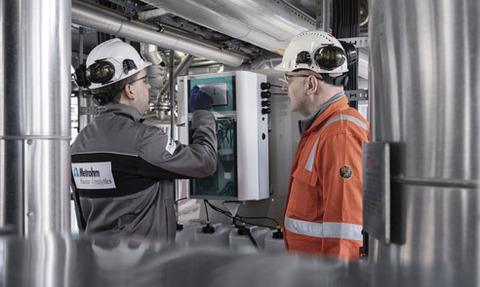
Propylene oxide (PO) is a major industrial chemical, necessary for the manufacture of several commercial and consumer products. The production of PO is possible via several routes, all with their own inherent risks.
Metrohm has published a white paper focusing on the improvement of various PO production methods through automated online and inline measurements of critical parameters directly at the process.
Polyurethane plastics, propylene glycol and many other goods are derived from the intermediate chemical propylene oxide. Production processes generally depend on the market value of by products such as styrene (from the SM-PO process). However, more environmentally-friendly routes have been gaining speed in the past decade.
The hydrogen peroxide to propylene oxide (HP-PO) process is one such method which only co-produces water with PO, but the risks involved are just as great as the other industrial processes. Both the precursors as well as the final products require significant care and attention to handle, purify and transport.
A safe and secure facility is one of the top requirements for PO manufacturers, and indeed at any industrial chemical plant. Automating chemical measurements performed directly at the sampling point is a superior choice over manual laboratory analyses.
Not only is data transferred to the control room in real time, allowing for optimisation of each part of the process, there is no need to put employees in harm’s way, creating a safer working environment for all. In a new white paper, several online application examples for monitoring critical quality parameters in the PO manufacturing process are provided, which are already utilised by top producers.
Metrohm Process Analytics is a leading manufacturer of customised solutions for the PO industry with a broad range of online, inline and atline process analysers engineered to run unattended 24/7.
For more information, click here.