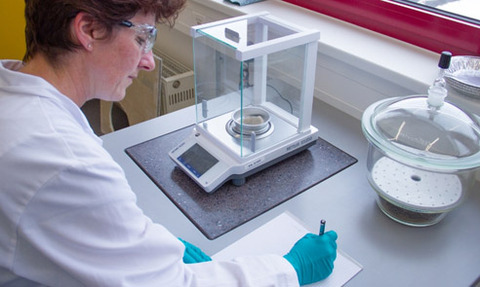
Only lately have we begun to appreciate fully the impact of filter medium resistance. Josef W Tichy explains how his company, BHS-Sonthofen, identified a gap in previously-accepted theories and the consequent potential benefits for industry.
Up until recently, it had been thought that cake filtration was sufficiently understood. However, in the early 21st century it was found that research had long overlooked one aspect – the proportion of the filter medium resistance to the total resistance of the cake filter at the end of a filtration cycle.
Previously, this was hardly ever measured, and experience led to the assumption that the value was between five and 10%. Manufacturers have reached their limits using existing theories, especially regarding the easy-to-filter materials that are increasingly used today.
Yet filter medium resistance is proving to be an important process parameter for the optimisation, simulation and design of high-performance filters in particular, as they have to cope with high quantities of filtrate. This is because the previously ignored filter medium resistance can represent quite a relevant proportion – up to 50% – of the total resistance.
Precise data, longer life
Cake filtration is commonly used in the processing of raw materials and minerals, as well as in the chemical and pharmaceutical industries. Both the separated solid material and the liquid are usually ready for immediate downstream processing. Users are demanding increasingly more efficient filter systems that operate smoothly from the first to the last filter cycle and that are available over the long term. These demands can only be met with an overall low filter cake resistance.
The filter also needs to reach steady operation quickly after the start-up phase, be simple to clean and replacement parts need to be easy to install. At the same time, manufacturers are ensuring the machine’s function using third-party filter media. This means that filter media designers also need reliable data to offer competitive material.
Recent research was therefore able to demonstrate that the resistance of the filter medium had a substantial influence on the separation work in cake filtration overall
Cake filtration is a process used for mechanical solid-liquid separation in which solid particles contained in the suspension are retained by the filter medium and deposited on its surface. This forms a filter cake which then acts as a barrier for each new suspension element.
The filter medium is key to the composition of the filter cake, meaning it is also the key factor for particle retention. The initial phase of the filtration is of particular interest in terms of gaining a clearer insight into filter medium resistance. When pure liquid flows through the filter, the filter medium offers a certain amount of resistance against the flow.
The transfer of the flow of a liquid free from solid particles into the flow of a suspension containing particles causes a so-called resistance jump. This jump refers to the interactions between the filter medium, the liquid and the solid particles.
Operational experience gave cause for researching this resistance jump and filter medium resistance. When adjusting a rotary pressure filter to a higher filter throughput in the early 2000s, the company BHS-Sonthofen observed that the proportion of the filter medium resistance to the total resistance of the filter cake must be significantly higher than 10%. This finding established a gap in the existing filtration theory.
Research efforts have made significant progress since this discovery, and it has been possible to calculate the resistance jump with great precision. This involved a series of experiments performed on a laboratory agitated Nutsche filter – the handheld measuring device from BHS-Sonthofen. The focus of these experiments was the time- and pressuredependent accumulation of the quantity of filtrate in a certain suspension, the cake height and composition as well as the mesh adherence properties.
A new method was used to evaluate the accumulated data. This was based on two tried and tested methods that were very similar in mathematical terms.
The first method evaluates the duration of the filtration by volume, while the second evaluates the difference in filtration time by difference in volume. Both methods were combined for the first time to realistically calculate the start time of the filtration.
This combined approach allows the resistance of the filter medium to be calculated more precisely.
The results help to improve the design of continuous filters. Even with an optimised mesh, the resistance of the filter medium here generally amounts to around 20% of the total resistance at the end of a filtration cycle – in other words, significantly more than it was assumed to be just a few years ago. The resistance jump can be very high, depending on the filter medium used. Or, more specifically, a coarser filter mesh structure causes the resistance to have an even greater impact.
Especially easy-to-filter materials are typically processed using filters with a large pore diameter. The values measured in these cases delivered peak filter medium resistance values of up to 50% of the total resistance.
Recent research was therefore able to demonstrate that the resistance of the filter medium has a substantial influence on the separation work in cake filtration overall. Better theoretical knowledge means the resistance of the filter medium can be reduced during the design phase. This improves the energy performance of the filters, especially in systems with high throughputs, thus reducing the user’s investment and operational costs.
However, there is still more to be learned about the physical relationships underlying the build-up of filter medium resistance in order to keep reducing it in the future. These relationships are the focus of current research efforts.
Focus on flow
Computational fluid dynamics (CFD) is the method of choice in this area. CFD makes it possible to visualise the extremely fast, microscopic processes at the start of cake filtration and provides insights into how the flow changes when particles first come into contact with the filter medium.
This then raises the question of similar processes occurring in other filtration processes. Both cross-flow filtration and depth filtration are viable candidates. Processes observed in the latter in particular have displayed similarities in the mesh at the start of cake filtration.
Even with an optimised mesh, the resistance of the filter medium here generally amounts to around 20% of the total resistance at the end of a filtration cycle – in other words, significantly more than it was assumed to be just a few years ago
Traditional computer models have since reached their limits, meaning that new models are needed for the complex analysis of these processes. Also, the applicability of computer-generated simulations is limited. Therefore, the physical background of filter medium resistance cannot be fully understood through these processes alone. Similarities demonstrated in other filtration processes suggest alternatives to CFD.
Scientific institutes now need to step in as companies cannot handle the scope of research involved on their own. It is still not fully known how and why particles accumulate on the mesh of the filter medium in the first moments of the cake filtration process.
In the future, the right expertise could contribute to further reducing the resistance jump and to preventing the filter mesh from becoming contaminated in the long term – a phenomenon that remains unclear.
- Dr Josef W Tichy was head of development, research & laboratories at BHS-Sonthofen in the area of filtration technology until his retirement in 2007