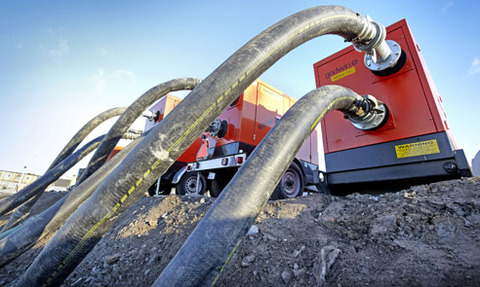
Sustainability, connectivity and the legislative framework are shaping water use across process sectors but how do these issues impact at the sharp end? Brian Attwood reports.
Water, its future availability and the means by which we use it are all subjects that lend themselves easily to the sort of ‘blue sky’ thinking that keeps event organisers well stocked with attendees.
Valuable stuff of course and an opportunity to share in the strategic mindset of regulators and major operators but often a prelude to more nitty gritty matters. Once a broad picture has been drawn of how things need to change, the challenge that follows is to ascertain how one delivers in practical terms.
The pumps sector of course is intrinsic to this delivery, providing many of the key tools and processes to actually realise schemes.
Yet it is hardly surprising that, in an increasingly connected world, it has become harder to focus on nuts and bolts implementation alone. Pumps products and ways of working are now too interconnected with concepts of automation and smart systems and cannot advance without them.
Greg Hookings [pictured below], head of business development – digitalisation at Stratus Technologies, cites the regulator’s recent heavy emphasis on asset health. While it may be indirectly serve as a pressure for digitalisation transformation (or Dx) in the industry, he sees this as “a natural step” rather than an explicit push.
“Dx makes sense. Asset-health is not just about reporting the status of assets. Dx unlocks the potential of assets and empowers organisations to adopt predictive maintenance strategies.
“With the ability to look ahead, organisations can prevent costly failures, reduce downtime, and focus on shaping what’s next. With improved analysis, it is possible to eliminate inefficiencies, optimise operations and improve profitability.”
David Amory, global head of marketing for AESSEAL, warns the external pressures are too great to ignore the need for change.
The water paradox
He cites international water lobby and advisory group CDP’s Treading Water report: to the effect that, while the number of companies setting targets to reduce water withdrawals doubled between 2015 and 2018, simultaneously, there was an almost 50% rise in the number reporting higher water withdrawals.
While their focus may differ, both Amory and Hookings are agreed on the business case for sustainable practice. As a starting point for embedding sustainability within a workplace culture in and ensuring that good intentions are converted into practical implementation, Amory suggests the following:
- Eliminate all water waste beyond the absolute minimum required for the efficient functioning of rotating equipment and the process
- Eradicate the leakage that leads to product dilution
- Improve reliability and put an end to unscheduled downtime
- Make significant energy savings
- Achieve swift return on investment and long-term operational savings
“If every company took an in-depth look at where water was being used to excess in their processes it’s guaranteed that certain repeat offenders would appear across all industries,” advises Amory.
Hookings’ summary of the key challenges mirrors those of the regulator and can be characterised, he says, in terms of cost, environment and resilience.
“To break these down further in detail: costs – relating to all involved, that’s customers, site managers and utilities providers alike. As an energy intensive process, wholesale power prices will always be a factor for providers.
“Environment and resilience are other key constant factors for the water industry. Climate change and a growing population are pushing ageing hardware to its limits, and with ever-increasing environmental standards – the pressure has never been higher for utilities providers.”
Smarter assessment
Better data underpins most of the substantial advances to be made in the pumps, valves and flow sector, as elsewhere in the process industries. And that makes movement to smart systems a necessity in order to access digital information.
“However, many devices deployed in the water industry are not smart, they were deployed more than a decade to ago, and ripping all this infrastructure out is too costly to bear. We need ways to connect to these legacy assets.”
Cloud computing opened the door to accessing real-time data, Hookings acknowledges, but the water industry has presented specific challenges, not least in terms of tracking adequately its pipeline and pumping processes.
This has been compounded by the prevalence of those legacy assets – often too numerous and too costly to simply replace.
“Previously the idea was to connect systems to the Cloud. However, connecting the old with the new was largely a failed concept due to connectivity and the costs of managing data offsite.
“Emergence of edge computing provides a significant enabler to connecting the legacy assets and providing the ability to identify and analyse the all-important data, nowadays we can run advanced software that improves decisionmaking leading to improvement in the overall performance of facilities,” he asserts.
However, even as representative of a leading edge computing proponent, Hookings allows that organisational objective will determine the balance with Cloud computing within a sector.
“Specifically with the water industry and the need for insights about operational performance we see a high deployment rate in edge computing. This is because many physical sights are unmanned and or remote, but there is a need to obtain visibility into operations.”
Sustainability does not however depend upon macro-level initiatives and cutting-edge digitalisation only. Amory offers a more parochial focus to tackle those ‘repeat offenders’ he references above – namely the gland packing and single mechanical seals used to seal process pumps.
Both need substantial quantities of clean, cool water to provide lubrication and prevent overheating, yet display flaws with leakage causing product loss and contamination, he asserts.
Worse, the bulk of seal flush water to provide this cooling lubrication, goes down the drain or is evaporated off at the end of the cycle.
“In a typical application, where water is measured for one minute, around six to12 litres (1.6 to 3.17 gallons) of flush water is required. In continuous operation that amounts to roughly 3.2 to 6.3 million litres (0.8 to 1.6 million gallons) per year, for each seal (or pump),” says Amory.
“Typical industrial process plants can have hundreds of pumps so that’s an unacceptable level of waste by anybody’s standards.”
Double mechanical seals and a water management support system eliminates costly leakage, improves pump reliability and reduces seal flush water required to virtually zero, he adds.
If sustainability comes at a price, one needs to factor in the savings too. Amory quotes the example of a paper mill that reduced energy use by 50,000 MMBtu per year, saving more than £400,000 to give a return on investment of less than four months. Add to that the elimination of much equipment, frequent repair/ replacement and maintenance engineer costs plus effluent charges.
Aiming hire
Sustainability and climate change is also influencing the market in a beneficial way, as many business opt not only for outsourcing expertise but also greater reliance upon rental solutions.
The UK and Ireland’s increasingly unpredictable weather, including drought and flood, has led pumps company Xylem – itself a pioneer in integrated intelligence products such as the Flygt brand – to announce a new European rental hub.
If every company took an in-depth look at where water was being used to excess in their processes it’s guaranteed that certain repeat offenders would appear across all industries
David Amory, global head of marketing, AESSEAL
Boasting 6,000 assets to hire across 80 sites, the aim is to provide no acquisition, storage or maintenance costs, calculating that rental provides significant advantages across a range of applications as a competitive alternative to outright purchase.
“Unfortunately, due to climate change, there is a risk that heavy rainfall can cause damage to wastewater infrastructure or to communities’ drinking water networks. Now, we can cover all of these demands and ensure continued operation with a fast response service and installation,” says Andy Grewar, general manager service and rental.
Likewise, pipeline equipment provider PSS Hire expanded its pressure testing hire fleet for the water industry market.
Its new IGN 4-01-03 compliant commissioning solution uses Tibiis Bluetooth data loggers in conjunction with the Piped App to provide live alerts to supervisors and instant, automated test results on site and online.
Director Mark Hamilton said the product offering would be aimed at water companies with PR19 and AMP7 obligations, due to its focus on data capture, assurance.
To cope with demand the firm recently qualified many service engineers and rental managers in the EUSR-accredited Pipeline Commissioning Technician course.