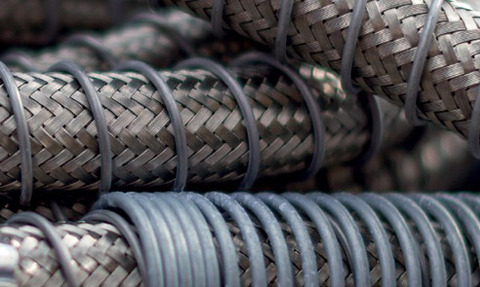
Chemicals will provide sustained business opportunities for pump companies working in the sector. And that’s not only down to digitalisation, hears Brian Attwood.
Disruption is a word that features frequently now in the vocabulary of industry. While its connotations were once almost entirely negative, now, more often than not it has become associated with opportunity and faster ways of doing business.
In Europe including the UK, several forms of transformation are affecting the sizeable chemicals industry which, say analysts Frost & Sullivan, is attempting “to redefine its value proposition”.
And, if regulatory pressures may not be uniformly welcomed by the sector, a new emphasis on sustainability and energy saving promises rewards that will stimulate growth.
Pump manufacturers offering value-added services such as end-to-end monitoring of pump performance throughout their lifecycle to increase energy efficiencies will remain competitive
Kiravani Emani, industry analyst, Frost & Sullivan
Unsurprisingly, a vast contribution to energy costs derives from the activities of pumps and their related systems. Last year, the chemicals sector produced revenues for the pumps market amounting to nearly $1.3 billion – in the region of £1 billion.
The indications are that compound annual growth for the chemical pumps market will maintain at around 2% until 2025. The challenge will be responding speedily to demand.
“Pump manufacturers offering value-added services such as end-to-end monitoring of pump performance throughout their lifecycle to increase energy efficiencies will remain competitive,” comments Frost & Sullivan industry analyst Kiravani Emani.
In addition, he says, digitalisation of chemical plants will mean another demand – for connectivity and intelligence capabilities in order to aid predictive maintenance, reduce asset failure and prevent shutdowns.
The old focus on purchase price and product range is switching to greater emphasis on performance and life cycle reliability. At the same time, advises Emani, customers will seek a more holistic approach, with remote services combining predictive and maintenance aspects to ensure continuous production.
That requires pumps companies with sufficient resources extend their offer further by being prepared to merge with automation and IIoT firms to enable chemical firms to progress towards smart manufacturing, says Emani.
It was noticeable that pumps companies comprised a significant minority component of guest speakers at one of the key chemical industries events in the UK, the recent ChemUK 2019 Show.
Focus from the floor
Among the participants leading discussions were representatives from Emerson Automation Solutions, Aesseal, Edwards Vacuum, Grundfos Pumps and the British Pump Manufacturers Association (BPMA).
Topics included pumps system auditing, extending reliability, Coriolis technology, chemical dry pumps and pumps’ role in process optimisation.
As the BPMA’s technical officer Gary Wilde pointed out at the conference, interest in pumping systems reflects the fact that overall growth rate for pumps consumption looks set to hold consistently into the next decade.
Breaking down pumps systems’ electrical consumption by sector, the lion’s share (41%) may be accounted for by commercial and public buildings, followed by water and sewage on 14%.
However, the chemicals pumps sector’s 9% outdoes any other and equals that of the oil and gas, food and drink and metal manufacturing sectors combined.
Controlling energy use by pumps reaps significant benefit for the chemicals plant but calls for the development of in-house knowledge, underlined Wilde in a talk promoting the benefits of the association’s Certified Pump System Auditor course.
“[It] aims to train engineers and technicians to understand the importance of pumping systems and how to identify the opportunities available such as, reduce operating costs, reduce carbon footprint and reduce on-site energy consumption,” he summarises.
The starting point is the realisation that energy saving and auditing requires a holistic approach – one that does not limit itself to consideration of motor and pump performance in isolation but as one part of an overall system.
[It] aims to train engineers and technicians to understand the importance of pumping systems and how to identify the opportunities available such as, reduce operating costs, reduce carbon footprint and reduce on-site energy consumption
Gary Wilde, technical officer, BPMA
Wilde says this better enables a plant to identify whether system design, pump selection, inefficient control or another factor is responsible for energy waste.
