Hidrostal helps transform a 'worst performing asset' into an efficient pumping station
25 Jan 2018
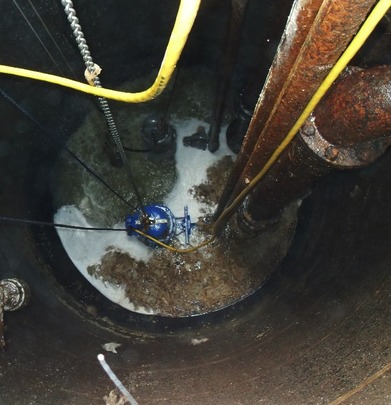
Braintree Marks Farm Terminal Pumping Station in Essex, was a frequent bugbear for Anglian Water’s maintenance and standards performance team.
Regular large accumulations of rag-laden media plagued the station to such an extent that Anglian had adopted an operational approach whereby the blanket of rags was strategically controlled between two levels in order to avoid the potential for blocking the current pumps installed.
Frustratingly however, the pumps still blocked, and wet well cleans were increased to once a month to prevent flooding of the well in the event of it becoming temporarily inoperable.
As a result, Braintree was deemed a ‘worst performing asset’ pumping station - that is, one identified with repeated reactive maintenance costs far outweighing the initial purchase cost of the pump unit.
Hidrostal had worked with Anglian Water on similar poorly performing pumping stations and resolved their issues for them by trialling a Hidrostal pump at the troublesome sites.
“There was an installed power saving of 2.5kW and almost twice the solids handling capability”
It was apparent that Braintree TPS was a fitting candidate for trial and assessment, so Hidrostal worked with Anglian Water to select an 11kw pump for the site.
Hidrostal’s single screw centrifugal impeller design was chosen because of its increased free passage capabilities whilst retaining a high level of hydraulic efficiency.
Braintree TPS is a twin pump wet well station on a duty / standby alternating cycle mounted on guide rails for permanent installation. The Hidrostal replacement pump was retrofitted with minimal disruption to the existing installation.
The Hidrostal centrifugal screw impeller was chosen for an initial trial to run for a period of 90 days, whilst one of the originally installed pumps was retained for comparison.
On completion of the trial, the Hidrostal pump was shown to have performed best overall, with no blockages.
Results indicated Hidrostal provided a more reliable, robust pump which is better suited to sites with high rag/solids content and could reduce or eliminate ragging issues.
In direct comparison to the pump model it replaced, there was an installed power saving of 2.5kW and almost twice the solids handling capability on free passage throughput.
After a further extended period of operation over 12 months, the decision was made to leave the Hidrostal pump in place and purchase another unit.
The telemetry systems and data collected helped identify which, how often, and what contribution each made in terms of running time, blockages and energy consumption.
Statistics demonstrated that this particular selection provided additional benefits to the site operation which resulted in lower pumping kW/hours per day for an equal number of start cycles, minimal variation in forward flow and less effect on performance through wear due to the steep hydraulic curve design.