Thickness profile measurement system provides Liberty from manual approach
18 Jul 2018
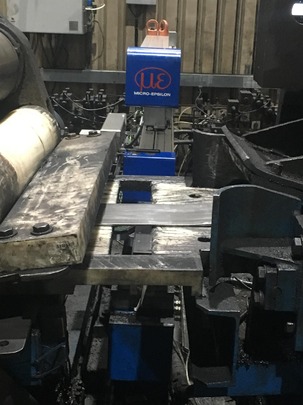
Liberty Speciality Steel produces high value, precision-engineered alloy and stainless steel products for use in demanding sectors such as aerospace, oil and gas, bearings and industrial engineering, as well as bright bar and narrow strip for customers around the world.
Rolling specialty steels remains a challenging process, explains Andy Spalding, works engineer at Liberty Speciality Steel (narrow strip) in Brinsworth:
“The strip materials can quickly wear the rolls, which in turn, affects the profile gauge of the strip.
“In order to minimise the effects of roll wear, we used to roll a maximum number of slabs, between 18 and 22 before the rolls would need changing.”
Hands free
Until late 2016, the company was manually inspecting strip, using micrometers by taking measurements at various points across the strip.
To improve its processes, Liberty Speciality Steel considered various thickness measurement systems, including both contact and non-contact systems, before it settled on Micro-Epsilon’s thicknessCONTROL C-frame system.
By combining highly efficient signal processing algorithms and visualisation software, the system is able to achieve accuracies in the single micrometre range
Glenn Wedgbrow, sales manager at Micro-Epsilon UK remarked: “Due to ever increasing manufacturing tolerances in metal strip production, the need to find higher accuracy, inline measurement solutions is accelerating.
“Micro-Epsilon’s range of robust, complete turnkey measurement systems offer distinct technical advantages in terms of measurement accuracy, thermal stability and reliability.”
Part of Micro-Epsilon’s thicknessCONTROL MTS 8202 family, C-frame systems measure the thickness profile of flexible metal strip.
Said Spalding: “Although most thickness measurement systems can handle the manufacturing tolerances that we work to, the strip does have a tendency to oscillate slightly as it’s being processed, which can affect measurement accuracy.”
C-frame systems can be installed in hot and cold steel rolling mills, as well as slitting, coating, casting and cutting lines, providing reliable, high precision measurement results that creates a basis for controlling the production process and product quality.
Engineering precision
The measurement system installed at Brinsworth uses two scanCONTROL laser profile sensors that are integrated in the upper and lower arms of the C-frame. The thickness of the strip is derived from the distance between the two sensors and the resulting signals. By combining highly efficient signal processing algorithms and visualisation software, the system is able to achieve accuracies in the single micrometre range.
Said Spalding: “We worked closely with Micro-Epsilon to devise a C-frame mounting arrangement that utilises a series of plastic wear plates that help to restrict the movement of the strip to a maximum of 60mm as it’s being rolled. This means our measurements are reliable and accurate.”
Employing the system, the firm can analyse the measurement data and make a decision whether to extend the number of slabs beyond 22, before the roll wear will start to affect the final quality of the strip produced he explained.
“We’re now using [it] to measure not only the thickness profile across the strip, but also three key quality parameters: the crown, the wedge and the edge drop. The system enables us to continuously check that the thickness profile and the key parameters are meeting the customer’s specification.”
Spalding said the capability of the profile measurement had enabled changes to meet the demands of the customer whilst also increasing productivity, enhancing customer-supplier relationships.