Clean steam provides a green option to counter contamination
13 Nov 2019
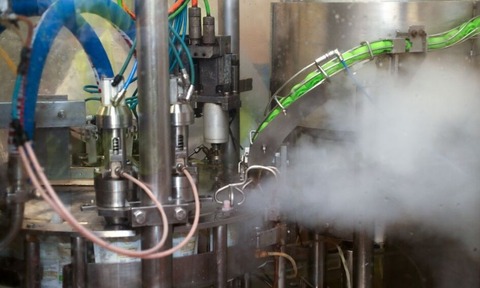
The Natural Fruit & Beverage Co. embarked on a project to transition to clean steam generation for its packing process while minimising the risk of contamination...
Manufacturing manager at the Natural Fruit & Beverage Co. Jamie Walker was approached by a key customer looking to enhance the quality of their product.
The product in question was baby fruit puree sachet pouches; Walker’s employer, meanwhile, is one of the UK’s leading packers of food products into resealable pouches.
Natural Fruit’s client wanted to differentiate itself from the competition in order to secure supermarket contracts. Walker saw an opportunity by focusing on the cleaning process.
The client wanted to differentiate itself in order to secure contracts. Walker saw an opportunity by focusing on the cleaning process
The firm had been using CO2 for purging and cleaning excessive residue before capping the product. Not only was there little room for improvement in the method, it was also expensive.
Consulting experts for an alternative method Walker decided to explore the potential of steam.
There were questions regarding potential contamination of the pipework running the risk of affecting the consistency of the product and confusion surrounding which steam type would be best for the process.
Walker initially believed the best solution might be a cost-effective filtration process but this highlighted the common confusion in the industry regarding the difference between filtered and clean.
So he called in steam specialist Spirax Sarco who presented to the Natural Fruit & Beverage Co management team.
They explained the various types of steam, the concept of clean steam as an ingredient and how it applies in relation to a Hazard Analysis and Critical Control Point (HACCP).
The specialist engineers explained that, despite the food and drinks manufacturer having made use of filtered steam in the production process, by choosing clean steam a consistency in taste, colour and quality of the end product could be achieved.
Filtered steam is plant steam that has passed through a filter and removes 95% of all particles larger than 2µm.
However the EU Regulation (EC) No. 852/2004 States steam used directly in contact with food must not contain any substance that “presents a hazard to health or is likely to contaminate the food”.
Generating and using clean steam within a process means controlling feedwater quality at the source. Rather than relying on a filtration process to extract particulates, the production of clean steam utilises a secondary steam generator with the ability to control chemical-free feedwater quality.
Prompted by the Spirax demonstration, Natural Fruit & Beverage Co. introduced an electric compact clean steam generator 50 kW (50 kg/h @ 3 bar) with preheating capability and the ability to control feedwater quality. The new operation was supported by site visits from the Spirax Sarco specialist engineers to help boost in-house understanding of the innovation.
Walker commented: “The Spirax Sarco team gave me the confidence and security that they knew the subject well enough to introduce a clean steam generator rather than filtered steam.”
Clean Steam Specialist at Spirax Sarco Francisco Pedrosa said the process represented an opportunity for many other businesses whose operations were broadly similar to those of Walker’s employer.
“There are many companies across the country that use the same processes as Natural Fruit & Beverage Co., and yet do not realise the full potential of clean steam,” he concluded.