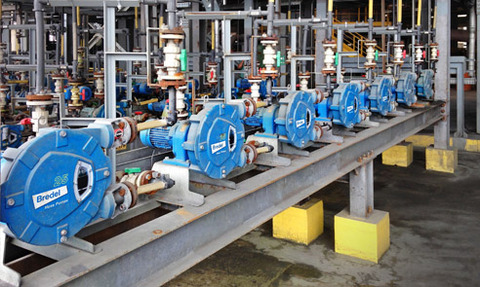
Difficult chemicals place particular demands on pumps and the systems that support their operation. Engineers need a touch of the detective, learns Brian Attwood.
However good any pump is and however well tested before leaving the factory, the real measure of it will be apparent only when it has had to contend with another variable: the context in which it must operate.
And, as The Pump Company’s Peter Staddon reminds, “it’s never just a case of one size fits all”.
Where difficult chemicals – aggressive or corrosive – are concerned, there are the usual considerations with which to deal: volume, speed, viscosity etc. In addition, there is the effect such products exert on the shelf life of equipment.
You’ve really got to think worst case scenario and what would cover all these products
Peter Staddon, The Pump Company
While the terms aggressive and corrosive are sometimes loosely used as interchangeable, there are differences of course. Rens Zwart, industrial sector business development manager at Watson-Marlow Fluid Technology Group, outlines: “To a pump, ‘aggressive’ can be a fluid containing a high percentage or sharp particles, slurries, suspensions or pastes for instance. Few pump designs will cope with abrasive wear without consequences.
“Peristaltic hose or tube pumps, however, can easily handle abrasives as the tube or hose wall ‘cushions’ the particles as they are pushed through. On the other hand, to a peristaltic pump, corrosives are any chemical that will attack the rubber hose or tube compound when in prolonged contact.”
In the process industries a wide range of difficult chemicals are employed. Lesley Eaton, business development and marketing manager at pump specialist Seepex, summarises her company’s range: “All chemicals and chemical compounds used in our main market sectors – water and wastewater treatment, food, beverage and pharma, oil and gas, paper and pulp.
“We regularly handle sodium hydroxide, sodium hypochlorite, phosphoric and nitric acid, and ferric chloride.”
In the industry overall, though, these will comprise numerous acids including both hydrofluoric and sulphuric, as well as alkalis and flammable liquids.
Safe handling, secure containment and efficient processing procedures, with a minimum of downtime, are key to successful usage.
Pumps form a vital component in this, so choosing the appropriate one for the task in hand requires a thorough appreciation of the demands that will be placed upon it, says Staddon [pictured]. Not always an easy job when a customer may be vague about the content to be handled.
“They’ll say ‘we want to pump this away to the tank and it’s waste acid’. We’ll ask what’s in it and they’ll try to tell you ‘there’s little bit of hydrochloric and a little bit of sulphuric…’ and we’re thinking, this is a mess,” recalls Staddon.
“So you’ve really got to think worst case scenario and what would cover all these products.”
Variable response
Identification of the product to be handled and its constituents is one of the prime considerations when deciding on equipment purchase. Not least because it will impact other factors determining pump choice, such as concentration and temperature.
With the standard operating temperature for most tubes and hoses spanning from -20°C up to 80°C, states Zwart, lower temperatures can cause the rubber hose or tube to go brittle; higher will deform the hose or tube to an extent that will affect volumetric accuracy and can weaken the wall of the tube or hose, causing splits or cracks.
Temperature, if not properly gauged, can impair the suction head, warns Staddon, who notes the example of some food companies operating self-priming pumps.
“They say it’s only pumping water and then complain it’s not working. You discover they had a full wash down with hot water going into the sump. With clean, cold water you’ll get a lift of seven metres. Raise it to 80°C in the sump and you’ll get one metre if you’re lucky, and it’s downwards from there.”
When it comes to the issue of concentration, Eaton points out it “will only affect the type of material selected for parts that come into contact with the chemical, and progressive cavity pumps can be constructed from a wide range of materials to ensure efficient operation”.
