High efficiency and low shear pumping solution
5 Aug 2020
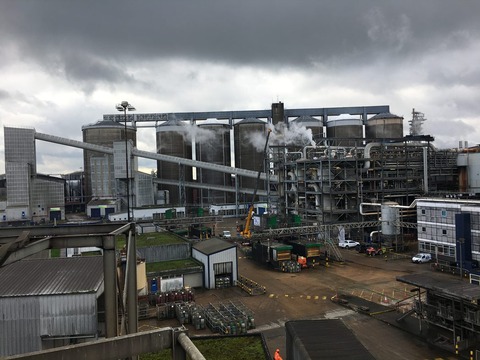
The UK’s only sugar beet producer needed to combine high efficiency with low shear pumping and velocity. It turned to Hidrostal for help.
Hidrostal, the Swiss manufacturer of pumping product to the food processing industry, has provided the leading sugar producer in Britain with pumps to enhance their sugar extraction process.
British Sugar is the sole producer of the UK’s beet sugar crop. The company processes around 8 million tonnes of sugar beet per year, to produce up to 1.4 million tonnes of sugar from their four manufacturing plants.
Unique role
The advanced manufacturing plant in Wissington is British Sugar’s largest factory and one of the most efficient sugar processing sites in Europe. At Wissington they process more than 3 million tonnes of sugar beet produced by more than 1,000 growers from surrounding counties.
After the sugar beet is harvested and off-loaded at the factory, it is washed and mechanically sliced into ‘cossettes’ – thin, V-shaped strips which offer the maximum surface area for sugar extraction. The cossettes are then passed to a diffuser to extract the sugar content into a water solution in a process known as leaching.
Pumping sugar beet cossettes requires delicate handling in order to extract the maximum amount of sugar, without damaging the crop. Hidrostal’s pumps are the ideal solution for this type of processing as the low shear, gentle handling properties of a Hidrostal pump ensure that no damage will occur.
The pumps combine the benefits of extended periods between maintenance, improved reliability and a compact cost-effective construction
All Hidrostal pumps contain the Hidrostal Screw Centrifugal Impeller, a unique design whereby the single spiral vane impeller is axially extended into the suction of the pump creating a large free passage for solids, but at the same time maintaining an optimum hydraulic design leading to high efficiencies, low shear pumping and low velocity at the pump inlet.
Triple solution
Hidrostal supplied four of the versatile, purpose built bearing frame pumps to British Sugar for the Wissington site. The pumps have a 300mm suction and discharge combined with 150mm of free passage and are able to handle 450 l/s at best efficiency point to a pumped head of 22m. Regulable liners allow the impeller and liner clearance to be adjusted to maintain the pump’s efficiency and performance.
The pumps combine the benefits of extended periods between maintenance, improved reliability and a compact cost-effective construction and will contribute effectively to the 400,000 tonnes of quality sugar produced per annum at the Wissington factory.
The first Hidrostal pump was developed in the 1960s, to transfer fresh fish from a trawler without causing damage to the stocks. Since that time Hidrostal pumps have been used to pump all manners of produce and other pumped medium in a wide variety of applications across many proc