How Watson-Marlow boosted recycling plant uptime by 25%
28 Mar 2018
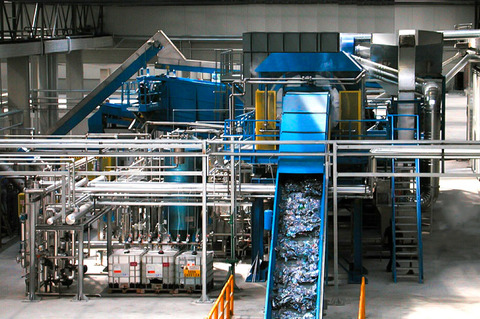
Montello SpA, a specilaist in sorting, recovery and recycling of post-consumer plastic packaging, as well as treatment, recovery and recycling of organic waste, wanted to reduce downtime and CO2 emissions at its plant in Bergamo, Italy.
At the company’s 350,000m2 site, waste is used to produce biogas from an anaerobic digestion process that in turn generates electric and thermal energy, as well as high-quality organic fertiliser.
The company uses pumps to feed the digester from buffer tanks. This is a high temperature and high flow (21m3/hr), 24/7 application. The sludge is viscous with high dry solids content (up to 60-70%), which can include sand – a highly abrasive constituent.
Pressure is a further issue: for safety reasons involving the production of gas, the digesters are located far from the plant, so the discharges are up to 100 metres distant.
The pumps were undersized when running at high speeds and subsequently demonstrated gearbox wear and hose life issues
As a result of these challenges, Montello’s existing pumps and hoses were falling short of expectations in terms of process uptime and operational costs, particularly when running at elevated speeds. In search of a solution, the company turned to Watson-Marlow Fluid Technology Group, requesting a trial of two Bredel 80 pumps.
The closed loop, speed-controlled pump, running against a discharge pressure of 5.5 bar, delivered an impressive process uptime by 25%, using NR (natural rubber) hoses.
In all, a total of seven Bredel 80 hose pumps from Watson-Marlow Fluid Technology Group replaced competitor models on buffer tanks feeding the digester at a major Italian recycling plant
The process provides significant reductions in CO2 emissions. The Montello plant alone achieves annual CO2 savings of around 90,000 tonnes
With the new pumps and hoses in place, the customer now achieves a reliable process that offers predictable gas generation and known maintenance costs.
“This is a perfect example of the growing demand for pumps in waste recycling applications,” says Pietro Spagnolo, sales engineer at WMFTG.
“Fermenting biowaste is the current focus of many recycling companies and energy producers in Europe, as the process provides significant reductions in CO2 emissions. The Montello plant alone achieves annual CO2 savings of around 90,000 tonnes.”
Installed capacities in biogas plants fermenting municipal and industrial bio-waste will increase from 900 MW in 2014, to around 1,750 MW in 2023, explains Spagnolo.
He adds: “We expect the number of plants in Europe to grow from 800 to over 1,450 in this time, representing significant opportunities for Bredel hose pump technology.”
Montello is now looking at Bredel 65 pumps for further applications, this time on the pre-treatment prior to the buffer tanks.
Here, flow is 10m3/hr, and once again abrasion is proving a concern. The customer has spoken with experts at WMFTG, discussing the principal technology differences of Bredel pumps – namely the use of direct-coupled technology versus the close-coupled technology of the encumbant pumps.
The next stage will be the acquisition of a single Bredel 65 pump for use in a long term trial against existing pumps.