How Landia enabled a first for Ireland's biogas pioneers
25 Jul 2018
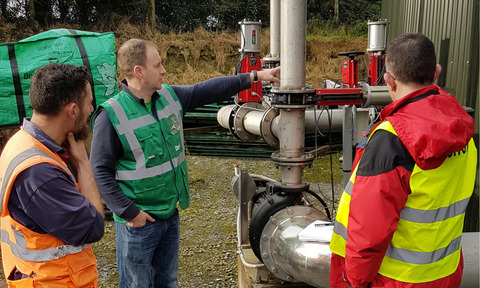
Landia chief the late Hugh Vaughan left a lasting legacy when he helped a father and son team create the Irish Republic’s first farm-scale biogas plant, which continues to expand to this day.
Farmers in European Union member states have been increasingly subject to the Nitrates Directive, which aims to sustainably protect ground and surface waters from nitrates derived from agricultural fertiliser use.
The McDonnell family farm in Limerick, Republic of Ireland used large volumes of fertiliser costing €100,000 annually, so the implications of the directive were felt keenly.
“We wanted to look at how we could produce our own, better, eco-friendly fertiliser, which at the same time for us was a natural progression for the farm,” explained David McDonnell, who runs the farm with his father Michael.
“We wanted to use the land as best we possibly could - and ensure that what came out of our AD plant could be put onto our land”.
Breaking new ground
After extensive research that involved site visits to Scandinavia, Germany, the USA and Australia, the McDonnells embarked on creating the country’s first farm-scale AD and biogas plant for renewable energy use.
German company Kreig & Fischer provided design input for the new GreenGas site, while Kirk supplied the first digester. The latter also recommended Landia for the mixing systems, specifically the company’s GasMix system.
After extensive research they embarked on creating the country’s first farm-scale AD and biogas plant for renewable energy use
When it looked as if the results might fall short, Landia UK director Hugh Vaughan came to the rescue. He paid a personal on-site visit, diagnosing a build-up of sulphur that he rectified by back-flushing the pipework. Digestate was forced up the reverse and quickly cleared the pipe.
Back-flushing has now been adopted as part of the GreenGas maintenance programme. Efficient mixing systems ensure that Gas Mix – which combines a Landia chopper pump and venture nozzles – needs to run for just 15 minutes out of every 150 minutes. Side entry mixers (for extra impetus when required) need to run for just five out of every 60 minutes.
The benefits of the AD venture for the commercial health of the farm have been clear, says McDonnell.
Commercial and ethical
“Thanks to our AD operation, our annual fertiliser costs have now been reduced to one third. In the future we can hopefully look at converting our digestate into a marketable product.”
GreenGas is now a 1MWel plant, having added a new 1800m3 digester (from Wolf-Austrian) and being supported by nearly two dozen Landia products.
Adds McDonnell: “With 23 of its pumps and mixers on site, Landia’s very robust and reliable equipment has certainly played its part in the growth, wellbeing and efficiency of this plant.“
GreenGas also uses a Landia pasteuriser, switching this from the front to the back end of the process: it was more efficient, process-wise, to increase the temperature of digestate already at 40 degrees to the required ABP pasteurisation of 70 degrees - rather than wait for it to be heated up from an ambient storage temperature of only 6-10 degrees.
Excess heat generated is used for the plant and for the poultry sheds on the farm, explains plant manager Senan Meade, who concludes:
“It’s all about getting the balance right and fine-tuning so that you hit the sweet spot for a smooth-running plant. We have alarms in place and can keep a very close eye on things away from the plant on our smartphones.
“Even after all this time, we’re still learning – constantly”.
Photo: David McDonnell (centre) with GreenGas plant manager Senan Meade (left) and Paul Davies of Landia (right)