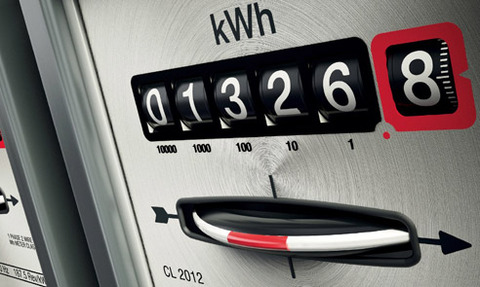
Reducing manufacturing labour costs has long had priority over energy savings but the focus is shifting and pumps will provide a catalyst, learns Brian Attwood.D
As anyone in need of DIY advice will be aware, there is a wealth of such knowledge to be accessed on the internet.
The same applies when it comes to manufacturing innovation, where the opportunity is growing for companies with limited resources to sample expertise normally open to those with larger budgets. One such is the recent (and recommended) webinar from oil giant ExxonMobil, How to Save Energy in Plastics Processing, featuring the founder of consulting engineers Tangram Technology, Dr Robin Kent.
Noting the most significant changes in drive technology have included the introduction of all-electric machines, Kent referenced the fact that the rate of adoption in East Asia is markedly ahead of where it is in the West.
Energy suppliers are also changing the way the way their tariffs are charged, which has an impact on the cost to us. So, anything we can do to offset that cost by making savings can only be a benefit
Chris Crowe, contracts service manager, Coal Authority
But, as he reminds us, this is not necessarily a matter of simple aversion to addressing an issue that would bring significant productivity benefits.
In the West, while energy has been an important consideration, labour costs have been a still greater issue historically.
In East Asia, such costs have been much lower traditionally. Therefore, these are a far less significant contributor to overall cost and “if labour costs are low, then you focus on energy”, suggests Kent.
Laboured gains
However, years of addressing the labour issue means that, in fundamental terms, European and American plant managers have largely wrung what they can from that source. Not least because digitalisation is creating demand now for new roles and skills.
At the same time, the labour force not only lacks the personnel trained for such jobs but is also contracting, as older workers are retiring and insufficient new recruits are available.
The consequence is that the average cost of labour is, if anything, likely to increase. Energy then becomes the significant resource that manufacturers must look to for significant savings.
The actual cost of energy is, of course, largely beyond the control of the individual plant or company. The gains therefore must come from efficient use of energy purchased. Which brings us to the part played by pumps.
Gary Wilde [pictured], technical services officer at the British Pump Manufacturers Association (BPMA) suggests that while pump manufacturers are mostly keen to invest in new technologies, “in my opinion, a lot more can be done”.
Given that there is, he says, a worldwide pump market valued at £61 billion, with Asia Pacific accounting for 50% and Europe about 25%, even slight technical improvements will reap appreciable benefits.
That will be crucial to offset other costs less likely than ever to permit savings – such as labour.
“As is the case with other engineering disciplines, there is a distinct lack of new engineers coming into the pump industry and has been for some time; the sector needs to encourage far more talent.
“Across the European continent, in order to maintain profit margins, we’re seeing the migration of manufacturing activities away from the West to Central and Eastern regions due to lower costs in raw materials, production and labour, as well more favourable tax structures.”
Efficiency drives
Motors, drives and controls could provide much of the focus. In the UK, the Coal Authority may represent a form of energy that is declining rapidly in terms of importance but it continues to be a substantial player.
The organisation’s annual electricity bill alone currently tops £2.4 million a year, says contracts service manager Chris Crowe.
“Energy suppliers are also changing the way the way their tariffs are charged, which has an impact on the cost to us. So, anything we can do to offset that cost by making savings can only be a benefit.”
Its solution has been to invest heavily in new pumps and pump controls at its various water treatment and pumping stations.
High standards
Working in conjunction with Severn Trent and partner JN Bentley, it has drawn up a new standard specification for its motor control centres.
