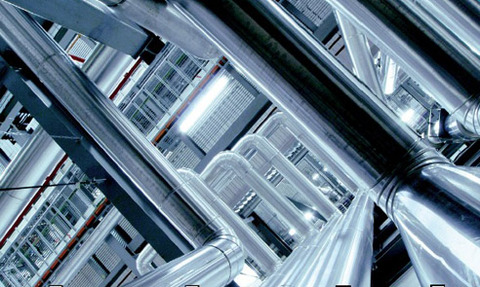
We can blame Brexit for much but there’s work for the chemicals sector to be doing around regulation and digitalisation that mustn’t stay on hold, learns Brian Attwood.
Two matters dominated the extensive agenda of this year’s ChemUK show. The first generated, predictably, by current political and economic events, the other concerning a longer term and all-embracing transformation.
Issue one was regulation and how this will look in the post-Brexit era. Departure from the European Union means quitting the umbrella of rules governing the member states and finding an alternative that ensures trade with the UK chemical sector’s largest market remains as frictionless as possible.
This entails an alignment of sorts, yet one that does not compromise the search for new markets; while, at the same time, guaranteeing the latter ambition does not undermine standards.
Issue two – digitalisation – is not specific to one sector of the process industries but its progress may inadvertently be advanced one day by the consequences of the country’s EU departure.
If they do nothing, they are leaving themselves open and, more important, leaving all employees working around these chemicals open
Mike Harris, CMS operations manager, Alcumus Sypol
Compliance and risk management specialists Alcumus are heavily involved in steering companies through the regulatory forest that encompasses three sets of chemical regulations.
As CMS operations manager for the firm’s Alcumus Sypol subsidiary, Mike Harris is well placed to assess the Brexit impact. It has, he says, slowed responses to making necessary updates to and investment in compliance. He defines the approach as one of “caution by association” – whereby businesses holding back on Brexit-related matters are similarly tardy about making decisions on those considerations not directly affected.
“People are very cautious about investing in anything and two of the three sets of regulations for chemicals management are EU regulations – so it invites hesitating around investment,” states Harris.
“If they do nothing, they are leaving themselves open and, more important, leaving all employees working around these chemicals open.”
Alcumus Sypol’s focus is the COSHH – Control of Substances Hazardous to Health – regulations, enacted under the auspices of the EU but a specifically British set of rules. From a technical point of view, says Harris, these will not be affected by Brexit. Despite this, many companies have effectively put their COSHH management strategies on hold.
Perils of doing nothing
“Back in February. Some were saying ‘we’re going to wait until the end of March’ [for the expected Brexit outcome]. Now, three months down the line, it’s still going to be x months before a decision.”
Added to which, the specialist nature of the advisory work provided by the likes of Alcumus means that, even without a Brexit-induced bottleneck, the process can take weeks or months for individual firms to complete.
“That doesn’t help the workers who might be exposed to dangerous substances every day they go to work. Seven to eight months of delay could prove catastrophic.”
Things are less clear cut when it comes to the Class Labelling Packaging (CLP) and REACH regulations. Then again, the CLP regulations align the EU with the Globally Harmonised System (GHS) – something an independent British sector must needs work within, in order to maintain and enhance its extra-European trade.
“Every piece of evidence I’ve seen says it would be madness to move away from it, so we’ll likely continue the classification because every major country we would be looking to build bigger trade with [such as the USA, Canada, Australia], they’d be using it. And, slowly but surely, a lot of other countries around the globe are converting to that.”
Harmonised global systems are a welcome theme too for Ian Elsby, head of chemical industry for Siemens UK. Referencing his White Paper delivered to the ChemUK audience, he stresses the work already happening with supply chain connectivity, linking companies to upstream suppliers with the power of digitalisation.
The problem though is that, as in the arena of chemical regulation, UK companies are doing too little while eyeing events in Europe and beyond. “We’re still at the curiosity stage. Germany and the Far East are leaping ahead,” comments Elsby.
Watching… and learning?
It’s the big corporates such as BASF that are making the running, driving digital solutions from R&D hubs with a lot of pilot projects under way, he adds.
“In the chemicals industry, we are waiting to see the success stories from others before people are willing to put their hands in their pockets and invest in digital projects. The issue is, we seem to have a lack of local case studies of digital wins in the UK – we certainly aren’t trailblazers.”
