Spirax Sarco solves metal refiner's carbon efficiency challenge
31 Oct 2017
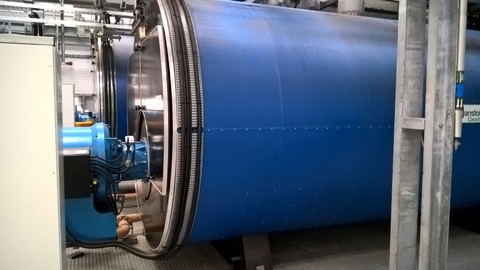
The precious metal refining industry notoriously consumes significant amounts of heat and chemicals to extract impurities from noble metals.
As a large user in chemicals and energy, Vale Acton was keen to boost efficiency and reduce carbon footprint. The refinery primarily uses steam for process heating but it is critical for production too. Most of its steam network was in the region of 45 years of age, which limited process efficiency throughout the site,
Production processes include reactor vessels, both coil and jacketed, which are used to control the temperature of reactants, heater battery and tank heating applications, unit heaters, direct injection systems and steam hose stations for cleaning tanks, vessels, and process equipment.
“The condensate return system was inefficient and costly to operate which was becoming a major issue, with corrosion to pipework, as well as inconsistent water and blowdown quality problems” says Vale Acton project manager Darren Matthias.
“We were using two boilers – one oil and one gas – to generate steam for the entire plant. Steam was generated in the boiler house at 3.8 bar g and the two boilers in question were operating at half the efficiency they should have been. This, coupled with an unreliable condensate recovery system, spelled a toxic combination of unsustainable operation and high costs”.
The perfect catalyst
Vale Acton’s steam system underwent a detailed audit, enlisting the help of Spirax Sarco which recommended a complete design and supply of new steam, condensate and cooling water systems which would help streamline our steam network and improve process and production cycles. New control valves, steam traps and condensate return units were fitted, with the addition of contamination detection systems.
“Since switching to gas we’ve already seen a 60 percent cost reduction and a considerable improvement in our operational efficiency. This has resulted in a faster process cycle and production levels
Darren Matthias, project manager, Vale Acton
Next, Vale Acton invited Spirax Sarco to carry out the design and supply of its boiler house, replacing the burners with two efficient gas boilers.
Two boilers fired only by gas were installed, as a more energy efficient and maintenance-friendly alternative to oil. The new boiler house is designed to allow a third boiler to be installed when Vale Acton are ready to increase capacity. One burner also allows the use of heat from a Combined Heat & Power (CHP) system.
“The new new boilers are consuming much less energy than before and are operating at approaaximately 95 percent efficiency. They have been fitted with an oxygen trim, which measures the gas emission in the flue and automatically brings it back in to line with our defined emission level when needed,” says Matthias.
New controls enable staff to monitor energy consumption. Data is now easily accessible, while improved visibility of energy consumption has allowed the company to track their environmental impact more effectively.
“By replacing the oil and gas burners with two gas boilers we have saved a significant amount in energy. We are achieving 55 percent less nitrogen oxides (NOx) emissions than we were from our old oil boiler and we’re also proud to be emitting zero sulphur oxides (SOx).
“Since switching to gas we’ve already seen a 60 percent cost reduction and a considerable improvement in our operational efficiency. This has resulted in a faster process cycle and production levels,” says Matthias.
Employees have been provided with an on-site Boiler Operation Accreditation Scheme (BOAS) course to ensure that safety and efficiency is always prioritised by staff.
Says Matthias: “By prioritising our impact to the environment we have also been able to advance production levels and protect the safety of our staff – something we simply can’t put a price on.”