While the capital outlay on pumps and panels has been a sizeable £1.7 million, the ongoing energy savings each year will provide the necessary return on investment.
With the benefit of a variable speed drive to control output, energy consumption can be reduced by up to 60%, says Crowe.
He adds: “This enables us to do away with complex programmable logic controllers and other systems that were neither functioning nor providing adequate control.”
As one example, a 132 kilowatt motor operating continuously will now yield savings of more than £27,000 alone.
Tangram’s Kent notes that the use of variable speed drives can effect an overall reduction in motor speed of up to 20%, producing a saving of nearly 50% of energy use in this area within the plastics processing plant.
The speed drives employed by the Coal Authority for its pumps overhaul were supplied by ABB which has, furthermore, sought to apply its advances made in sensor technology for motors within the pumps arena.
It is now three years since it unveiled its ABB Ability Smart Sensor [pictured] at Hannover. The company represents the product as a gamechanger that revolutionised maintenance with a consequent saving on downtime.
But its collaboration with Swiss firm Egger allowed the company to make the lateral move from motors to pumps. Sensors were adapted to accommodate pumps’ requirements for values on speed, overall vibrations, unbalance, cavitation and clogging, says the firm.
Data gathered is then directed to the ABB Ability Cloud, with operators able to view data on browsers or a smartphone.
The advantage of the smart sensor is that it addresses a key challenge for companies that lack resources or need to manage cost closely but are saddled with substantial amounts of legacy assets.
ABB’s smart sensors for example can be attached to most low voltage induction motors and without wiring. This removes the need for a comprehensive overhaul and replacement programme that a company may be unable or unwilling to afford in order to achieve full IIoT connectivity.
“Just like a home security camera being connected to your mobile phone, a smart sensor could give a motor a new lease of life, making it perform as an integral part of the data-rich factory and providing all the additional benefits that this creates,” says ABB food and beverage program spokesman Markus Brettschneider.
On average, says the BPMA’s Wilde, using a more energy efficient motor can save about £610 over the lifetime of the motor, although he cautions, this is of course dependent on the size of motor and its efficiency rating.
Best saves
Scaled up to the macroeconomic level, the potential returns are undoubtedly impressive as Wilde outlines: “Approximately 50% of all the electricity generated across Europe is consumed by motors.
“Reports suggest that using more efficient motors could save the EU around 135 TWh per annum, which roughly equates to the annual electricity consumption of Sweden. Furthermore, some 60 million tonnes of C02 emissions will be avoided.”
The challenge with technological innovations is identifying which will best produce the efficiency/downtime saving/ sustainability gains required.
For Wilde, the best developments in recent years have been increased hydraulic designs and the onset of variable speed drives, that can better match system requirements.
As most installed pumps are oversized, fitting a variable speed drive encourages the pump unit to maintain the optimum pump system curve.
Approximately 50% of all the electricity generated across Europe is consumed by motors. Reports suggest that using more efficient motors could save the EU around 135 TWh per annum
Gary Wilde, technical services officer, BPMA
“The Affinity Laws come into play, whereby a 50% reduction in impeller speed will result in the following: the flow ‘Q’ will reduce by 50%; the Head ‘H’ will reduce by 75% to one quarter of its previous value; and the Power Consumption ‘P’ will reduce by 87.5%, to one eighth of its previous value,” states Wilde. “This is the reason why variable speed in pump applications has such importance.”
Efficiency, though, depends upon a properly holistic perspective. Not only with regards to assessing value for money in terms of life cycle rather than purchase price alone; but also through an appreciation of the various components of a system.
Solutions for improving pump effectiveness may include a range of actions, advises Wilde. These might include the addition of a variable speed drive, selecting a correctly sized pump for the task, changing the pump unit itself if very old, the removal of a throttle valve control system, the removal of any bypass lines, ensuring the correct suction or discharge pipework. Also better overall design, installation and maintenance.
“Making any number or combination of these changes could realise possible energy savings of up to 40%.”