How automated lubrication can help reduce product recall
31 Oct 2017
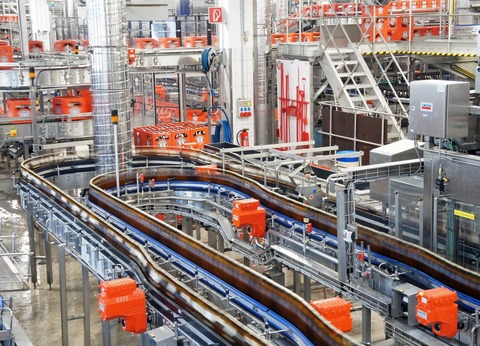
An automated centralised lubrication system can help food manufacturers avoid machine failure while cutting the risk of product contamination, explains Matt Preston.
Poor lubrication is one of the main reasons for machine component failure. When bearings seize up, the problem can often be traced back to a sub-standard lubrication regime.
Lubricating every relevant part of a machine is vital, yet doing it manually is time-consuming – and considered menial. Too often the job is given to junior employees, who will not have the necessary experience to carry out such a vital operation. One common problem is over-lubrication – which can be as harmful as under-lubrication – and it’s not only junior employees who make this mistake.
In the food and beverage industry, a further complication is the danger of product contamination, which would lead to a manufacturer’s worst nightmare: a product recall.
Automatic application
One effective solution is to install an automated centralised lubrication system. Here, all lubrication points – including inaccessible ones – are automatically re-lubricated with the correct lubricant, in the right quantity and at the right time. There is no need for an employee – junior or not – to walk around the entire factory carrying out manual lubrication.
But, switching to an automated system is a big decision. The process can start with a grease analysis, performed either by an external expert or by using a grease test kit. The kit helps a manufacturer take grease samples and analyse them to verify whether a lubricant is suitable for an application, for instance, or whether a grease has degraded to the point of needing replacement.
Central control
A typical centralised system comprises a central pump that delivers the lubricant around a network of pipes to each lubrication point. Metering, monitoring and control are also essential elements of the system, as they ensure timely, accurate lubrication – delivering enough lubricant for the needs of the machine, but no more. As well as maintaining machine reliability, this conserves grease reserves, and so helps to control costs.
A further complication is the danger of product contamination, which would lead to a manufacturer’s worst nightmare: a product recall
While centralised systems offer the most benefit to large operations – with thousands of lubrication points – they can be successfully implemented in smaller operations. For instance, a single – but vital – machine could be lubricated automatically, to ensure that it is always working at peak efficiency.
Filling time
One brewer, Erdinger Weissbrau, recently installed an extensive centralised lubrication system in its filling system – which has more than 3,000 lubrication points.
The sheer number meant that manual lubrication was out of the question. With SKF’s help, the company implemented a zoned system: the filling plant was split into different sections, with a centralised drum pump supplying a series of localised EDL1 (Electric Driven Lubricator) pumps – one for each section. Each EDL1 pump can increase an inlet pressure of 2 bar to an outlet pressure of 280 bar, to ensure that even distantly located points are supplied with lubricant.
The centralised system greases machinery and rolling bearings on conveyor belts, taking in two halls and a connecting tunnel. In total, three centralised drum pumps serve a total of 90 different zones.
By using centralised lubrication Erdinger has raised system availability and lowered lubricant consumption.
It’s clear that centralised systems take the guesswork – and grunt work – out of lubrication, leaving employees free to carry out other tasks, and ensuring more uptime for machinery across the plant.
Matt Preston is lubrication systems application engineer, SKF