Concentration is however a crucial element when compatibility with tube or hose material must be taken into account, reminds Zwart [pictured], given that the rubber compound in a peristaltic pump is continually worked by the pump rollers, shoes or wipers.
And, adds Staddon: “It follows that if you have a greater concentration then you have a greater probability for either crystal growth or a change in the product.”
Should the result be a more abrasive product then, in general, for positive displacement pumps including peristaltic, the favoured option should be bigger and slower, he maintains.
One example of the latter was the pump his firm supplied for a clay pigeon manufacturer, whose products involve a careful mixing of pitch and French chalk. Too much pitch and the ‘pigeons’ shattered when leaving the traps; too much chalk and they remained impervious to gun pellets.
The solution was to run the mixing process at between just 30 and 40 revolutions a minute.
“They were delighted because they had been going through gears, bearings and shafts. It was grinding them to bits,” explained Staddon.
“What you really want is to make sure – because it’s viscous – that the velocity going through the pump is slower, because the slower the pump, the better the life of it.”
Think lifecycle
Extending lifecycle is not of course an end in itself, yet it will have a decisive influence on the success of the industrial process the pump serves. Working back from that premise affords a useful way to pinpoint the best machinery for the task.
Just as pump speed and size contribute to ensure success, so too does the choice of material in certain cases.
Says Eaton: “We select both elastomer stator materials and pump body and rotor materials based on a range of published data on materials resistance, together with empirical data from existing installations.”
In progressive cavity pump construction, she adds, materials such as iron, stainless steel, Teflon and alloys may be employed together with titanium rotors or ceramic coating. Where certain applications such as enzyme preparation in the food industry are concerned, some ranges are available without wetted metal parts.
We regularly handle sodium hydroxide, sodium hypochlorite, phosphoric and nitric acid, and ferric chloride
Lesley Eaton, business development and marketing manager, Seepex
Increasingly, stainless steel and other materials have displaced longer-standing options throughout areas of the process industry. Traditional materials, though, do still remain in use – for example, cast iron for handling sea water, although corrosion becomes an issue once an elevation in temperature is involved.
Plastic has proved particularly effective in overcoming the limitations of metals for some of the most challenging chemicals such as hydrofluoric acid, whose ability to cause damage on contact can go unnoticed initially.
One of Staddon’s largest projects involved a contract for a leading nuclear fuel company, for which there was no option: “They wanted to clean the sleeves on the containers with uranium bars in and they wanted to pump hydrofluoric acid. So we ended up with a complete plastic pump – plastic internals, plastic bearings… it was a fantastic job for a little company.”
For many pump firms the double demands of scaling up or innovating is an intimidating prospect and explains the reluctance of some to embrace ATEX-related projects. The approach, insists Staddon, remains the same: a careful consideration of the steps, going from A to Z.
Having identified these key contexts in which the pump must operate, the next requirement is to combine this information with an assessment of the overall system.
For the less experienced or novice engineer dealing with a company representative whose own knowledge is limited, achieving system conditions accuracy is inevitably more difficult and requires more guidance and less reliance on intuition and precedent.
A checklist of factors – flow, head and suction – needs to be supplemented by information about the materials being handled, specific pump location and the overall system.
“A lot of issues don’t derive from the pump as such but from the system and [firms have] not thought about it,” says Staddon.
False start
Likewise, companies can become fixated about certain aspects – insisting on larger centrifugal pumps when the cause of underperformance lies with the system overall.
False economies also prompt skewed decisions. Some buyers will opt for smaller, faster machines on the grounds of their cheaper purchase price – disregarding the inevitable costs further down the line for replacement or repair and unnecessary downtime.
Others, while embracing the principle that choosing the right equipment is essential for overall performance and investing wisely in a “critical” high value product, make no provision for the possibility of accident or product failure.
“Why would you have just one if it’s critical and particularly one that might take four to five weeks to replace – when even four to five days would be too much?” queries Staddon.
Finding what’s best for the client requires a marriage of engineering know-how with some informed sleuthing.
“You have to take it back to first principles, it’s down to your questioning technique,” advises Staddon.
“That’s what makes the job interesting because there’s a bit of intellectual rigour involved to solve problems – but if you do it, then you’ve got a customer for life.”