3D is revolutionising manufacturing for metal components
17 Apr 2018
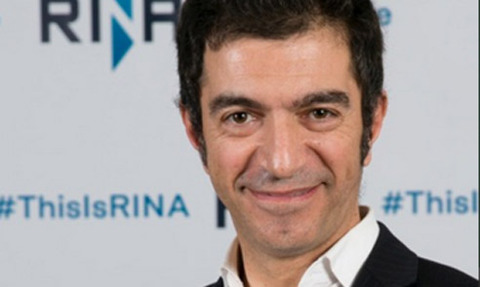
The way we manufacture is changing. Additive manufacturing (or 3D printing) is a quickly growing area that is removing previous component limitations bound by how a part needs to be machined, explains Guido Chiappa.
It is reducing lead times, lowering production costs and increasing manufacturing flexibility. Is it no wonder, therefore, that leading companies are investing in this technology for the future of their businesses?
Additive Manufacturing (AM) uses metals, composites or plastics typically in a fine powder form which are built up in layers to form a component. Although it may appear that the first step of embracing AM is to select a machine for the process, this is not the starting point. It must first be established how components or products are connected to the options enabled by AM. This dictates which particular AM process, and so machine, is required to best meet application needs.
The benefits of AM may include removing a production bottleneck, lowering the cost of machining a particular part, better optimizing a part that is constrained by machining, or even more general areas where greater flexibility in supply may help meet demand for small batches or easy customization.
One of the major appeals of AM is freedom from the constraints of traditional manufacturing processes. Geometries, ergonomics and overall design can be optimised along with the potential for reducing the number of manufacturing steps. This revolutionises component design, enabling geometries to place strength and integrity precisely where required.
Use of AM increases component reliability and helps assure quality; giving it particular appeal in industries such as oil and gas. Special metallic and alloy powders can be selected or developed to handle extremes in corrosion, pressure and temperature. Advancing technology is further enabling the production of larger component sizes and, along with support from advances such as Industry 4.0 and the Internet of Things, the application of AM is rapidly broadening.
Use of AM increases component reliability and helps assure quality; giving it particular appeal in industries such as oil and gas
In medical industries, there is widespread interest due to AM’s ability to create patient-specific, complex parts directly from a 3D CAD model. In the aerospace industry, AM is being used to improve the buy-to-fly ratio of metallic parts as well as for topology optimisation to create complex structures and reduce aircraft weight.
Through its Centro Sviluppo Materiali (CSM) business, RINA specialises in helping companies wishing to incorporate AM into their metal business. It can give independent advice to ensure best return on investment and trouble-free implementation of the technology with understanding of the composition of the powders and machinery options available.
Once the benefits of AM are identified, the next step is to consider what requirements are connected to the component and whether technology exists today to meet these or not. If not, can a special metallic or alloy powder be developed that will meet the needs of the component?
There are currently less than 30 metal powders generally available that cover a wide range of mechanical and chemical needs. RINA is able to develop, produce samples and thoroughly test new powders or AM processes for specific needs.
Furthermore RINA be releasing a guideline for the assessment and qualification of AM processes and products. Designing new metallic or alloy powders for use in AM is an iterative process based on existing material properties. Using state-of-the-art laboratories and production facilities, this then needs to be trialled in pilot production and the product tested to verify characteristics are as required.
As this exciting new technology continues to develop, the number of applications that will benefit from AM continues to increase. With specialist support, businesses can look to incorporate the technology into production lines with peace of mind that processes have been tested and validated prior to full-scale investment.
- Guido Chiappa is senior director industry, RINA