Chopper pumps drive sustainable farming
24 Oct 2018
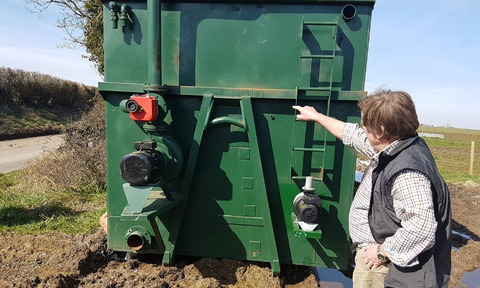
Chris Reynell is at the forefront of the ‘farm to fork’ sustainability chain. His wife Jane’s family has run Windover Farm in Hampshire for more than a century. But it mixes tradition with some revolutionary processing methods, thanks to him.
The 420-herd dairy farm has had organic status for a decade and has been a testing ground for the pioneering research and development of his multi-stage hybrid Bioplex digester process.
Appropriately, the Reynells actually met during an industry visit to view a digester back in 1990. Five years later Chris unveiled his own digester model on Windover Farm.
Fibre defeating
His aim was efficient sustainability that would be effective in terms of cost and process, achieving enhanced energy recovery from manure, grass and other energy crops plus various forms of waste.
Straw-based manure is a very problematic feedstock, observes Reynell, so the challenges for pumps were considerable.
The chopper pump is a processing device in its own right. Chemically and biologically, it breaks everything down – and doesn’t get blocked.
“For some AD plants this has caused an immediate and then long-term problem with pumps and mixers that can’t cope with some of the typical challenges of farm and food waste.”
It took until 2006, when he made his first purchase of a Landia chopper pump, before the inventor was happy with the consistency of outcome.
“I knew that we were seriously testing our process, so at one stage we ended up with a tank that wouldn’t mix with the existing equipment.
“Landia simply told us what their pumps would do – and they succeeded. The flail effect of the Landia chopper pump soon saw our straw come out like peat,” says Reynell.
It was a similar story when Bioplex launched its early food waste projects for clients, he explains.
“The Landia chopper pump made degradation very fast indeed. The food waste was unrecognisable. We also saw a noticeable improvement in the levels of our gas yield. For me, their chopper pump is a processing device in its own right. Chemically and biologically, it breaks everything down – and doesn’t get blocked.”
With at least two stages in its process, the Bioplex technology enables the conditions for hydrolysis and fermentation to thrive, breaking down more of the cellulose materials. This makes the digester far more resilient to a much wider variety of feedstock.
“We’ve been able to join all the dots on sustainability with a process that kills weed-seed and pathogens,” continues Reynell. “And because the digestate from our AD process is so much quicker and easier to spread, it also reduces our diesel costs and produces better soil for the long term good of our farm.”
Additionally, low nutrient fibre from the process can be used as a solid fuel (similar to peat) in boilers and wood-burning stoves.
Sustained relationship
Since the first Landia pump was installed with a Bioplex unit, Reynell has purchased a further 24. Landia opted to mark the 25th purchase in style, appropriately presenting it to Reynell coated in silver paint.
“Our constant factor, which for over a decade has given us increased confidence and peace of mind to take on R&D projects all over the country, has been the outstanding performance and durability of Landia’s pumps and mixers,” says Reynell.
“The very first Bioplex unit with a Landia pump, which was installed in 2006 for hydrolysing and pasteurising fish waste in Scotland, is still working perfectly.”