As an evangelist for the transformative nature of digitalisation, Elsby is adamant about the need for UK chemicals to develop a greater agility in order to compete globally.
“Absolutely; we’re competing with the likes of South America and South East Asia, where they do have significantly lower energy costs than we do. We’ve got to do something else to become more competitive.”
Brexit has provided greater heft to the pressure to digitalise, confirms Harris, thanks to the combination of a labour shortage and skills gap that was previously plugged with non-UK recruits.
“There are a lot of people working in these niche areas who aren’t from the UK, so it’s going to need a major education piece upskilling people. But the big push will be around digitalisation to move it away from human error. In most processes, we are the ‘things’ which cause the most problems.”
Add to this scenario, the monumental task of converting the Registration, Evaluation Authorisation and Restriction of Chemicals – or REACH – regime into a separate UK legal framework.
Whereas EU directives provide for individual legislation in member states, as an EU Regulation, REACH is directly enforced and requires some form of replication in UK form.
Already, there has been concern regarding the transformation of pesticide regulation expressed by the UK Trade Policy Observatory, the research body/think tank supported by the University of Sussex and Chatham House.
The knowledge in the chemical industry simply isn’t there; they don’t know how to ‘do’ digitalisation
Ian Elsby, head of chemical industry, Siemens UK
Authors Chloe Anthony, Ffion Thomas and Emily Lydgate asserted there were “significant” departures from EU law within the Government’s new Statutory Instruments.
In particular the trio cited “the removal of a blanket ban on hormone-disrupting chemicals” and replacement of the requirement for independent scientific evidence on pesticide safety with an option for ministers to “consider such evidence at their own discretion”.
And, while Harris appears cautiously optimistic for the future of a UK REACH supervised by the Health and Safety Executive (HSE), he retains certain caveats. In particular, the loss of the UK’s influential role in the European-wide REACH framework and the effect of previous years of HSE under-resourcing.
There is also the issue of the interaction of the EU and new UK regulations – not only the cost implications but also the potential for long-term divergence.
“I know that there is talk of the cost being borne by the company that’s importing it into the EU. However, in a lot of cases for a lot of major companies, they’ll be the ones exporting it because they have bases of operation in both Europe and the UK.
“[Also] we will have our own set of regulations aligned with the EU but does the fact they’re a different set of regulations mean there’s the possibility that we might not introduce future changes that the EU does?”
Less dirty, more digital
All of which presents the UK chemicals industry with a Catch-22 situation in which digitalisation and skills needs are intertwined, explains Elsby.
“There’s going to be a massive skills and knowledge shortage and that is where companies like Siemens are starting to have these conversations about digital transformation, because the knowledge in the chemical industry simply isn’t there; they don’t know how to ‘do’ digitalisation.”
Digitalisation or the lack of it impacts too on a company’s ability to recruit the right people, cautions Elsby. There, the chemicals sector has a problem of perception and visibility.
“You have to be appreciative of what chemicals do for our day to day lives and this lack of awareness is critical. Young people who go into the chemical industry do have the ability to make a significant impact – bigger than they would at the likes of Google and Amazon.
“They also need senior management [who] cannot be blinkered and siloed in their views, at the very top of that business. I think these two things will make the difference.”
Large firms such as the ubiquitous BASF can provide a varied business experience that ensures young engineers are not poached by the financial and other sectors. Yet, explains Elsby, the average small to medium enterprise (SME) often needs engineers and process engineers that already have the skills and ability because they lack the financial and human resources to train.
No wonder, when before implementing digital strategies, firms must first address their cyber security.
Connecting assets together creates potential risks, however. Traditional machine and process safety personnel will not be familiar with cyber security needs, says Elsby, but “the two sit side by side now, so straight away there’s a skills gap they didn’t realise they had”.
As he puts it, the holy grail of the chemicals sector is always to make sure the plant is safe – “Even before you make money, you have got to make sure it’s safe.”
“Before you go down the route of digital strategy, you’ve got to start looking at cyber security – get audits, ask where’s the gaps that are causing concerns. So there’s a cost prior to transformation.”
The chemicals industry is now included among the 13 national infrastructure sectors on the Critical National Infrastructure (CNI) list, together with those other process industry stalwarts, energy, food and water.
And, though reducing the scope for human error is a key benefit of digitalisation, the lack of awareness by personnel on-site will remain a significant risk, reminds Elsby: “The biggest challenge for cyber is still the human factor.”