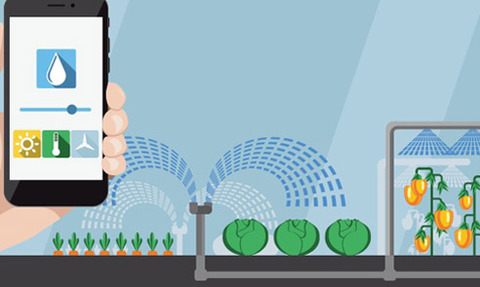
Whether it’s quality, delivery or cost, as the demands on the food industry keep increasing, so too do the expectations on its pumps, learns Brian Attwood.
Product safety is a keystone for maintaining success in the food and beverage sector. Compromise it and the effects on brand confidence can be catastrophic, no matter how speedy the remedy.
Malcolm Walker, product manager for AxFlow, comments: “The ever increasing costs financially, and potential harm to a brand’s reputation resulting from hygienically defective products, has meant that never before has there been so much pressure on food manufacturers to utilise the correct hygienic process equipment in the sight of the law.”
He notes there are two types of approval for equipment manufacturers and plants to consider; those that apply to material compatibility and those to the actual design of the pump.
Hygiene friendly
Where the former is concerned, few regulatory bodies matched the worldwide influence of the US Food and Drug Administration (FDA), at least until it was superseded by the wider and stricter criteria of the EU’s EC 1935/2004.
This requires that compounds must be subjected to more specific tests and traceability be demonstrated, whereas the FDA does not necessarily do this. A reminder that Europe’s influence may continue after next year.
Manufacturers have not been slow to recognise the need to re-examine product efficiency.
Walker cites as an example Waukesha Universal’s series of rotary lobe and ECP pumps [pictured], notably the WCB Universal 1 and Universal 2 that have played a key role internationally in the dairy industry’s fluid handling requirements.
However, the newer Universal 3 brings an extra focus on hygienic applications in food processing to meet the most stringent global standards – with SIP/CIP capabilities and double O-ring seals, which are not available in the Universal 2 and Universal 1 Series.
Additionally, the Universal TS pump for food and beverage processing employs Waukesha Alloy 88 non-galling material twin screws to pump various media containing large particulates.
This has the net effect of lowering damage to the pump and reducing maintenance, while high suction capability and a wide range of operating speeds allows just one pump to transfer product and undertake CIP.
It also removes the number of pumps, valves and control instrumentation, contributing to reduced costs and simpler, more compact systems.
The twin screws’ rotating geometry create a pulse-free flow suitable for many applications such as feeding homogenisers and the meshing screws’ identical rear and front profiles give bi-directional flows which enable easy media transfer between vessels without alteration to the pump set-up.
Front-loaded access to product side seals makes for easy maintenance and reduced downtime.
Says Walker: “Across the broad spectrum of fluids handling in the processing industries, one element that is common to all is the requirement for positive displacement pumps that can move delicate or sensitive media without causing damage to or physically altering the structure of the media.”
Digital first
The key industry refinement, however, remains the increasing integration of product into the overall industrial process: making pumps more responsive and ensuring that communication at local level is as fast and reactive as possible.
As David Brown, MD of Borger UK, points out, it is not only a question of feeding back data but ensuring pumps can help regulate their own health and remedies.
“As a critical part of most processes, pump failure is a major issue. Any forward-thinking company will want to reduce or eliminate failures that cost production – and as a minimum, condition monitoring can highlight potential failures before they cost valuable production time and product,” he states.
Seepex business development and marketing manager Lesley Eaton emphasises that pump monitoring is nothing new for companies such as hers. What has changed is the level and complexity.
The three basics now catered for are flow, pressure and temperature. “The difference is that with the smart pumps there is closed loop feedback to a PLC on the drive,” she explains.
Any forward-thinking company will want to reduce or eliminate failures that cost production – and as a minimum, condition monitoring can highlight potential failures before they cost valuable production time and product
David Brown, MD, Borger UK
“So, as the flow drops from the set point, the drive will speed up to compensate, and as the pressure increases the information is analysed and the pump shut down when the safe pressure level is exceeded.”
A mobile system linked to a Cloud-based system means that data provided can be local or involve Cloud-based data logging.
“Because Seepex pump monitoring is Cloud-based, the information comes back into our offices from the customer and we can analyse the pumps and can say whether this pump is running off curve and it needs investigation. We can say when what’s being delivered by the pumps is not what should be delivered – and I think that’s a fundamental difference.
