Rosemount division
To bridge this gap, continuous emission monitoring system (CEMS) specialists such as Emerson are rising to the challenge with next-generation analysis and control instruments to trim costs.
“Anything that brings down cost has significant impact, especially for large plants that have to monitor emissions but need the highest accuracy and the lowest cost,” says Waguespack.
In order to monitor their emissions, industrial operators traditionally extract them from a stack, and bring them down to where they can be measured, with each gas often needing its own analyser.
To lighten the load, Emerson has developed a range of analysers for accurate detection and analysis of numerous gases simultaneously. These are aimed at its core customer base in the petrochemical and chemical sectors where virtually all applications fall within hazardous rating areas.
Based on Quantum Cascade Laser (QCL) technology, Emerson’s CEMS was designed specifically for monitoring flue gases to gain regulatory compliance.
Legislative and administrative changes are needed for across stack measurements implementation to catch up. These legislators will need some time to adapt their systems to the current technology
“Cascade can also provide a wet and dry measurement, which eliminates a whole grouping of equipment used for handling it,” says Waguespack.
Unlike many products on the market, these systems can also be placed outside, so don’t require an expensive shelter, he adds.
“The next step forward would be to mount the laser analysers across the stack, so there is no extraction required.”
But while this capability is already available in Cascade, there is still no means to validate across the stack results in line with Relative Accuracy Test Audits (RATA).
“Legislative and administrative changes are needed for across stack measurements implementation to catch up. These legislators will need some time to adapt their systems to the current technology,” says Waguespack.
Continuous measurement
Other sectors where emissions must be closely regulated are biomass and energy-from-waste, where waste material is being used as a renewable fuel source to create energy.
Emissions monitoring provides important information on the combustion process, which enables operators to improve efficiency and demonstrate compliance with industrial emissions legislation, says Ken Roberts, managing director of Quantitech.
“In the UK, this means monitoring emissions 24/7 to prove to the Environment Agency that what you are emitting is below the emission limit values.”
The main gases the company’s analysers measure include HCl, HF, NH3 (ammonia), NO, NOx, SO2, CO, CO2, O2, TOC, formaldehyde and other parameters.
The key technology behind this measurement is called Fourier Transform Infrared Spectroscopy (FTIR), which has the ability to analyse such a large number of gases.
Quantitech also provides a range of specialist instruments for analysing specific pollutants.
“There is always someone needing to measure a single gas, in addition to other parameters such as particulates, flow, temperature and pressure,” Roberts says.
In the UK, this means monitoring emissions 24/7 to prove to the Environment Agency that what you are emitting is below the emission limit values
By continuously measuring their emissions, operators can raise alarms if specific gases approach their emission limit, so they can take appropriate action.
“Another way of reducing emissions is to conduct raw gas measurement, pre-abatement, which involves measuring gas levels within the process and using the measured output to optimise the process conditions, improve abatement and reduce potential emission events,” says Roberts.
As legislation evolves, he says there may soon be other parameters that need to be measured, such as dioxin, mercury, and isotopes of carbon as examples.
“Only when we have on-line isotope monitoring can we begin to measure rather than calculate carbon emissions related to the use of fossil and renewable fuel sources. However, development of this technology will depend on how carbon trading develops in coming years,” he says.
“Speciation of particulate size is another area of potential interest for regulators because the small-sized particulates are now understood to cause more damage to human health.
“If there were a system that could continuously determine particle sizing and mass, this could also be of great value.”
Damage limitation
Flue gas treatment (FGT) is one of the methods used in heavy industry to remove gases and pollutants before they are emitted.
A common FGT is for acid gas removal which works by targeting the components that are acidic and reacting with basic reagents.
“Reagents and absorbents produced by companies such as Lhoist, are commonly used in this process,” says Johan Heiszwolf, R&D director at Lhoist’s Environmental Applications Department.
“We produce basic reagents that react with acidic gases, but there are other types of pollutant that are not acidic but are still harmful to the environment, such as dioxins. For these pollutants we supply absorbents,” he says.
Changing landscape
“Because environmental regulations continuously evolve, Lhoist’s business model tends to change and adapt to the legislation,” says Heiszwolf.
“The first stage legislation typically targets reductions from the big polluters – for example SO2 reductions in coal-fired plants. Then regulators will move on to target smaller emitters.”
At a global level, Lhoist has also observed emission regulations evolving in a diverse way, often dependent on the region. For example, in the last 10 years China has made an enormous investment in flue gas treatment, says Heiszwolf.
“They have installed much more capacity than in the US, and what is also very interesting is that in China they locally have emission limits that are the strictest in the world.”
While European environmental regulations are considered quite mature, the US has recently been pioneering Mercury and Air Toxics Standards (MATS) regulations.
“Developments such as these have given rise to entirely new product ranges, such as a process and materials used to capture mercury by adding dry powder into flue gas,” he says.
“The application for mercury capture is really quite new, and in some areas of Europe they don’t even have regulations in place yet.”