Case study: monitoring is the key to water flow
22 May 2017
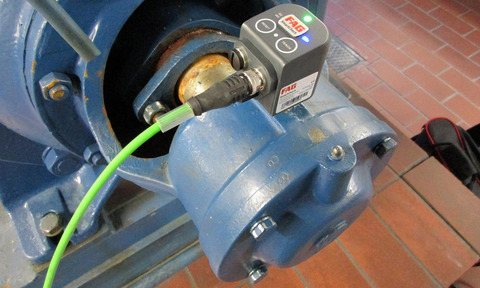
Standalone monitoring ensures bearing faults don’t result in a loss of water supply.
Perlenbach water treatment plant plays a key role as a supplier to residents in part of Germany’s Eifel region, close to the Belgian border.
The site provides fresh drinking water daily to more than 50,000 residents across seven municipalities, processing the equivalent of 2.4 million cubic metres of water per year to its consumer market.
Complex methods are required to ensure successful filtering and treatment in order to produce safe supply. Monitoring of machinery is therefore essential to ensure all round effectiveness.
A particular concern is pump monitoring: the plant includes two centrifugal pumps which owner, the Perlenbach water supply association, noted were producing increased levels of noise and vibration.
Our employees do not require any specific knowledge of vibration diagnosis. They can get started right away
Joachim Dankwardt, water treatment, Perlenbach water supply association
Both factors can indicate possible bearing defects in machinery and the possibility of wear and tear, leading to pump failure at a later date.
While the plant had a rigorous code of regular pump patrol monitoring, it was keen to avoid the prospect of several weeks of unplanned downtime that would interrupt Perlenbach’s regular water supply.
The association turned to the Schaeffler Group and its local partner KSA for a more effective remedy – replacing pump monitoring with a continuous online system that could effectively pre-empt any problems.
Schaeffler’s solution was the FAG SmartQB, a standalone system for monitoring the condition of rotating plant and equipment with fixed or variable speeds from 100 to 15,000 rpm.
It comprises a FAG SmartQB sensor unit, a cube-shaped housing with touchscreen display, and a cable for power and data transmission (Power over Ethernet).
Pre-configured for electric motors, pumps, fans, compressors, gearboxes and other rotating plant and equipment supported by rolling bearings, it is simple to install. Commissioning takes only five minutes and the automatic fault assessment feature means the technology can be operated by staff with little or no expertise.
it was keen to avoid the prospect of several weeks of unplanned downtime that would interrupt Perlenbach’s regular water supply.
The plant was keen to avoid the prospect of several weeks of unplanned downtime
“The FAG SmartQB is so easy to use that our employees do not require any specific knowledge of vibration diagnosis. They can get started right away,” comments Joachim Dankwardt, deputy manager, water treatment department at the Perlenbach water supply association.
The two pumps were fitted with SmartQB sensors to measure vibration and temperature, which were connected to one another via a FAG SmartQB. Next to the latter, a smart lamp illuminated red and the system activated an alarm if a bearing fault was detected.
Two clicks on the touchscreen display can provide maintenance technicians with details about each fault and also recommended actions. When changes occur in the condition of the equipment, the sensor automatically generates plain text messages on its 7-inch display.
Bearings in the plant’s eight-stage centrifugal pump were replaced in a short time and averted any likelihood of severe damage to the facility, reduced downtime and maximising plant availability, says Schaeffler.