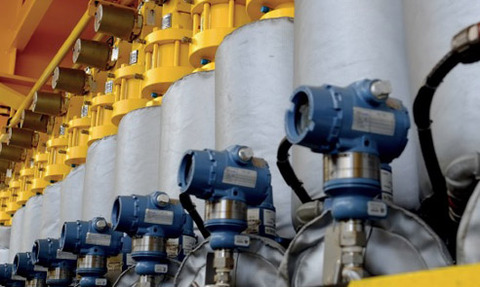
The recent history of the oil and gas sector has been one of ups and downs. It has always expected reliability from its pumps but now it wants still more, writes Brian Attwood.
If any word has characterised oil and gas in recent decades, then surely it is uncertainty.
The sector’s fortunes fluctuate precariously between high and low prices, as sources have served as a geopolitical weapon between states. Meanwhile, the growing demand for clean energy has forced the sector to contend with new practices, culture change and greater innovation.
Small wonder that, where pumps and their ilk are concerned, the emphasis in the industry has been upon toughness and reliability both upstream and down. Or put another way, certainty in performance.
By contrast, the issue of energy efficiency has tended to receive rather less attention – a view expressed by the British Pump Manufacturers Association chief executive Steve Schofield more than two years ago in these pages.
Intelligent pumps will receive a further boost with pump companies adopting the 2020 strategy, wherein the focus will be on saving energy using advanced and sustainable technologies
Srividhya Murali, senior research analyst, Frost & Sullivan
Granted, the often extreme demands placed upon products, especially upstream and offshore, has fuelled the bias.
Yet the contribution that energy costs make toward overall expenditure is substantial, as is the proportion of total energy expended that is accounted for by pumps.
Given that the oil and gas sector is facing competitive pressures from alternative fuel and power sources and (certainly within the UK context) a diminution of traditional supplies, we can expect the issue of pumps efficiency to become increasingly crucial.
This pressure will not be mitigated by the promise of new sources such as shale onshore or more effective exploratory techniques; these will involve more complex and/or controversial operations with extra cost attached. The pressure is on pumps to deliver and to do so better.
Leading international market analysts Frost & Sullivan note that European Union directives have played a useful part in nudging industry in the right direction.
Energy gains
The EU directive on the reduction of energy consumption has helped stimulate the market for intelligent pumps. This process began with the integration of variable frequency drives (VFDs) and controllers that enabled the conservation of energy, speed controls, performance monitoring and measurement.
For manufacturers and suppliers that has had export benefits too. German-based SFC Energy’s Simark Controls subsidiary recently announced a major contract with a Canadian oil producer seeking VFDs to operate its electric submersible pumps which lift heavy oil from well pads. Benefits include reduced system downtime and optimised pump performance.
“Our customised VFD solutions are experiencing continued demand and strong recognition in the oil and gas industry,” states Simark Controls vice president, drives and motor control, Mark Vandenbrink.
“Automation, system intelligence, simplified logistics and low integration and operating costs are the main innovation drivers in the industry. We custom design our systems to give producers exactly what they need.”
Customisation is an important factor for companies with substantial legacy assets they would rather repurpose than replace. This has enhanced the rate of intelligent pump adoption within the EU region, including its departing UK member state.
“With IIoT, there is a huge demand for sophisticated techniques such as predictive maintenance, remote monitoring, digital twin technology, artificial intelligence (AI) and virtual reality/augmented reality (VR/AR),” says Srividhya Murali, senior research analyst, industrial team at Frost & Sullivan.
“Intelligent pumps will receive a further boost with pump companies adopting the 2020 strategy, wherein the focus will be on saving energy using advanced and sustainable technologies.”
The company’s newly unveiled report, European Intelligent Pumps and Controllers Market—Driving Smart Revolution, Forecast to 2024, cautions however that the benefits of VFD are already proving insufficient for next-generation automated industries.
Smart move
Increased adoption of IIoT (Industrial Internet of Things) technology will boost the need to transform merely intelligent pumps into smart and fully integrated products, says the company.
Two capabilities these areas could address are predictive analysis on the one hand and digital twin and augmented reality/virtual reality on the other.
Adds Murali: “With software-based predictive analysis becoming a highly popular feature, there will be a surge in the number of collaborations between pump manufacturers and the IT sector.”
For the aforementioned suppliers and manufacturers there are further gains as oil and gas companies increase adoption of intelligent pumps and identify potential savings and investment.
These include connected plant, waste-saving 3D printing, after-sales service to reduce downtime and repair charges, as well as predictive maintenance.
Notes Murali: “The shift in market focus from product-centric to service-centric will lead to new types of business models that will feature more lifecycle management contracts.”
