Case study: solving a cereal packaging puzzle
17 Oct 2017
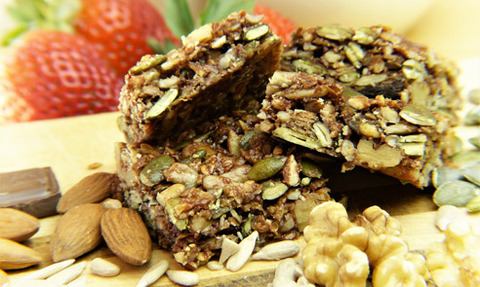
A cereals and cereal bar producer benefits from a fully-integrated packaging suite.
Dailycer, a manufacturer specialising in breakfast cereals and cereal bars for many leading food retailers, was seeking to increase production.
The company wanted to develop and install a complete cereal bar packaging line, comprising conveying of the product from the end of the cooling tunnel, through primary packaging, and onto secondary packaging.
Due to the different components in the line, effective inter-machine communication was vital. The rowdistribution system had to ‘talk’ to both wrappers, and both of the wrappers had to talk to a cartoner at the end of the line in order to achieve optimum throughput.
Westbury, UK-based MGE Automation supplied the major elements of the packaging system for the line, which included conveyors, row-distribution systems, buffers, two flow wrappers, a cartoner and conveyors around check weigher.
The primary benefits in this instance are based around the capabilities delivered by a connected and integrated control solution
Mark Gerrish, managing director, MGE Automation
To control this line, MGE turned to Rockwell Automation for its Integrated Architecture control solution.
Primary control products deployed across the line included Allen-Bradley CompactLogix programmable automation controllers (PAC) and Allen-Bradley PowerFlex variable speed drives on the conveyor systems; a CompactLogix PAC and Allen-Bradley Kinetix servo drives on the row-distribution solution; and Allen-Bradley ControlLogix PACs on each of the two high-speed flow wrappers.
The two (LH and RH) flow wrappers deployed at the Dailycer site were actually refurbished machines that had previously been equipped with a mechanical camming solution for motion. MGE Automation was able to replace the mechanical control elements with a Kinetix servo-based solution.
“We have undertaken these sorts of modifications many times in the past,” explains Mark Gerrish, managing director at MGE Automation.
“We have an intimate knowledge of the Logix programming environment and have become very adept at replacing cam-based systems with modern electromechanical hardware solutions driven by the very latest integrated control software.”
All about communication
The whole line runs on a Stratix-switch-managed EtherNet/IP communication network – equipped with Allen-Bradley POINT I/O modules – which also offers seamless communication back to the enterprise solutions and the all-important kitchen equipment, which was also based around an Allen-Bradley solution.
The use of an Ethernet/IP backbone and integrated hardware gives Dailycer the ability to exploit the benefits of The Connected Enterprise.
Indeed, future plans include the exploitation of real-time manufacturing data in order to make better decisions centred on planning and production metrics.
According to Gerrish: “As a completely new line, this was an interesting proposition as we had a blank canvas in the packaging area. This formed part of a larger blank canvas for Dailycer from the kitchen all the way to the end of the line.
“The primary benefits to Dailycer in this instance,” he continues, “are based around the capabilities delivered by a connected and integrated control solution.
“Throughput and efficiency targets were met and we could in fact offer Dailycer higher throughput if necessary. However, this would depend on the product being processed and would need to be balanced with the time required in the kitchen prior to packaging.”