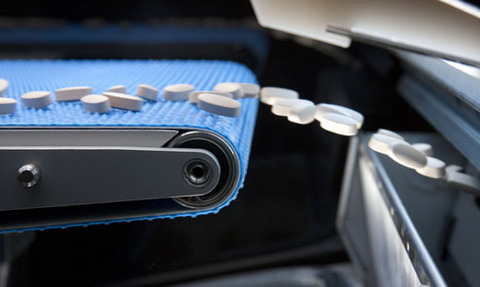
Modern bulk vision inspection systems could be just as transformative in the pharmaceutical world as they have been in the food industry, as Michelle Knott discovers.
Machine vision has been a complete game changer when it comes to mass sorting raw materials such as nuts, fruit and grains in the food industry and looks set to be just as transformational for quality control of solid-dose medicines in the pharmaceutical industry.
In food, vision technology has been central to the rise of digital sorting as a replacement for manual operations, not only incrementally improving on sorting and grading performance in existing applications but also opening up fresh ways to tackle emerging problems. The fight against aflatoxins is a great example.
Aflatoxins are the result of fungal contamination. They can be lethal in acute doses and chronic exposure can trigger cancer, which is why they are classified by the World Health Organisation as a Group 1 Carcinogen.
Machine vision is particularly useful where the colour of the accept material and the defect is similar
Ben Deefholts, senior research engineer, Bu?hler Group
Historically, aflatoxins are a problem most commonly encountered with plants grown or foods stored in hot and humid parts of Asia, Africa, and the United States. However, in February this year the European Food Safety Authority (EFSA) reported that there are also concerns about “the elevated aflatoxin levels observed by some food commodities originating from European countries”, leading to calls for EFSA to make its first full risk assessment of aflatoxins in more than a decade.
Some food businesses check for aflatoxins by testing samples, but Karel Strubbe, EMEA sales director for TOMRA Sorting Food, uses the example of a silo full of peanuts to explain why that’s not a dependable approach: “The problem is that dangerously high levels of aflatoxins can be present in the silo but only in small clusters of nuts. This means there is a correspondingly small chance of those contaminated nuts being picked for a test-sample.”
Instead, TOMRA advises using sorting machines that rely on a combination of sensors to visualise aflatoxin contamination and sort all the nuts. “TOMRA’s machines employ near infrared (NIR) spectroscopy, fluorescent lighting, and state of the art lasers to analyse the surface structure and elemental composition of objects passing along a food production line.
“The special optical design of TOMRA’s Detox laser makes it possible to identify the extremely low intensity of light reflected by aflatoxin mould and fungus in a variety of food types, enabling the detection of aflatoxin contamination,” says Strubbe.
Shine a light
Bu?hler Group is another major sorting company that has turned its sights on aflatoxins. Senior research engineer there, Ben Deefholts, explains how they work with maize: “Aflatoxin in maize is caused by the interaction between a specific type of fungus and the material in the maize. This same interaction also causes creation of an acid on the surface of the maize – Kojic acid. We are very fortunate that the Kojic acid glows a bright green colour when illuminated with UV light. We use this as our major indicator in our new LumoVision technology for sorting maize to reduce aflatoxin contamination.
“Another interesting point about LumoVision it that it uses an AI system and cloud technology to process huge amounts of info in milliseconds that is not humanly possible. This cloud-based digital service can predict in real-time the risk of contamination in any given batch of maize. Data gathered by the camera about each grain is combined with more general risk data related to the batch, allowing the machine to assess the overall level of risk of contamination and automatically stop and start sorting.
Advancing technology has ushered in a new class of bulk vision inspection systems that is prompting debate on what it means to be diligent in pharmaceutical manufacturing and packaging operations
Marco Azzaretti, inspection systems product manager, Key Technology
“If the risk is high, the customer is sent an alert, so that they can take additional precautions. If the maize is assessed to be clean and the overall risk as small, the machine can decide it is safe to halt sorting. As soon as the machine identifies aflatoxin in the product again, or a higher level of risk, sorting is automatically resumed.”
Decision-making happens on a ‘per-grain’ basis in less than 100 milliseconds, at industrial throughputs of 10-15 tonnes per hour. The increasing sophistication of optical sorting systems are also finding favour in a host of other food applications, as Deefholts explains: “Machine vision is particularly useful where the colour of the accept material and the defect is similar. In some varieties of almonds for example it is almost impossible to see the difference between a small almond within its shell and the brown skin natural almond out of its shell.
“For these applications we make use of different properties that the materials might have. For tree nuts we know that the nut material has a high oil content. If we look at what we are trying to remove, for example shells, sticks, or hulls from almonds, we can make use of the oil absorption dip in the IR to distinguish clearly between the nut meats and other material. In frozen vegetables we know they contain water, so we are able to use a water absorption dip in the IR to distinguish between a wide range of foreign matter and vegetable matter.”
Meanwhile TOMRA has developed its unique biometric signature identification, or BSI, to improve the performance of its sorting machines. “BSI works by detecting the biometric characteristics of the food items it scans and compares these to features stored in the machine’s database to determine whether the items should be accepted or rejected. This detects and removes smaller defects than is possible with conventional spectral technology. Detection accuracy is so good that false-rejection rates are exceptionally low and yields exceptionally high,” says Strubbe.
Optical sorting technologies may have been born in the food industry, but they’re increasingly important in pharmaceuticals too. For instance, Key Technology is another major player in digital food sorting, but the group is also promoting the use of bulk sorting through its pharma-focused Symetix group.
“Until recently, automated inspection of solid dose pharmaceuticals was either crude (in the case of mechanical size graders) or expensive, slow and difficult to changeover (in the case of single-file optical inspection systems). Many pharmaceutical manufacturers and contract packers have historically relied on labour-intensive manual inspection. Now, advancing technology has ushered in a new class of bulk vision inspection systems that is prompting debate on what it means to be diligent in pharmaceutical manufacturing and packaging operations,” says Marco Azzaretti, advanced inspection systems product manager at Key Technology.
First introduced 20 years ago, single-file or single-stream optical inspection systems are effective, but have significant drawbacks, including high capital costs, low throughput (often around 50,000 doses per hour, according to Symetix), expensive change parts and changeovers that can take as much as eight hours to complete.
“Unlike single-file optical inspection systems, bulk optical inspection systems need not single-file or orient the products prior to inspection. Like single-file optical inspection systems, bulk optical inspection systems are highly effective in detecting and removing defects and foreigners based on differences in size, shape and colour. Bulk inspection systems feature high-performance, high-resolution colour cameras to detect even small and subtle differences,” explains Azzaretti.
“Compared to single-file optical inspection systems, bulk optical inspection systems are affordable (roughly one third the cost of single-file systems, based on equivalent capacity). They achieve high throughput (inspecting up to one million tablets or capsules an hour). Furthermore, bulk optical inspection systems can be cleared and cleaned in less than five minutes. These automated systems offer operator-independence that improves repeatability to produce the most consistent final product quality.”
Azzaretti believes it’s hard to overestimate the likely impact: “The arrival of modern bulk vision inspection systems designed for solid-dose pharmaceuticals is likely to transform the industry.”