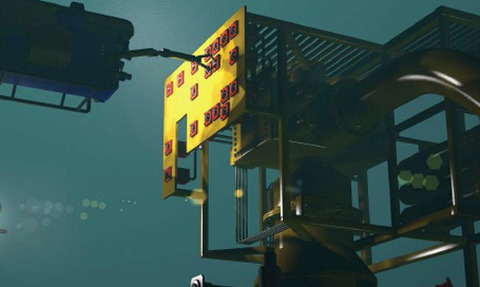
The future of oil and gas depends upon recruiting more millennials as engineers. The sector’s failure may be down to perception rather than reality but that still matters, argues Brian Attwood.
The Royal Academy of Engineering’s #ThisIsEngineering campaign highlights, as others have done, the annual demand for thousands of engineers and technicians with core engineering skills, plus many more additional roles requiring an element of engineering skills.
Yet, recruiter Matchtech’s Voice of the Workforce, 2017: A report on the current perceptions and ambitions of the engineering community identified clear differences in the way that ‘modern’ sectors such as recycling were viewed, compared with traditional areas such as oil and gas.
Renewables was seen as a clear growth area by 42%, with power generation scoring 28% in second place. Oil and gas meanwhile scored a mere 14%.
Likewise, while renewables topped the list of sectors with an improved year on year reputation, oil and gas had a massive lead among those sectors whose reputation had not improved but fallen.
The industry is embracing new data-driven technologies, such as robotics and the Internet of Things, which are fundamentally changing the way operations are conducted…young people are well placed to apply their skills in this industry
Chris Claydon, chief executive, ECITB
While this may have mattered less during the sector’s era of retrenchment, the pickup in oil’s fortunes mean a new recruitment cycle is beckoning.
The negatives associated with oil and gas may be more perceived than real but operate as powerful deterrents, acknowledges Chris Claydon, chief executive of the Engineering Construction Industry Training Board (ECITB) which, together with the Offshore Petroleum Industry Training Organisation (OPITO), manages the UK Oil and Gas Technical Apprentice Programme (OGTAP).
Says Claydon: “There has certainly been concern that the recent downturn in oil and gas has conveyed a negative message about the industry being in decline and that this has undermined the attractiveness to new recruits. Many young people might hold negative preconceptions from an environmental perspective too, which is something that the industry is taking steps to address.
“In certain parts of the UK such as Aberdeen, awareness of the career opportunities in oil and gas is strong. However, the industry isn’t widely understood nationally, nor is the fact that it offers highly-skilled careers with key transferable skills.”
Chief among the challenges for oil and gas is that it is easily perceived as traditional in terms of its tasks and skillsets, but also in terms of a company culture that is represented as overly hierarchical, lacking in diversity and risk averse. And for a generation brought up on notions of environmental awareness, fossil fuels remain a hard sell.
The 2017 World Economic Forum report Digital Transformation Initiative notes ruefully that millennials, projected to constitute most of the US workforce by the early 2020s, currently favour working in industries perceived to be ‘greener’ than oil and gas.
It has not helped that a lack of diversity in its workforce has limited the sector’s recruitment pool from the outset.
This point has not been lost on ECITB and OPITO who have recently campaigned for a greater proportion of females and ethnic minority applications for the swathe of apprenticeships OGTAP will offer this year.
“This year we expect to recruit around 55 apprentices and we’d really like to see more females and people from ethnic minority groups applying, as these communities are under-represented in both the offshore population and OGTAP,” says Alix Thom, workforce engagement and skills manager with Oil & Gas UK, and former chair of the OGTAP Steering Group.
The experience of firms such as BHP Billiton in the mining sector demonstrates that traditional male-dominated heavy industries that have previously failed to recruit female recruits can transform. It succeeded in boosting the number of women employed at all levels by 3% in a single year, combining directives and increased reliance on remote control and automation.
Tellingly, OPITO’s 2017 conference included a keynote speech from the author and pundit Ryan Jenkins on the particular challenge of hiring millennials; the demographic that the industry needs most in order to safeguard its own longevity.
The crux of Jenkins’ argument is that reaching and recruiting the millennial generation requires a different approach and mindset. That provides a greater challenge for companies with a legacy culture and established way of working; for, as is often pointed out, the sort of risk taking favoured in Silicon Valley sits less well in sectors which place a high premium on predictability.
Recruits can now experience certain work scenarios which enable companies to break preconceived ideas about a position or an industry. The feeling that one gets from being able to put a plant back online after a failure is easier communicated through digital media
Youssef Mestari, program director, Honeywell Connected Plant
While earning potential still ranks highly, company culture and the opportunity for innovative, project-based work have risen in significance markedly.
When it comes to what marketeers dub the ‘decision funnel’ –the process by which promising students do or do not opt for engineering – the role of parents and teachers has declined markedly in favour of search engines and social media.
Research carried out by YouGov on behalf of the #ThisIsEngineering campaign revealed 51% of 13 to 18 year olds surveyed relied on the internet, compared with just 37% seeking advice from school.
Youssef Mestari, program director, Honeywell Connected Plant, explains: “Recruits no longer just go to a job board website and apply. They first do research on sites where actual employees of the target company speak about their jobs.
