KKI builds its biggest ever butterfly valve to keep Danish energy plans on course
18 Oct 2018
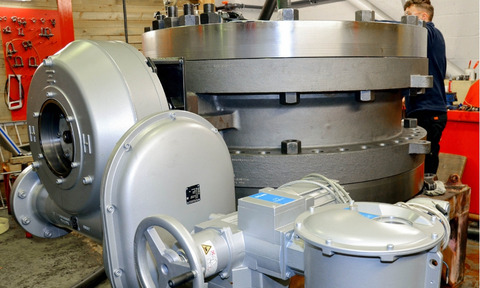
A Danish utility company’s search for a more energy efficient heating solution provided Koso Kent Introl with a major challenge. Their solution? A seriously large valve.
To fulfil Copenhagen’s aim to become the world’s first carbon-neutral capital by 2025 Danish utility company HOFOR has been working since the early 1990s to upgrade the existing district heating system to a more energy-efficient solution, using hot water instead of steam.
The project has a completion deadline of 2021 and with financial support totalling 500 million Danish krone (c£59 million) has the resources to ensure the best equipment for the job.
As part of the scheme, a bio-fuel plant was required to supply the capital city - which houses more than 585,000 people, or more than one in ten of the Danish population - with heat and power.
This was intended to replace the previous 600MW coal-fired plant and reduce CO2 emissions by a total of 1.2mt.
A question of scale
Hofor also manufactures and supplies turbine equipment for power stations and was able to develop a suitable concept. However, the project demanded butterfly valves that could cope with the scale of the system.
The new biomass boiler required a valve with a high constant volume coefficient, capable of working across a large pressure drop and able to ensure a reduced chance of cavitation.
The valve and actuator weighed 3,675kg [which] combined with the test flanges gave an overall weight of over four tonnes
Mark Tolley, sales engineer, KOSO Kent Introl
The wide range of process flow conditions meant the valve opening needed to operate within a range of 11 to 86 degrees of opening, compared to the 10 to 60 degrees of opening within which traditional butterfly valves operate.
In short, the company required two 32” butterfly valves and one 48” valve. Hofor turned to KOSO Kent Introl for a solution.
With more than 35 years’ experience engineering high-performance rotary control valves for the oil & gas, petrochemical and power industries worldwide, KOSO’s Rotrol range of high-capacity butterfly valves has been developed to problems associated with control, cavitation and noise in conventional butterfly valve designs.
Being lighter in weight and more compact than globe valve alternatives, it performs especially well in severe-service applications says the manufacturer.
However, even KKI had not built a valve to this scale before, so the result was a bespoke product designed and built after discussions and input from Hofor staff.
Bigger – and better
This involved a visit to the Danish firm’s site in the Czech Republic by KOSO Kent Introl’s sales engineer Mark Tolley and project manager Maxine Wood gave a company presentation about their unique product offering to the team, followed by HOFOR personnel visiting the KKI Brighouse manufacturing.
“The valve and actuator weighed 3,675kg, combined with the 482kg ASME 300 test flanges gave an overall weight of over four tonnes,” said Tolley.
“The water required to achieve the seat leak test; the test required 1,710 litres/min to achieve Class III leakage class – the quantity of water required resulted in the installation of a new water supply to our test area. Thankfully, the valve didn’t just comfortably achieve this, but bettered it.”
Boasting a Cv of 59,531 the valve has a profiled vane that dissipates the energy as the valve works across a large pressure drop, reducing the chance of cavitation. It also meets the greater demands required in terms of valve opening range.
The new biofuel system is now due for commission next year, two years ahead of the overall project completion date.