Efficient pumps pay their way in ROI
30 Apr 2020
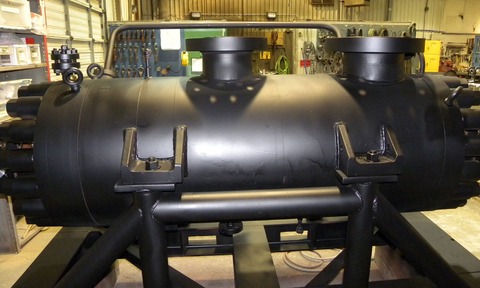
A refinery achieved improved performance from its pumps with help from Sulzer to deliver a return on investment in just 35 days...
Demand for ultra-low sulphur diesel (ULSD) has increased significantly, thanks to increasingly stringent rules, leaving refineries searching for innovative solutions to meet increasing capacity.
One US refinery turned to Sulzer to investigate possible solutions that hinged on two pumps were originally sold in 2006 at a rated point of 1,110 gpm (252 m3/hr) at 4’014 ft (1,223 m). The refinery aimed for a capacity increase to 1’628 gpm (370 m3/hr) at 3’450 ft (1’052 m). The goal for Sulzer was to find the most economical and timely solution.
Of the options available, parallel operation of the existing pumps was least costly to achieve the increase in flow. However, the risks in the event of a failure could prove costly in terms of lost production. A new pump selection to fit the application could be advantageous with regards to efficiency but involve long lead times, the cost to reroute pipework.
Re-rating was the chosen option instead. Sulzer engineers conducted a thorough feasibility study both hydraulically and mechanically to determine whether the goal was possible. A specific speed (Ns) based search through Sulzer’s vast hydraulic database revealed an existing proven design that would meet the client’s needs.
A mechanical cutback was done to achieve both an increase in nozzle area and lip diameter. The outlet vanes of the impeller were underfiled to increase the outlet area between vanes (OABV) flattened the performance curve and pushed the best efficiency point to achieve higher flows.
Challenges and drawbacks
With a major re-rate such as this, it can be rather difficult to fit a new, relatively large, high capacity impeller within the existing volute. Fortunately, the pumps in this example were originally equipped with a relatively low flow rotor compared to its frame size, which offered more room to work. In order to accommodate the increased impeller outlet width, the volute side walls required widening or “slabbing” to ensure adequate side-room clearance important to centrifugal pumps.
Re-rate required no changes to the footprint of the existing pump, saving valuable time in completing the project
In addition, the inner-case line bore diameter was increased to accommodate the larger impeller eye diameter. Increased pump performance required more power than the original 1’250 hp (932 kW) motor could deliver, so a new motor was required to meet this demand.
The Net Positive Suction Head Required (NPSHR) had increased with the new selected suction impeller. However, this was not a problem as the Net Positive Suction Head Available (NPSHA) was adequate.
Customer advantages
The decision to re-rate the existing pumps rather than buying new was more economical, especially since the outer barrel alone is a very high-priced component.
Re-rate required no changes to the footprint of the existing pump, saving valuable time in completing the project. If a new pump had been specified, baseplate modifications and the rerouting of suction and discharge pipework would have been required.
The hydraulic modifications were all confined to the inner-bundle, allowing the outer-barrel to remain piped up in the refinery. This had a significantly positive effect on the overall delivery time for the project and the much shorter completion date proved very attractive to the customer with ROI achieved in just over one month.