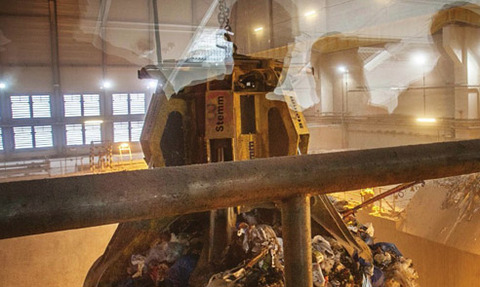
Smarter measurement technologies are coming to the aid of food and drink manufacturers under pressure to reduce waste, writes Louisa Hearn.
Political and economic uncertainty coupled with rising raw material and energy costs are taking their toll on the UK’s largest manufacturing sector.
The Food and Drink Federation (FDF) recently found that a triple whammy of rising ingredient, packaging and energy costs had a large impact on food and drink businesses in the second quarter of the year.
On top of this, the shadow of a ‘no deal’ Brexit “looms large over business confidence amongst the UK’s food and drink manufacturing industry”, says FDF chief executive Ian Wright.
Waste management, however, is one area where UK manufacturers can throw some caution to the wind in the quest to find new and ingenious ways to trim costs — and even source new streams of revenue.
It starts with accurate and targeted conformity and contamination testing at the earliest stage in the production process, ensuring that only non-compliant batches are returned to suppliers
Russell Morgan, product inspection specialist, Mettler Toledo
Large reductions in the amount of waste sent to UK landfill have already been achieved, says the FDF, with its most recent research indicating that participating members had reduced the amount of food waste sent to landfill to effectively zero by 2015.
“Between the first FDF waste survey carried out for the year 2006 and 2015, it is estimated that FDF members diverted approximately 800,000 tonnes of food and packaging waste from landfill,” says Helen Munday, chief scientific officer at the Food and Drink Federation.
Its 2015 survey revealed the most popular alternative waste treatment methods for food waste were landspreading (76%) and for mixed waste many had adopted thermal treatment, with energy recovery (65%).
While improved reporting may have contributed to these figures, Munday says that government policies such as increases in the landfill tax — now set at about £89 per tonne for food waste — have incentivised this shift.
Munday says that an increase in the number of de-packing services offered by AD operators and some feed mills was also “likely to have had a significant effect on the waste prevention and treatment options available for the mixed packaging and food waste material stream”.
In addition to physical waste, repeated line stoppages to clear reject bins and troubleshoot machine issues can undermine the cost effectiveness on production lines
Phil Brown, European managing director, Fortress Technology
Going forward, however, she says waste reduction efforts are now being focused further up the “waste hierarchy” with many companies now targeting manufacturing processes themselves.
According to WRAP, a non-profit organisation tasked to support resource efficiency in the food and drink sector, the key culprits when it comes to waste in food and drink processing include: machinery performance problems, such as product blockages and mechanical mishandling; poor quality production – including over or under baking and inaccurate weighing; and not reusing or repurposing offcuts such as pastry trim, bread crusts, tomato ends and vegetable peel.
Equipment makers are stepping up to these challenges with an array of new technologies to better control or measure the flow of materials throughout production.
Russell Morgan, product inspection specialist at Mettler Toledo, says food manufacturers are keen to extract the maximum amount of product from the raw ingredients that come into their facilities.
This makes inspection systems based on x-ray, metal detection, checkweighing and vision technologies, useful tools for streamlining processes.
“That starts with accurate and targeted conformity and contamination testing at the earliest stage in the production process, ensuring that only non-compliant batches are returned to suppliers,” he says.
Further downstream, he says challenges can arise around packaging and labelling integrity. “For example, caps on sauce bottles must be fully secure and there can be no meat trapped in the seal on a pack of minced beef.”
Automated quality checks using x-ray, checkweighing or vision inspection technology can reduce the likelihood of such nonconformance in packaging and labelling, he says.
False rejection – where contaminants are signalled but not actually present – is another common cause of waste, with product effect from wet products like meat and poultry particularly challenging for traditional metal detection technology.
He says Mettler Toledo’s Profile Advantage system was designed to overcome false signals, and boost accuracy in detecting smaller, irregular-shaped metal contaminants in more challenging applications.
The Bury Black Pudding Company uses the system to inspect packaged products including large pudding rings and frozen slices, in a bid to overcome this phenomenon.
The company says this is because both characteristics — size and frozen state — can present a potential challenge for traditional detection technologies.
Phil Brown, European managing director of Fortress Technology, says equipment choices, robust quality control processes and staff training are all critical factors when it comes to reducing factory food waste.
“If anything, production lines today need to be faster, accommodate quicker product changeovers, recalibrate at the touch of a button and provide suppliers with assurance that contaminants haven’t slipped through the net,” he says.
Problems on the line
Adding up the amount of product wasted due to false rejects can be challenging, but he says industry estimates put the cost per line at up to £14,000, depending on the scale of the problem.
“In addition to physical waste, repeated line stoppages to clear reject bins and troubleshoot machine issues can undermine the cost effectiveness on production lines,” he says.
The company’s Interceptor metal detector applies both high and low-frequency ranges in order to isolate the product signal, and more readily identify any contaminant signature beyond that.
“Trials with stainless steel in wet products have shown that Interceptor can pinpoint contaminants half the size of those detectable by former generations of equipment,” he says.
Product recovery technology can be another effective method for eliminating waste in a processing environment, says Matt Hale, international sales and marketing director of HRS Heat Exchangers.
“For example, installing a system which automatically diverts residual product when it no longer meets specification can significantly reduce waste and improve cleaning processes.”
When processing viscous foods, a certain amount adheres to the inside surfaces of machinery and pipework and can be left behind at the end of a production run.
The three main techniques — physical ‘pigging systems’, water-based flushing, and forcing clean air through the system — can all remove residual product as part of clean-in-place (CIP) procedures, says Hale.
“While all three of these recovery techniques have the ability to salvage residual product, inevitably, a certain amount is still lost as waste,” he says.
By using inline monitoring equipment linked to a system designed to allow product which meets the specified parameters to be reworked, he says the amount of valuable product recovered from equipment such as pasteurisers and sterilisers can be maximised.
“These can measure changes in the physical or chemical properties of the product, such as concentration, which is passed to a controller which determines whether to ‘keep’ or ‘discard’ that material based on pre-determined quality parameters,” he says.
The HRS Product Recovery System can continually monitor any suitable physical or chemical property such as Brix, pH, viscosity or density, depending on the nature of the product and the sensors that are available, he says.
In the pipeline
Looking further downstream, progressive cavity pumps (PCPs) can offer a unique solution for waste removal, says Lesley Eaton, business development manager at Seepex.
“In production areas, PCPs are often used to handle delicate ingredients and components that are difficult to work with, due to either high viscosity, the presence of soft solids, or shear sensitivity,” she says.
PCPs have enclosed piped systems which can remove solid waste from both high care and low risk areas, without compromising hygiene standards.
As well as the ability to handle extremely high viscosity products which do not flow, Seepex has designed a progressive cavity pump that can chop and pump in the same unit.
This means discarded products, defective raw materials and trimmings and rejects can be handled in a single system, enabling pre-treatment and source segregation of waste and by-products, says Eaton.
“This provides food processors with a solution that delivers low-cost removal while preserving the highest residual value of their by-products – particularly if the resultant ‘soup’ is sent for anaerobic digestion, to be converted into biogas.”