“What we have now are smart pumps, so the idea is that you can set the pump up as a stand-alone unit if needed; as the flow changes, the pump speeds adjust automatically. This has always been possible with a VFD and centralised control – but now it can be achieved locally as well as centrally.”
Conditioning counts
While the advantages apply across all aspects of the process industries, Borger’s Brown notes the sector has an added incentive.
“The food and beverage sector is more susceptible to business costs because failures can result in total loss of a complete batch.”
Small wonder, he says, that the industry is moving towards developing condition monitoring as a standard fit on most pumps. Takeup is powered by the interplay between cost, market demand and innovation.
“The elements of what can now be monitored are endless. Process engineers can fill their boots with data that at one time would only be found in the aerospace industry. Size and cost of sensors have reduced to a point where even the simplest process can be monitored at every level.”
And yet, in the food and drink industry, not everyone buys into this. Earlier this year, Seepex celebrated an industry accolade, winning the Innovation Award in the Pumps and Compressors category at the 2018 ACHEMA show for its new Smart Dosing Pump [pictured above].
Featuring a directly integrated control system, it merges field and control levels by connecting actuators and sensors with local intelligence. Self-regulation and minimal pulsation conveying reduces maintenance and boosts cost efficiency, says Seepex. It’s also easy to operate.
Take up in the water treatment industry has been good and reception in the chemicals and pharmaceutical sectors has been favourable. The food and beverage sector has been rather slower to respond.
Eaton is optimistic that the firm’s proven success in niche areas will bear fruit. These include dosing of minor ingredients for cider (Bulmers) and bread making, plus flavouring into pet food.
The challenge as so often is to persuade potential buyers to take the long view and consider total cost of ownership rather than purchase price.
“The cost of pump purchase is recognised as being between 10-20% of the total pump ownership cost of a PC pump. The rest of it is energy and maintenance. So the initial purchase price shouldn’t be a barrier to buying technology that will reduce energy and maintenance requirements,” advises Eaton.
“It means you can move from planned maintenance to predictive maintenance. You may find that you are maintaining your pump assets more often than you need to; smart pumps provide the information needed to move to predictive maintenance.”
Inside the box
New challenges for the pumps world are prompting new solutions from the industry…
Xylem has successfully trialled its technology that provides a virtual reality view of complex pumping solutions. Pump station design specialist Adam Sheehan hit on the concept after a colleague brought a VR headset into Xylem’s Flygt office in Sundbyberg, Stockholm.
It uses virtual simulations of 3D CAD models to take the customer through various pump station layouts, transferring existing product data into gaming software to develop a VR scene, explains Sheehan.
“We were able to use specialist software to generate an accurate virtual ‘tour’ of a complex pumping station, which allowed our customers to understand how it would work in-situ. We were also able to present multiple options so they could compare the performance of different pump station simulations.”
Jamie Mills, systems engineer for Xylem UK & Ireland, said the project would have particular benefits for the water industry: “VR is a particularly promising technology for the water industry because it allows the supply chain and owner operators to collaborate in the same virtual environment and identify problems before construction, for example the position and accessibility of valves.
“This 3D visualisation is also the best way to present complex benching and baffle design which has benefits for both construction and design review. Leveraging technology in this way drives key efficiencies for capital deliver and asset management.”
The firm is now investigating the feasibility of using computational fluid dynamics (CFD) to simulate the water in pumps as part of an enhanced VR model.
* Netzsch unveiled two new pumps with a food relatedapplication. The Tornado 2 positive displacement pump’s bi-lobe rotor design creates a clonger sealing line and more wear padding, while a specially developed pulsation reduction system is intended to ensure minimal pulsation or shear forces.
Its elastomer cage acts as a stator and is subject to less dynamic load and deformation than a traditional rotary lobe pump design. Full service in place design improves access for inspection, cleaning, service, and replacing parts. A removable cover plate gives quick access to the pump chamber, while rotors are not bolted or keyed to the shafts inside the pump head.
Netzsch’s Nemo B-Max progressing cavity pump is targeted at the biomass market, aiming for homogenisation and efficient conveyance of biosubstrates.
Spiral lobes for the mixing and screw conveyor are strengthened to ensure optimum mixing of the liquid phase and dry substrate in the hopper chamber.