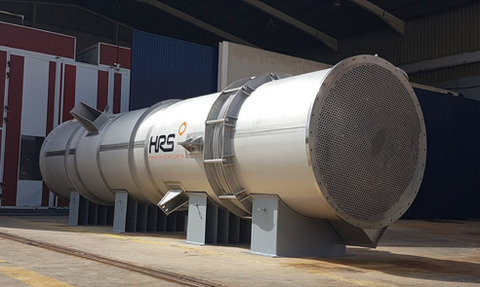
Process operators deploying heat exchange technology realise there’s an appreciable gain to be had in terms of energy efficiency – good for business and environment, explains Louisa Hearn.
With energy efficiency a perennially hot topic in the industrial sector, heat exchanger technology is becoming widely accepted as a sustainable path to heating or cooling of critical processes throughout the plant.
But while their energy saving potential is gaining attention, the return on investment of the technology is highly dependent on selecting correctly specified equipment, say experts.
Due to their energy efficient design, heat exchangers can boost sustainability across numerous industrial processes, says Matt Hale, international sales and marketing director at HRS Heat Exchangers.
Choosing a unit which represents a cheaper capital outlay but which is less energy efficient in use, or which requires more frequent cleaning or maintenance, is not only false economy in monetary terms, but it will consume more resources in terms of energy, equipment and manpower over its operating life
Matt Hale, international sales and marketing director, HRS Heat Exchangers
Optimising the energy used throughout different stages of a heat-controlled process, such as evaporation, can also benefit the bottom line.
“When combined with heat regeneration, heat exchangers can deliver savings of up to 70% compared to other options,” says Hale.
“That is why we are increasingly seeing their use in a wide range of applications including water and sludge treatment, drying and concentration fine foods and ingredients, and waste treatment including zero waste discharge projects.”
However, one of the key considerations for businesses hoping to reap these sustainability benefits will be the operational life of a heat exchanger, says Hale.
This is not just in regard to their length of service, but also in environmental terms. “For example, choosing a unit which represents a cheaper capital outlay but which is less energy efficient in use, or which requires more frequent cleaning or maintenance, is not only false economy in monetary terms, but it will consume more resources in terms of energy, equipment and manpower over its operating life,” he says.
Hale adds there are many common mistakes that can occur as a result of poorly specified or wrongly installed heat exchanger systems, from choosing the wrong materials or unit location, to having insufficient maintenance, cleaning or safety backups in place.
The ramifications of these can range from “mild inconvenience or extra costs, through to severe and catastrophic equipment failure”, Hale warns.
HRS recently installed a unit at an AD site located within a large waste management operator in the UK, which transforms food waste from domestic and commercial sources into renewable electricity and high-value digestate biofertiliser.
[Failure to prioritise heating systems] leads to growing levels of scaling and corrosion. These will increase energy consumption and reduce heating efficiency, shorten operating life… and lead to unplanned shutdown
Mark Bosley, product manager, SUEZ Water Purification Systems
The plant reuses energy across all stages of its processes, including the hot exhaust gases generated by the combined heat and power (CHP) engines that transform the biogas from the plant into heat and electricity.
According to HRS, heat exchangers used for exhaust gas heat recovery must be especially robust to cope with the physical and chemical stresses imposed on them from the hot and corrosive exhaust gases emitted in the process.
The AD plant’s original heat exchanger was fitted to the exhaust system but had failed after just a few years of operation.
HRS was commissioned to provide a replacement and selected an HRS G Series gas cooling heat exchanger, which comprised a completely stainless steel multi-tube heat exchanger specifically designed for exhaust gas cooling and thermal recovery.
According to Hale, the use of stainless steel was a key factor behind the decision, because it was corrosion of the original carbon steel unit that had contributed to the failure of the original.
“All HRS tubular heat exchangers include bellows in their design to allow for thermal expansion,” he says. “The original heat exchanger we replaced was exposed to significant thermal stresses which contributed to its early failure.”
Because of the potential for failure in a poorly specified system, safety is also a prime concern when it comes to selecting and maintaining equipment. Hale says any equipment deemed potentially unsafe should not be used until it has been checked and certified by a competent authority.
“For less serious issues, if you find that processing is taking longer than anticipated, or you are spending longer than expected cleaning your heat exchanger, it may be time to get a second opinion.” Water wise Inadequate treatment of feedwater to heat exchange equipment can also cost manufacturing and process businesses dearly over time, says Mark Bosley, product manager at SUEZ Water Purification Systems.
Despite their importance to many operations plant wide, he says plant heating systems are often given a low priority when it comes to maintenance and overhaul.
“This can be a costly mistake that leads to growing levels of scaling and corrosion. These will increase energy consumption and reduce heating efficiency, shorten the operating life of tubes, condensers and pipework and, in the worst case, lead to unplanned shutdown,” he says.
Minerals and dissolved gases such as oxygen and carbon dioxide can often attack metal surfaces when heated and pressurised, which can result in a build up of scale and cause corrosion.
Scale can impact on the efficiency of heat transfer and liquid flow, says Bosley. Strategies for dealing with the issue include water softening, using brine to regenerate a resin which replaces calcium, and magnesium with sodium. And an alternative pre-treatment is demineralisation, which is otherwise known as deionisation and reverse osmosis, says Bosley.
When it comes to the problem of corrosion, Bosley warns that it can produce localised pitting, that can cause systems to fail without warning.
Dissolved oxygen and incorrect pH are the main causes of corrosion, which he says can be avoided by managing the levels of oxygen and maintaining an alkaline pH using a range of chemicals.
Equipment efficiency, uptime, longevity and cost control can all be improved with “awareness of scaling and corrosion issues, and proactive investment in water treatment, monitoring and management”, says Bosley.
Fluid factors
Not all heat exchange equipment uses water as its medium, with a wide range of thermal fluids increasingly being deployed to maximise efficiency and heat transfer.
UK-based Thermal Fluid Solutions (TFS) launched a new form of thermal fluid filtration technology last year, designed to remove particulate matter measuring less than 20 microns.
The company says that it can target matter too small to be captured by conventional techniques, such as the carbon solids formed as a result of oxidisation of thermal oil used at high temperatures.
This matter can compromise the performance of critical components, the company says. “Our work with process manufacturers worldwide demonstrated that, while growing numbers were adopting ongoing risk management policies to ensure that their thermal fluid systems complied with health and safety legislation, many systems were operating inefficiently due to a build-up of matter that escaped conventional filtration,” says Richard Franklin, TFS managing director.
These can form deposits, restricting flow and reducing the heat transfer capability of the system, which, if left unchecked, can become blocked and cease to work. The company estimates that about 80% of particulate matter is below the 20 micron minimum size handled by conventional full flow filter mesh filtration techniques traditionally deployed in this region.
The depositional filtration units work by re-routing oil from live thermal fluid systems, and then running it through fine filters to remove solids, without the need for any down time. “Our pioneering new depositional filtration technique…captures that elusive 80% or so of particulate matter, so enabling manufacturers to keep their systems clean, efficient and cost-effective,” says Franklin.