KSB enables Mumm producer to service drinks market
16 Mar 2018
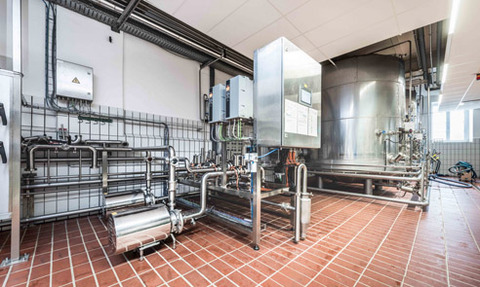
Rotkäppchen-Mumm’s Eltville site in Germany’s Hesse region produces the new product Mumm Dry Alcohol-Free for the premium sparkling wine market, bottling around six million litres of the alcohol-free beverage every year, to cater for rising demand.
The company also produces an annual eight million litres of wine-based mixed drinks, such as Rotkäppchen Fruchtsecco, in various flavours.
Initially, the plant was configured to produce large quantities of alcohol-free sparkling wine. But on the back of its success, more varieties of Rotkäppchen Fruchtsecco have since been successfully launched to market.
The same system now produces both larger and smaller quantities as required. With the market for beer-based mixed drinks or fruit-flavoured sparkling wines increasing, alcohol-free, beer-based mixed drinks are becoming more popular as alternatives to traditional alcohol-free beverages.
Special attention had to be paid to ensuring that all pumps employed hygienically suitable designs.
However, juices and sugar added to mixed drinks can create a fertile breeding ground for bacteria. Such processes thus require extensive experience and attentiveness on the part of operating staff.
“Process technology is required to react extremely flexibly, as quantities can fluctuate massively depending on what flavour is in demand,” says Rene Kopp from Sales - Life Sciences Applications at KSB. “After all, sales quantities rarely reach the per-head volumes associated with traditional beverages.”
This demands extreme flexibility from pumps, tanks, piping systems and automation. While traditional sparkling wine is protected against contamination by its high alcohol content, this effect is not present in alcohol-free variants.
The pumps used in the plant were planned and selected by InfraServ Wiesbaden (ISW Technik) and KSB, working in collaboration.
Special attention thus had to be paid to ensuring that all pumps employed hygienically suitable designs. They also required CIP compatibility, i.e. the ability to operate with acid and alkaline media and withstand high temperatures. In the new production system’s tank farm, twelve Vitacast pumps transport wines and alcohol-free drinks between the tanks, and to the filling systems.
Here they have to comply with technical, automation and quality requirements encompassing pressure, temperature and flow rate.
“As demand is subject to fluctuation, all pumps are fitted with frequency inverters. The PumpDrive smart frequency inverter, which is combined with an IE5 synchronous reluctance motor, continually adjusts the speed to the actual demand of the system,” says Kopp.
As a result of the system’s extensive use of automation, all pumps are also equipped with a PROFIBUS PA interface.
Hygienic design plays an especially important role when selecting pumps for alcohol-free drinks or beer-based mixed beverages. But that is not all: Supporting innovative processes also requires exceptional flexibility so that production quantities can be matched to the market’s demands.