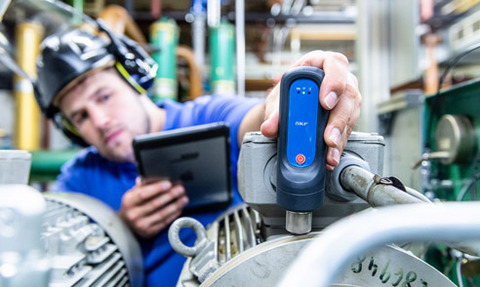
Developing technology is ramping up the potential of condition monitoring while decreasing costs make it possible for more companies. Good timing, reports Nicola Curtis, since current business pressures indicate need is growing.
Across much of the process industry, cost and efficiency has been the traditional motivation behind the adoption of condition monitoring. Although it remains the key driver, more recently, other business pressures are also beginning to emerge as major factors.
Geraint Jones, technical manager service delivery – reliability services, SKF UK has witnessed the concept of compliance appearing as a more recent core driver for the uptake of condition monitoring.
“In the marine industry, for example, if you’re registered with Lloyds you can potentially defer maintenance by demonstrating you’ve done some condition monitoring and, therefore, you might not have to remove large pieces of equipment like thrusters or main engines every few years,” he says.
“That’s a massive cost saving so clearly that remains a driving force but actually – it’s about compliance.”
What we’re going to see with the second or third generation of these kind of sensors is some sort of inbuilt analysis going on in the sensor itself. This is quite a departure from what we’ve seen in the past
Geraint Jones, technical manager service delivery – reliability services, SKF UK
The need to avoid reputational damage is another influence creeping into the mix according to Jones. With everybody on social media these days bad news travels fast. Paying meticulous attention to asset condition therefore makes good all-round commercial sense.
Current trends
Recent advances in machine-learning are paving the way for a much smarter process of condition monitoring – crucial anomaly detection, for example, is becoming far more sophisticated. Automated decision-making is another key trend to emerge as a result.
“Prognosis has always been really difficult to do,” says Jones. “It’s a very challenging concept to really be able to understand how long a machine component, for example, has got to run until it breaks.”
Data integration, another hot topic, is getting better too. Although Jones notes that there’s still some work to do.
And the concept of the traditional monitoring loop – where you collect data from a machine, analyse it, write a report, feedback to a client and then do the same again many times over – is changing too.
“There are now a lot of other ways you can convert that data to knowledge. At SKF we refer to ‘actionable insights’ where we’re taking not just a trend of vibration data, for example, but we actually want to say something about the performance of the machine, the combination of data and the defect that we’re seeing,” says Jones.
“You can then feed these ‘actionable insights’ into many things – it could be the supply chain, it could be field maintenance, it could be engineering knowledge.”
New products
Along with advancing technology and evolving trends come a raft of new products. Wireless sensors are becoming more prevalent and, with the cost of the networks decreasing, it’s becoming more cost effective to start using them.
They are also getting smarter. The days of a sensor simply waking up, passing data onto an acquisition device or Cloud, and then going back to sleep again are numbered.
“What we’re going to see with the second or third generation of these kind of sensors is some sort of inbuilt analysis going on in the sensor itself. This is quite a departure from what we’ve seen in the past,” says Jones.
Jones also notes that the cost difference between offline systems – where data is collected periodically, and online systems – which scan continuously and will collect and store data at whatever interval you want, is also diminishing.
“Typically, those online systems have been much more expensive than offline systems – but costs are coming down. As a result, companies may now be able to monitor equipment they might not have done previously because it wasn’t cost-effective to do so. And for those companies who haven’t embraced condition monitoring at all because they saw it as too expensive there is now an entry level.”
Emerson has introduced the AMS Wireless Vibration Monitor, a low-cost, easy-to-deploy vibration sensor that performs prescriptive analytics on vibration data using native software to automatically identify failure modes and prevent potential problems involving rotating assets.
The new compact device makes it economically feasible to fully monitor motors, pumps, fans and other critical plant equipment.
“Thanks to the embedded prescriptive analytics, plant managers can add wireless vibration monitoring to their maintenance toolbox without having to train current staff to perform complex analysis,” says Robert Skeirik, director of machinery health solutions product management, Emerson Automation Solutions.
The SKF Enlight ProCollect is another new, portable vibration monitoring solution designed to help companies adopt smart condition-based maintenance approaches, or for those seeking to extend their machine monitoring programmes to a wider range of assets.
Thanks to the embedded prescriptive analytics, plant managers can add wireless vibration monitoring to their maintenance toolbox without having to train current staff to perform complex analysis
Robert Skeirik, machinery health solutions product management, Emerson
Barrie Rodgers, product line manager – mobile solutions at SKF, notes that ownership of Enlight ProCollect is as flexible as its use. Customers can opt to buy the solution outright or choose a subscription approach that provides all the hardware, software and support services they need for a fixed monthly fee.
“Our subscription model allows companies to shift the costs of maintenance programme improvements from CAPEX to OPEX.
“They can easily extend their agreement to include other equipment and services – such as bearings or lubrication,” Rodgers adds.
Customers can even shift to performance-based pricing models that reduce the costs and risks associated with the transition to advanced condition-based and predictive reliability approaches.
Obstacles to success
Despite the new, versatile and cheaper products that are now on the market there are still obstacles to overcome to ensure the success of a condition monitoring programme.
Greg Hookings, head of business development – digitalisation at Stratus Technologies, notes that accessing legacy control systems can be a challenge as well as access to data or poor quality of actual data. SKF’s Geraint Jones believes there are two distinct parts to achieving success. The first part to get right is the system set-up while the second key element is the closure of the maintenance loop.
“There are a lot of obstacles around setting up your system. Cloud access, cyber security – where there’s a need to allow third party access to internal company databases. There’s a lot of nervousness about doing that but it’s essential if we’re really going to get these databases joined together,” he says.
“And then as usual in the programme itself it’s how do you go back and close the maintenance loop? This is one of the largest difficulties. We’ve collected some data and we’ve reported on it. We’ve even given some real knowledge insights to a company – what happens next?”
While a run-to-failure mentality still exists, with advancing technology and decreasing costs, it’s becoming harder to deny the benefits of condition-based maintenance which is set up correctly from the outset and utilises the right equipment to do the monitoring.