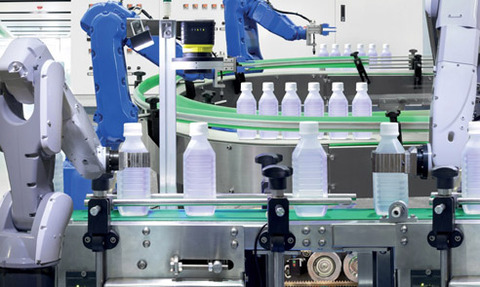
The issues facing the food and drink sector are not new but national and international conditions mean they are intensifying. The process industries are mining new seams of innovation, reports Brian Attwood.
Probably, this will be the last time that Process Engineering focuses on the food and drink sector before the consequences of Brexit are a matter of reality rather than supposition.
Already, though, within there is consensus that the period ahead will see contractions in the labour force, a more harshly competitive manufacturing environment and more focus on standards and the circular economy.
The sector’s response rates will be crucial in three areas. First, general process efficiency – how can the sector use best the people it has, employing them where they are most useful and removing them from areas where they are not; how can lines (factory and supply) operate faster and limit downtime?
Second, safeguarding integrity – watching out against accidental and (along the supply chain) deliberate compromising of product.
Growth in food fraud indicates that it is time to apply the same traceability techniques to spices, meat products, olive oil and wine, where counterfeiting is an enormous issue and safety is paramount
Joanna Mooberry, marketing manager, Mettler Toledo
Finally, sustainability – reducing the incidence of waste at point of production and also recycling food waste as material for other processes and thereby realising more process value.
The catalyst for much of this transformation will be the IIoT/digitalisation of industrial processes, yet these oftenabstract concepts have perhaps succeeded in scaring as many companies as they have inspired.
The more effective persuaders may prove to be the multiple instances of innovative technology in each of the above areas.
At the ‘farm’ point of the journey, robotics can make an obvious contribution in a sector that is likely to be denuded of much of its foreign labour and hit by increases in National Living Wage that could increase manual harvesting costs by more than one third over the next three years.
Future proofing
Entrepreneur, engineer and farmer Peter Keeling, founder of KMS Projects, has partnered with technology leader FANUC UK to design a selective automated broccoli harvester. It may prove a godsend for producers who typically rely on teams averaging seven people for work that is monotonous and prone to injury and human error.
Three FANUC rig-mounted, 6-axis M20iB robots each have a cutting tool able to harvest a head every three second. It’s designed to be twice as fast as a human picker and, thanks to a visual detection system, guaranteed only to pick vegetables that meet the size requirements. Tailored to broccoli, it can nevertheless be adapted for a variety of leaf crops.
Technical sales support engineer at FANUC UK, Oliver Selby, remarks: “Broccoli picking is just one great example for the use of robotics in agriculture. In time, we will see more and more applications develop as the industry accepts and adopts the need for automation in order to stay competitive. Innovations such as this can go a long way to help future proof the industry for years to come.”
This will be welcome news for the fresh food produce market as a whole. Despite being one of the fastest-growing food sectors, automated packing and palletisation machine manufacturer Brillopak recently noted in a report by Plimsoll that fresh produce languishes third from bottom where profitability is concerned.
The more extensive a supply chain and the further inspection equipment is pushed up the line, the greater the risks
Phil Brown, managing director, Fortress Technology
Brillopak addressed the practical considerations built around that staple of the fresh food sector, the punnet.
Director David Jahn explains: “The most common dilemma in punnet packing is not the movement of products but managing the container in which they are being placed.
“With punnets we are dealing with a pack shape that can vary by three millimetres. This can cause punnet edges to catch, overlap or flip when inserting into retailer containers. This in turn slows the line down while an operator manually resolves the issue and flattens the layer, before the next layer can be stacked on top.”
Layers are assembled on the container side and then a vacuum end-effector suctions the entire layer, allowing a supporting plate to retract, before lowering and pressing the punnets into place.
Removing a layer of human intervention saves on production time sufficiently, claims Jahn, to provide a return on the not inconsiderable £87,000-plus price tag for the Brillopak BR2 Punnet Packer within one year.
To the rescue
Time constraints do not provide an accommodating environment for packing the most delicate fresh produce. Yet, again, innovation is coming to the rescue.
ULMA Packaging’s Venturi system was pioneered in the herb sector and designed to improve vertical packaging methods in order to reduce time spent when product became stuck in the seal positioned over the container bags. It’s now being extended to salad leaf packing.
