A guide to picking the right blower for wastewater aeration
12 Jun 2018
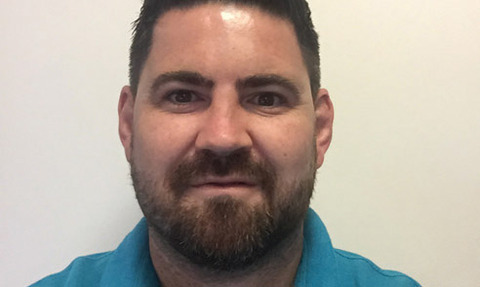
Aeration is a key process within wastewater treatment plants, forming the secondary treatment stage after solids have been removed.
The blower plays a big part in this process because it provides the air supply that metabolises organic compounds in the wastewater and removes carbon dioxide, explains Adam Bond.
The main elements to consider when choosing the most suitable blower are total cost of ownership, efficiency, turn-down capability and maintenance requirements, in addition to the pressure, flow and size of your plant.
In a typical wastewater treatment plant, blowers account for only 10 per cent of capital expenditure. Due to operating expenses, however, they can represent 40-80 per cent of the energy used at a treatment plant. Therefore consider lifetime cost.
Non-contact blowers often have the lowest total cost of ownership due to high efficiency and lack of frictional damage. The air bearing blower has the added bonus of being entirely automated, thus requiring little operator intervention, and can achieve high bearing lifetimes if triple nano silver coatings are used.
Integral gear type centrifugal blowers arguably have a higher cost of ownership because the control system is complex and expensive and requires more plant space and good ventilation, as it can emit a high amount of heat, noise and vibration.
Wastewater treatment plants reap the long-term benefits of improved efficiency and reduced operational costs.
Blowers use a considerable amount of energy in wastewater treatment and must match the size of plant and varying conditions. To understand the potential payback period, read the manufacturer’s guidance on how well they transfer the energy power into air power and consider turn down capability for different operating conditions.
Direct Drive Turbo Blowers offer excellent efficiency because the turbo impeller is connected directly to the shaft, which makes it possible to eliminate all transmission losses. They use motor and variable frequency drive technology, which transforms 50 or 60 Hz of supplied power into high rotating frequencies.
Positive displacement screw and lobe blowers often see efficiency losses through their transmission, motors, gears and variable frequency drives. Both lose efficiency through increased pressure, although screw blowers are often more efficient than lobe blowers, which have no internal compression during the 360-degree rotation cycle.
Turndown is essentially a blower’s ability to reduce its air flow rate to meet demand, taking into account the maximum and minimum blower or system flow rates. It is important to gauge how a single blower or group of blowers is able to satisfy a change in future air demand.
Positive Displacement lobe blowers and screw blowers are renowned for their reliable turn-down capabilities when sized correctly due to their simplicity and are applicable to medium and small flows.
Consider how frequently repair and maintenance is required, how complex it is, and ultimately if it is more economical to repair or replace.
Non-Contact Air Bearing Blowers do not require additional backup systems, are not negatively impacted by power failures, and are self-controlled with no need for any safety devices to protect the bearing.
Integral Gear Type Centrifugal Blowers, used for higher flows, require considerable upkeep due to their flow inlet guide vane (IGV) and variable diffuser (VD). These components contain several mechanical parts requiring maintenance and the control system required for their operation is often complex and expensive.
Non-Contact Magnetic Bearing Blowers can demand an intense maintenance regime because they use active magnets to position the motor rotor in the right position during both operation and at standstill. Despite offering good levels of efficiency and significant turn-down capability, constant monitoring of the rotor position means that this technology is sensitive to power failures. Overall, the technology is affected by higher temperatures and requires several backup systems and control functions.
Positive displacement lobe blowers and screw blowers both have moderate repair and maintenance requirements but, due to their high levels of vibration, screw coatings can wear away and, over time, will need to be replaced.
Best practice combines a customer’s knowledge of the application with the equipment provider’s knowledge of the blower technology: Wastewater treatment plants reap the long-term benefits of improved efficiency and reduced operational costs.
Adam Bond is sales manager, biological treatment at Xylem