Revolutionary sludge treatment adopted by Thames after trial success
22 Mar 2019
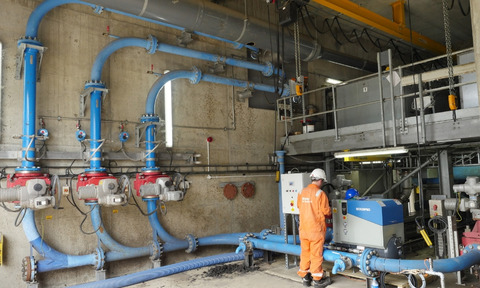
SEEPEX recently trialled its revolutionary treatment for dewatered sludge handling and following tests it's now being adopted by Thames Water
Thames Water, which provides wastewater services to 15 million customers, was committed to reducing its energy consumption for the handling of dewatered sludge for its Riverside project.
“We were faced with a particularly tough challenge at Riverside,” explains Paul Fountain, senior consultant – biosolids, for Thames Water.
“Replacing a problematic conveyor system with proven PC pumps was the preferred solution, but due to very tight space constraints, low access walkways and a labyrinth of pipework to work around, the traditional multi-stage pump was not going to be possible.”
Progressive cavity pump specialist SEEPEX had worked for many years to increase the water company’s process efficiency and reduce the energy consumption of dewatered biosolids sludge handling.
It has developed a new system to improve dewatered sludge handling using smart air injection (SAI) – enabling long distance transfer with reduced operational costs by using a combination of PC pump technology and dense-phase conveying. Having observed SAI in action in Sweden, Thames sought to measure the potential energy savings it could make by installing a trial system at its Reading STW.
Reading the benefits
This site had previously used piston pumps, but as a result of process limitations and high operating costs, Thames Water switched to SEEPEX’s multistage PC pumps in 2014. That solution halved Thames Water’s energy use, as well as reducing transport and maintenance costs.
The recent Reading trial set out to prove the technology and quantify the additional energy savings that could be delivered by pumping the dewatered biosolids from the centrifuge discharge to the storage silo. An SAI trial unit, including full controls and monitoring, was installed on the SEEPEX multistage PC pumps for a trial period and the results were recorded.
The recent Reading trial set out to prove the technology and quantify the additional energy savings that could be delivered
For SAI, a ‘plug’ of dewatered sludge is formed by an open hopper pump, then split into smaller plugs and transported onwards using compressed air in the discharge pipework. Air injection is tailored to each application on-site, using algorithms to ensure that the discharge pressure remains below 4 bar.
The plug is lubricated with boundary layer liquid, which reduces friction losses in the pipework and improves the energy efficiency of the system as a whole. Adjusting system parameters such as plug length, boundary layer liquid and air volumes on-site makes it possible to set application-specific, energy efficient, operating parameters.
Tested for action
The trial concluded the energy saving with SAI compared to a multistage PC pump without air injection was 15%. Compared to the original piston pumps, the energy saving was 61%.
Based on air usage data from a working SAI installation using SCT pumps in Belgium, it was estimated that switching to a single stage SAI pump fitted with SEEPEX’s Smart Conveying Technology (SCT) in place of multistage pumps wold produce estimated energy saving at Reading STW of 40%. Compared to the original piston pumps, an SAI system with SCT pumps would reduce energy consumption on this application by approximately 75%.
SCT pumps deliver a range of other benefits, too: reduced investment costs; longer service intervals; lower maintenance costs; smaller pump footprint; maintain in place capability; and long-distance transfer of non-flowable products.
As a result of the successful Reading trial, Thames Water has procured several of SEEPEX’s SAI units for its Riverside project.
“This allowed us to significantly reduce the pump length and installed motor powers, and has the added benefit of ease of maintenance,” said Paul Fountain.