Business manager at ULMA, Steve Brooks, outlines: “Unlike traditional vertical packaging machines where the re-work required for bags with product stuck in the seal is between 7-10%, the Venturi System’s use of air to pull the product all the way down to the bottom of the bag safely can lead to a reduced re-work of less than 1% when used in conjunction with ultrasonic sealing technology.”
Bag length and width can also be reduced because product is pulled further inside during sealing, while the machine can deliver 60 packs a minute worked by two employees, compared with a flow wrap machine average of 10-16 employees achieving 25 packs per minute.
Safety foremost
Intrinsic to the pursuit of productivity and likely to become more so, are the issues of food safety. Ground-breaking innovations such as MIT’s newlydeveloped RFIQ system offer a chance to harness consumer power and the end user: RFIQ includes a reader that senses minute changes in wireless signals emitted from RFID tags when the signals interact with food.
However, where other aspects are concerned, the pressure is growing to combat metal and other threats at an earlier stage. Phil Brown, managing director of Fortress Technology [pictured], warns that food inspection needs to become more precise.
With an average ready meal, there can be more than eight production steps between sourcing ingredients to packing, and more than five different product components each requiring, cleaning, peeling and inspection, slicing, cooking, quality inspection, flavouring and finally weighing and packing.
“The more extensive a supply chain and the further inspection equipment is pushed up the line, the greater the risks,” he cautions.
A bigger threat ultimately is likely to be the incidents of deliberate food fraud. Marketing manager at Mettler Toledo, Joanna Mooberry, warns that the growth in online food sourcing could ‘open the floodgates’ to the level of counterfeiting that has dogged the luxury goods market for decades.
“Serialisation and track and trace techniques have proved highly effective in combating fraud in other industries like pharmaceuticals,” she says, adding that food industry investment has been limited to high value items such as caviar, with a universal labelling system to prove authenticity and legal purchase.
“Growth in food fraud indicates that it is time to apply the same traceability techniques to spices, meat products, olive oil and wine, where counterfeiting is an enormous issue and safety is paramount,” says Mooberry.
The greatest productivity dilemma in food and drink though remains waste. The World Resources Institute estimates that a quarter of human food remains uneaten and within Europe and America, significant opportunities occur within the production, processing, storage and distribution stages.
Jason Andersen, vice president – business line management at Stratus Technologies, notes one side effect of greater awareness and more sophisticated technology has been a sizeable increase in recalls. That’s not an argument against progress, he says, but a challenge to extend best practice down the supply chain.
“While manufacturers may have controls set up to monitor their own processes, they are missing specific, beginning-to-end monitoring of their entire supply chain, including raw materials through packaging and distribution, which will help them recalibrate and adjust to this new-found visibility.”
His remedy is wider implementation of tracking technology and, where resourcing is limited, to prioritise areas that are most essential to food safety and quality. IIoT offers the means to ensure compliance down the food chain but essential to its effectiveness is the ability to leverage and protect data, insists Andersen.
What goes around…
A still greater contribution to food waste in the developed world occurs at the consumer stage; long-term then, effective solutions require this material is reintroduced into the industries from which it emerges.
At Queen’s University Belfast, one of the UK leading centres for excellence in food science, Dr Eoin Cunningham’s research is focused on development of the circular economy, with the valorisation of agri-food industry waste streams into new added value products.
Among his projects, ‘Consumer and Manufacturing Driven Alternative Packaging’ has been enthusiastically received by industry, with sign-off pending from retailer Waitrose, German research giant Fraunhofer and leading meat supplier ABP food.
Scaleability is always an issue so I have deliberately tried to target wastes that are abundant in nature and pose problems
Dr Eoin Cunningham, Queen’s University Belfast
His target is not only food waste reduction but also plastic pollution. Poultry waste provides an example of unused ‘product’ into a new bio-based polymer, creating added value for the waste producer.
For example, he says, feathers are essentially keratin and a natural polymer in themselves, yet difficult to process as a traditional polymer. Cunningham has now successfully processed feathers in the QUB Polymer Processing Research Centre like a traditional polymer – creating a product alternative to plastic.
Industry engagement is essential in order to progress such work, insists Cunningham; there needs to be demonstrable opportunity for companies to derive practical value.
“Scaleability is always an issue so I have deliberately tried to target wastes that are abundant in nature and pose problems,” he explains.
Where his work is concerned, there is a clear benefit in terms of combating landfill, “and it feeds into a polymer industry that uses 5.7 billion barrels of oil a year to create 311 million tonnes of synthetic polymer”.
But he adds: “I have to admit, the Blue Planet effect is making my job a lot easier.”