“Social media allows companies to attract recruits while they are in their personal space and not necessarily during their actual job search. In that way, the touchpoints between companies and recruits have changed dramatically thanks to online analytics customising ads to specific interests, geographies, etc.”
While some companies such as Honeywell and BP boast a sophisticated social media and online operation that emphasises innovation and sustainability, many more do not.
Different perspective
Likewise, employment expectations are centred less around seeking a career to fit into; more about finding work that aligns with their interests. Naïve and idealistic this may appear but, as demand for engineers and technicians will vastly outstrip supply, the likelihood is that it is oil and gas companies that will need to change rather than their recruits.
Fortunately, those aspects most likely to attract millennials – technological innovation, project working/agile teams, transferable skills, sustainability – align clearly with the way in which the sector acknowledges it needs to develop.
“Through videos for example, recruits can now experience certain work scenarios which enable companies to break preconceived ideas about a position or an industry. The feeling that one gets from being able to put a plant back online after a failure is easier communicated through digital media,” says Mestari.
Of four areas cited by the WEF 2017 report, three are pertinent: digital asset lifecycle management, integration of digital platforms and greater digitalisation of energy systems. In the United States alone, says the WEF, these would have additional value to the sector of $845 billion.
In practical terms this comes down to automation combined with data analysis, harnessing virtual reality for what the director of industry value engineering, oil and gas and utilities at SAP India Anseel Nubari typifies as a “data-led virtual view”.
WEF statistics suggest 36% of oil and gas companies are investing in Big Data and analytics. Yet just 13% use this to inform their commercial approach towards the market and their competitors, suggesting the willingness among C-suite executives to embrace change founders on lack of knowledge as to how to apply it strategically.
For an industry focused on the need for predictability, breakthroughs such as robotics, additive manufacturing, drone and HoloLens technology, allied with real time data, offer advances in cost and efficiencies. They are also powerful drivers for millennial recruits.
Bristol-based Rovco, bolstered by funding from Innovate UK, intends that its development of underwater robots capable of live 3D scans will positively impact inspection and decommissioning expenditure. Estimates suggest this could be by as much as 80% when integrated with artificial intelligence (AI).
Says ECITB’s Chris Claydon: “The industry is embracing new data-driven technologies, such as robotics and the Internet of Things, which are fundamentally changing the way operations are conducted.
“This will increase the demand for high-level digital skills across all roles, from mechanical engineers to designers and project managers. As a generation that is typically accustomed to using new digital technologies, young people are well placed to apply their skills in this industry.”
Real-time data provides a means of increasing the proportion of remote working, especially offshore. This increases personnel safety by ensuring less human involvement on-site and more targeted activity when it is necessary. It can also ensure more control of equipment, varying drill speed and pressure, for example in order to maintain equipment.
As digital transformation is being rolled out and becomes more embedded in the processes, we will see new skills are required for new roles like data scientist, machine-learning or 3D-printing expert. Because of that, there is a need to develop agile competency programs and new learning methods
Meanwhile increasingly sophisticated virtual reality (VR), 3D imagery and modelling have increased the opportunity to test design faults before they are identified in the field. California-based PG&E has invested heavily in VR to boost its audit of thousands of miles of distribution lines.
HoloLens technology allied with platforms such as ArcGIS provides opportunity for a 3D depiction of oil reserves for prospective, new and diminishing wells, with the added advantage that individual team members can view the results simultaneously while in different locations.
Still underused and biologically-inspired convolutional neural networks (CNNs), employing image, video, sound, text and time-series data, offer better accuracy levels and can contribute towards safer operations.
At a more developed stage, Shell’s use of 3D printers effected a $40 million saving for the company when designing its Stones station in the Gulf of Mexico.
Producing a scaled-down version of the site in one month highlighted improvements needed for components ahead of construction, identified the most efficient assembly procedure, and provided evidence to secure government approval for the project.
Opportunity knocks
The sector’s difficulty may in fact be less one of what it has to offer the millennial engineer in terms of challenge and innovation; more one of how it markets that offer to the uninformed.
That, suggests Claydon and Mestari, may mean less focus on narrow job and sector specific skills and more attention to occupational ones – an approach ECITB and Honeywell have promoted respectively with the Connected Competence initiative and Honeywell Connected Plant Skills Insight.
States Mestari: “There is a focus on developing a workforce with transferable skillsets in-house. As digital transformation is being rolled out and becomes more embedded in the processes, we will see new skills are required for new roles like data scientist, machine-learning or 3D-printing expert. Because of that there is a need to develop agile competency programs and new learning methods.”
Both agree that the onset of IIoT does not mean fewer but different opportunities. As Mestari puts it, “unmanned operations of an oil platform not only imply a safer work environment, but overall improved work conditions”. The job still needs to get done, but now can be done remotely, without having to be away from home.
Concludes Claydon: “As many companies are now diversifying their portfolios, it is more important than ever that their workforce possesses transferable skills. The skillsets of an electrical engineer in oil and gas versus one in offshore wind are in fact largely the same – the difference being the environment in which they work.”