The four-day CPSA course is designed to provide solid grounding in pump analysis and hands-on auditing and is divided into three parts.
The first, the QPSAT syllabus, encompasses identification of energy saving opportunities, life cycle costing contingency planning and application of the pumping system assessment tool, and assessment of pump and motor performance characteristics among its elements.
The second component examines solutions in theory and practice, while the third covers proper use and application of ISO 14414 to assess pump systems, as well as identify opportunities for energy consumption reduction improved reliability. “It gives a common definition for what constitutes an assessment for both users and providers of assessment services. Its objective is to provide clarity for these types of services which have been variously described as energy assessments, energy audits, energy surveys and energy studies.”
Returning value
The biggest returns tend to accrue to those most in need of it. Wilde quotes the case of one process industry leader, Tate & Lyle, whose actual electric costs for the site referenced in his quoted case study amounted to more than £29,000.
Provision of a new pump working with an existing valve offered an electric cost of just £6,400; opting for a new pump and VSD with no valve produced an electric cost of £1,900. In other words, a choice between saving £22,900 or £27,400 respectively.
Pumps system efficiency is intrinsic then to the overall productivity of process and other enterprises. While external expertise will also be a necessary component for achieving this, courses such as the BPMA’s address the need that companies have to exert direct control through their own informed decision making.
Such decision making, however, depends not only on the standard of personnel training but increasingly upon the equipment employed to extract vital information and data.
Getting connected
Just as automation in the form of variable frequency drives and suchlike has increased the ability to control processes more accurately, so the advent of greater connectivity has further advanced the process.
This was referenced in a second pumps-focused seminar at the ChemUK conference by Emerson Automation Services’ Julian Spadaccini, examining the latest developments in Coriolis technology.
Coriolis flowmeters working in a chemical context must contend with harsh processes that can result in corrosion, erosion or scaling. Additionally, wearing parts and electronic failures contribute to meter degradation.
There is also a high demand for regulatory compliance with both internal and external standards such as ISO 9001 and a certainty of levels of accuracy that enable consistent processes.
Attitudes to calibration vary hugely, reports Spadaccini, leaving questions over data reliability and the causes of faulty processes. He cites the example of one customer who complained their manual calibration approach removed meters from the process, rarely identified problems and cost between £2-£5k per meter annually.
By contrast, new generation smart meter verification processes allow companies to avoid downtime calibration, put verification control in the hands of the customer and remove the need for specialised equipment.
The verification system checks tube stiffness, drive and pickup coils, RTD and electronics with values stored and complete meter and transmitter functional assurance. Even the accuracy challenges presented by multi-phase measurement can be overcome with the necessary advanced phase measurement software options available.
The right stuff
But, while digitalisation and training may be key drivers of chemical pumps efficiency, ‘traditional’ materials innovation has a place too.
Watson-Marlow Fluid Technology Group (WMFTG) scored a breakthrough for one European precipitated calcium carbonate manufacturer seeking to recycle product waste.
The PCC waste – which contained sand and water, with the slurry between 100-1,000 cPs viscosity – created lengthy downtime and costly repairs for the firm’s existing pumps.
When these were replaced by Bredel 65 pumps with 3kW motors run at 17rpm over a 24/7 duty cycle and recording flow rates of 6-10m3/h, the accompanying Bredel 65mm diameter standard natural rubber hose lasted for 3.36 million occlusions, or circa 83 days/2,000 hours.
However, by checking pump speed, heat, back pressure and product dilution, hose life was increased to 4.468 million occlusions or 110 days/2,660 hours – an improvement of 32%.
The customer was then persuaded to participate in trials of the new Bredel NR Endurance hose, constructed from high-quality compounded rubbers, reinforced with individual layers of braided nylon. Inner and outer layers are extruded and after construction, the hose machined over the entire length, to ensure critical tolerances are maintained.
Trials demonstrated a hose life of 7.056 million occlusions or 175 days/4,200 hours – a further 57% gain. Overall, WMFTG claimed a downtime reduction from 24 to two hours, achieving ROI in 12 months and saving €100,000 TCO.