SPX Flow’s ClydeUnion Pumps brand is employed in both downstream and upstream oil activities including exploration, refining and distribution. Its ClydeUnion Pumps CUP-BB5 is one example of the latest generation of high-pressure, multistage, barrel case pumps designed for this increasingly sophisticated market.
Part of a portfolio of high-pressure pumps designed to the latest application programming interface (API) specifications and global oil industry requirements, it featured at the Abu Dhabi Petroleum and Exhibition Conference (ADIPEC) show in Abu Dhabi in November.
Engineered in a variety of configurations to match process needs, applications include seawater injection, produced water reinjection, flow-line displacement, crude oil pipeline, NGL pipeline, refinery process charging, gas treatment, boiler feed and refined product pipeline distribution.
Yet certain factors dictate that there will be a divergence in attitude sometimes between the upstream and downstream industry. Sulzer Wood general manager Murray Wilson cautions that, offshore, capital expended in order to improve reliability is too often outweighed by unpredicted failures and the cost of resultant downtime.
Yet even if this limits the scope for innovation, there is much that can be done to improve proactive maintenance of equipment.
“In terms of through-life maintenance cost, preventative action is almost always less costly than corrective action, and adopting a carefully managed, proactive regime is crucial to identifying potential issues before they develop into problems,” he states.
Where pumps are concerned understanding cavitation and tackling erosion are of prime importance, he advises. By preventing cavitation, one avoids the alternative of simply trying to reduce the effects on pumping equipment retrospectively; usually by increasing suction head, lowering fluid temperature or decreasing the net positive suction head.
Fluid abrasiveness gives rise to decreased pump performance in produced water re-injection pumps, often as a result of sand particles. This can be tackled by manufacturers minimising flow velocities or ensuring flow is lowered for close-running clearances, advises Wilson. High-quality protective coating is also required.
The valves sector has also been ripe for innovative approaches to coating. Bicester-based Hardide Coatings partnered the Canadian Master Flo Valve Inc (MFV) to create a new solution for subsea choke valves in 2017.
Preventative action is almost always less costly than corrective action, and adopting a proactive regime is crucial to identifying potential issues
Murray Wilson, general manager, Sulzer Wood
Previous attempts by MFV to find coatings that could cope with the high temperature and pressure demands had failed.
The result was a solution that could form a smooth finish with a firm metal to metal seal and was capable of dealing with temperatures up to 400ºF and 20,000psi pressure.
Valve effectiveness is no less crucial as the emphasis increases upon the distant and deeper sources for oil and gas upstream. Lee Products’ check valves function in environments where chemical injection systems must operate in hostile conditions.
With aggressive fluids used at extremes of temperature and pressure, reverse flow prevention is essential but with the caveat there must be no leakage. Custom polymeric valve seats ensure zero leakage of fluids at pressures up to 15,000psi and at temperatures up to 400ºF.
The case of MFV demonstrates that valve manufacturers’ ability to make significant advances may depend upon their ability to seek partners with different skillsets and expertise.
Specialist in computational fluid dynamics (CFD) TUV SUD NEL has collaborated with one leading UK valve manufacturer to create a series of safety tests for products used in similarly demanding contexts.
Different dimensions
CFD team manager Marc Laing and his colleagues were able to create a 3D model of the valve equipment to test performance.
“The client has designed a valve they want to use for a specific purpose in a very challenging environment, one in which there is a very high-pressure drop and a flow with a high level of sand contamination,” he explained.
“They wanted to test the valve to ensure that it works to specifications. Prior to this, for health and safety reasons, they needed to check that the valve wouldn’t be destroyed or fail catastrophically during the test itself.”
Downstream, in the case of refineries, control valves form a significant capital investment and are intrinsic to safety and optimisation.
Emerson Automation Solutions, oil and gas business development manager Vincenzo Sipala cites the contribution control valve technology can make to achieving that ‘top quartile’ performance (defined as amounting to 3% unplanned downtime with maintenance costs of less than 2% of plant replacement value and reduction in plant downtime) that forms one of the company’s core themes.
Selecting the right valves ensures the reduction or avoidance of cavitation, excess noise and compressor surge – thereby enhancing flow capability while reducing noise, damage and vibration.
But just as important for combating those threats within the process plant is ongoing maintenance and diagnosis. Emerson’s Severe Service app for process control engineers, designed for Fisher globe control valves, offers one means for doing so.
Capable of displaying valve coefficient (Cv) value and indicating cavitation or noise issues, information can be shared with maintenance and other teams. It also includes access to a Fisher control valve sizing tool, control valve diagnosis information, plus technical and application libraries.