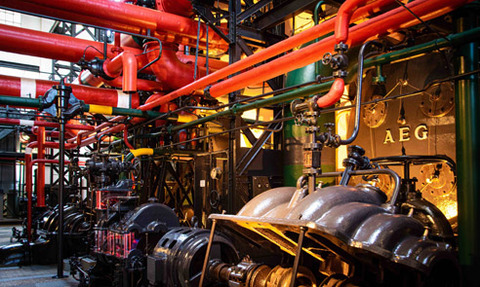
The ad hoc, ‘one asset at a time’ route to improving energy efficiency has undoubtedly brought improvements. A more fundamental approach is needed now, suggests Michelle Knott.
Suppliers have made great strides in improving the energy efficiency of individual items of electrically powered process equipment. However, many industrial sites could go much further by managing their electrical energy supply more effectively, rather than sticking to a piecemeal approach.
Alex Mardapittas, CEO of smart energy solution provider Powerstar, is an advocate of this approach: “To meet the challenges posed by the need to decarbonise energy, whilst also becoming increasingly reliant upon it, businesses are increasingly looking for ways in which they can implement a comprehensive energy strategy.
“This is achieved by deploying solutions that provide the four core components of the flexible power future – energy efficiency, energy flexibility, power resilience and actionable insights.”
There is an opportunity to regulate the pressure more towards mainland European levels to protect the device and maintain its designed life span
Alex Mardapittas, CEO, Powerstar
Different energy management measures will provide the best way forward for different sites, but there are some key approaches that deserve a mention.
First is voltage optimisation, which can typically shave between six and 15% off the electrical energy consumed by an industrial installation in the UK, although that will vary according to the application.
Put simply, voltage optimisation aims to match the voltage coming into an electrical device more precisely to the requirements of that device. This might mean installing a transformer to control the voltage coming into the overall site or it might mean using separate transformers to target devices where controlling the voltage will make the biggest difference.
Look east
“There are many sites across Europe where voltage optimisation can save energy, but it is especially useful in the UK, where historical reasons mean that the incoming voltage is often higher than needed,” explains Stephen Vizard, business development manager for energy-saving specialist EnergyAce.
The single-phase supply voltage in the UK was 240V for many years, while European levels were based on a 220V system.
Today, CE-marked electrical devices across the EU are designed to operate at around 230V, rather than the average voltage in the UK, which remains at around 242V in practice, despite efforts towards harmonisation.
This makes little difference to the power consumption of some types of equipment, but for voltage-dependent loads, it means more energy is being used than necessary.
“Voltage optimisation improves efficiency by optimising the incoming voltage to a site which consequently leads to a reduction in the site’s overall electricity consumption and costs,” says Mardapittas [pictured]. “Amorphous alloy core distribution transformers provide an upgrade on conventional transformers by providing a quicker rate of magnetisation which leads to lower losses and improved efficiencies to ageing high-voltage infrastructure.”
Voltage optimisation also has other advantages. “Consideration should also be given towards accelerated deterioration of the electrical device at the higher voltage levels,” says Vizard. “Voltage can be described as a pressure, there is therefore an opportunity to regulate the pressure more towards mainland European levels to protect the device and maintain its designed life span.”
Power factor correction is another important tool for managing electrical energy. It’s important because the power factor is a measure of how much of the energy supplied is available to do actual work.
In simple terms, the power factor drops away if the current and voltage in an AC supply are out of phase, which tends to happen when there are induction motors in the system. When that happens, only some of the power entering the system is useful, with the rest termed reactive power. “We find it helpful to visualise it as a pint glass, with the beer being the useful power while the head is wasted or reactive power,” says Vizard.
While the ideal power factor is 1.00 (i.e. a full glass with no head), some sites can drop as low as 0.50. Power factor correction brings the current and voltage back into sync, achieving an efficient power factor closer to 0.95.
Getting it right
It’s achieved by introducing an array of capacitors into the system. These can be added or subtracted to offset the amount of induction in the system at the time. So, for example, if fewer induction motors are being used overnight, the power factor will naturally be closer to 1.00 and fewer capacitors will be needed in order to compensate.
Correcting the power factor offers knock-on benefits in terms of the capital investment required in the electricity network, says Vizard: “A site operating on a power factor close to unity would require less investment in associated power plant… Investments into costly network upgrades due to an overloaded electrical supply can be avoided by improving power factor and at a fraction of the cost of an upgrade.”
Remote metering and monitoring are becoming more important for managing energy as Industry 4.0 and the Industrial Internet of Things continue to gain ground. “First stage of any scheme is to gather accurate information and data on your existing energy consumption and efficiency,” says Vizard.
Boltage optimisation can save energy, but it is especially useful in the UK, where historical reasons mean that the incoming voltage is often higher than needed
Stephen Vizard, business development manager, EnergyAce.
Beyond this initial data-gathering exercise, Mardapittas stresses the importance of the right ‘front end’ systems to help companies turn their energy data into actionable insights: “Actionable insights are provided through the remote monitoring capabilities of the respective technologies. The key performance characteristics of each asset are visible through a single portal, [enabling] users to turn insights into actions and implement optimisations that could improve the performance of the energy profile.”
In addition to being the responsible thing to do for the environment, targeting energy efficiency also improves the bottom line. With that in mind, Mardapittas says that the biggest business boost comes when companies implement efficiency measures alongside systems designed to boost the flexibility and resilience of their power supplies. This helps prevent any issues with the supply from impacting on other aspects of their operations.
“Benefits of a comprehensive energy strategy can be defined in terms of the return on investment [it provides...] a large proportion of the revenue and savings are achieved from offsetting energy, and operational savings due to increased resilience and energy optimisation. This accumulates to a typical payback period of four to six years with a typical return on investment of up to 25%.”
Harvest time
One way to keep a grip on electrical energy consumption is to rely on technology thatbypasses the need for it
Not only can monitoring networks help save energy, but energy harvesting sensors can do so without consuming electrical energy. This helps to eliminate wiring and the need to replace batteries.
“Installing a sensor network using copper wire, conduit and supporting infrastructure can be extremely cost-prohibitive for manufacturers, especially if they are only just starting to incorporate smart technology in their factory,” says Sophie Hand, UK country manager for global automation parts supplier EU Automation.
“While there are wireless protocols for sensors, such as ZigBee, Bluetooth and 6LowPAN, which eliminate data communications wiring, the sensors still need to be powered by something. Often, manufacturers opt for batteries.
“However, ON World research has predicted that battery change-out costs $1 billion per year. Clearly, the industry needs an alternative.”
Energy harvesting sensors operate by gathering energy such as kinetic, solar and thermal power from their surroundings and turning it into electric power. As a result, these sensors require no batteries to gather or send data.
“Applying these devices in a machine-to-machine (M2M) sensor network could eliminate the need for grid-based power and primary batteries, creating a maintenancefree, battery-free and cable-free way of gathering and transmitting data in a manufacturing facility,” says Hand.