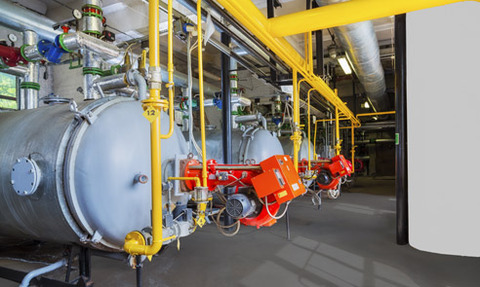
They play a crucial role in industrial processes but getting a grip on boiler and steam performance is a matter of mastering some basics while understanding when to call on experts.
Despite their vital importance to so many operations, industrial boilers and plant heating systems are often given a low priority in terms of maintenance and overhaul, reckons SUEZ Water Purification Systems’ business support divisional manager, Mark Bosley.
“This can be a costly mistake that leads to growing levels of scaling and corrosion; these will increase energy consumption and reduce heating efficiency, shorten the operating life of tubes, condensors and pipework and, in the worst case, lead to unplanned shutdown,” he warns.
But it can be a problem discerning how much a plant can do for itself on limited resources and budget. Expert help promises greater certainty yet there’s a financial cost. Not only in terms of the price of contractor time or extra salary but also the potential downtime when issues are addressed.
[Underestimating the importance of boiler maintenance] can be a costly mistake that leads to growing levels of scaling and corrosion
Mark Bosley, business support divisional manager, Mark Bosley, SUEZ
Chris Coleman, boilerhouse national specialist at Spirax Sarco, says that, where the planning, management and upgrade of steam boilers are concerned, professionals need to have a solid grounding in the fundamentals of steam to achieve better efficiency and safety.
By developing a basic understanding of the properties of steam before consulting an expert, plants are better able to address such matters as meeting specification, deadlines, budget, safety and regulatory requirements, energy efficiency targets and minimising downtime.
“Granted, there is a wealth of information available on steam systems and sometimes it can be a minefield to navigate. [The] core elements that will give you a basic understanding: the different boiler types, how steam is produced into three variants and the condensate loop. Develop your knowledge in these areas and you are already on track to an optimised solution,” says Coleman.
While shell boilers are the most common, there are many variations out there. Also, he states, three types of steam to know about – saturated, superheated and flash steam.
The manner in which steam is produced and distributed has a significant impact on potential performance as well as economy for the end user. And technical materials such as steam tables provide more detail around the properties of steam at varying pressures.
Condensate, although a much wider topic, needs to be included in terms of understanding the way it is created and should be recycled. Also, adds Coleman, a number of essential tests such as feedwater treatment, deaeration and storage.
While the need to extract maximum returns in terms of life cycle from a product is well understood, planning needs to be made too for the possibility of upgrading kit. This requires a full audit of the existing system. And, advises Coleman, “as with any piece of equipment in our industry, it will most likely not be a like-for-like for the system that is currently in place”.
There he instructs, ask two key questions: Has your facility changed in any way in terms of its requirements? Have there been any technological developments since the first install?
“By re-acquainting yourself with the fundamentals of steam, be it through written literature or industry training courses, you can build the requisite knowledge you need to identify areas of improvement so fewer problems or faults need to be dealt with in future.”
Inadequate treatment of boiler feedwater is an issue that exercises SUEZ’s Bosley [pictured]. It can, he cautions, create a high cost for manufacturing and process businesses, due to the aforementioned scaling and corrosion.
Water contains dissolved gases, including oxygen, carbon dioxide and minerals, and when heated and pressurised these can attack metal surfaces, causing corrosion, before being deposited as scale: “Corrosion tends to produce localised pitting, can also cause systems to fail without warning, while scale lowers the efficiency of heat transfer and liquid flow.”
For modern boilers, with high heat transfer rates and efficiencies, says Bosley, feedwater quality specification is crucial.
“Water must be carefully treated, monitored and managed. Both the raw feedwater and the condensate returning from steam circulation need to be appropriately purified using a combination of equipment and chemicals.”
The chief scaling elements, calcium and magnesium, should be removed before reaching the boiler. One approach is water softening. This process uses brine to regenerate a resin which replaces calcium and magnesium with sodium. Yet, as no single treatment is totally efficient, chemicals are also added to the boiler.
A side effect of softening is an increase in total dissolved solids that can produce a form of scaling, as well as foaming and loss of boiler water level control, says Bosley.
“In such a situation, boiling water may be ejected into the steam main and damage pipework designed for gaseous flow. To avoid this, water at the bottom is periodically discarded or ‘blown down’ to remove excess solids.”
[The] core elements that will give you a basic understanding: the different boiler types, how steam is produced into three variants and the condensate loop. Develop your knowledge in these areas and you are already on track to an optimised solution
Chris Coleman, boilerhouse national specialist, Spirax Sarco
Alternative pre-treatment methods include deionisation (DI) and reverse osmosis (RO) which stop scaling and foaming, reducing the need for blowdown and energy efficiency. Also, electro-deionisation (EDI), in which ion capture resins are regenerated using electrical potential. Finally, reverse osmosis involves water passing under pressure through a semi-permeable membrane which can remove 96-98% of the dissolved ions.
However, these scaling treatments make water more corrosive and require additional chemicals to lessen that effect, adds Bosley.
Dissolved oxygen and incorrect pH are the main corrosion agents. Bosley recommends heating and stripping with steam in a hotwell or deaerator to remove much of the oxygen, but chemicals are required too. Sulphite is one option but adds to the total dissolved solids, whereas oxygen-reducing organic chemicals do not increase solids but are unsuitable for certain steam uses.
Maintaining an alkaline pH minimises corrosion, but if this involves excessive use of sodium hydroxide (caustic soda) this can corrode iron and increase solid levels. For demineralised water alkalinity can be maintained by chemicals including phosphates and amines.
‘With awareness of scaling and corrosion issues, and proactive investment in water treatment, monitoring and management, the boiler’s efficiency, uptime, longevity and cost control are all improved,’ states Bosley.
Calling the experts in
At some point however, external expertise may be needed. Not surprisingly as he’s service sales manager UK and Ireland for his company, another of Spirax Sarco’s authorities, Iain Harper, is an advocate of outsourcing maintenance work.
“A service contract is a flexible way to make sure that a plant maintains peak operational efficiency, ensures equipment longevity and gives the customer peace of mind that all their equipment is safely maintained by dedicated engineers,” he asserts.
It comes down he says to two factors. Firstly, freedom of choice: “Whether old equipment has been replaced to update the plant, or a completely new system has been installed, [you] choose a level of support to match the needs and budget of the plant manager. What’s more, maintenance can take place on site to limit business downtime. This can fit around any plant shutdowns or planned maintenance.”
Secondly, it offers predictability and peace of mind as a service contract gives priority over those without a contract in place, ensuring that they receive the support they need when it is most needed. Don’t overlook, too, the wealth of external advice to be had in the form of free online assistance. The Healthy & Safety Executive risk assessment information provide useful primers on such matters.