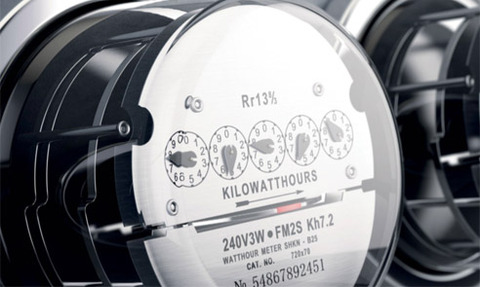
Regulatory rules tightening, a continued post-Brexit headache and now a pandemic to threaten export and sales. Fortunately, the sector is making the most of leveraging Industry 4.0 in some very specific areas.
In the power and utilities sector, worldwide lockdown is providing new impetus for greater automation and the reduction in human involvement in the process of making and operating pumps systems for the energy and utilities market.
The potential gains are considerable. Automation and digitalisation reduces the number of people directly interacting with systems, reducing issues around social distancing in peak epidemic periods. It also lessens the impact of substantial staff absences.
And, says Mark Ingham, sales engineer at Sensor Technology, it enables pump systems to supply real time operating data to control networks so that their performance can be monitored and adjusted for today’s rapidly changing production requirements.
It follows that, if the amount of time spent on wiring and installation could be reduced, the factory could reduce its operating costs significantly
Mark Ingham, sales engineer, Sensor Technology
This brings challenges, he warns. Take the traditional means of attaching sensors to a pump’s rotating drive shaft.
“Hard wiring a sensor into a pump’s rotating drive shaft usually requires the use of a delicate slip ring, [an] alternative solution is to use a non-contact radio frequency detector. Such advances are not without difficulties; one such being the need to connect machines and equipment such as pumps... to the control computers.”
Whereas wiring up one machine is not a major undertaking, in a highly automated factory there will be hundreds or even thousands of them in use, so the task becomes considerable, he cautions.
“Even a moderately sized factory has to employ a significant number of electricians and engineers who spend their days wiring and rewiring equipment. It follows that, if the amount of time spent on wiring and installation could be reduced, the factory could reduce its operating costs significantly,” says Ingham.
Talking torque
Take the task of fitting torque sensors to rotating equipment, which requires the use of fiddly and fragile slip rings. Torque, he points out, is a key performance indicator: a gradual increase may suggest increasing flow to compensate for growing leakage, sudden increase may indicate a blockage downstream, while a sudden reduction may be due to an upstream blockage.
TorqSense is a wireless sensor that replaces the need for physical wiring and slip rings with radio wave communications. Fitting a TorqSense typically takes about one-fifth the time required for a conventional hard-wired transducer, assesses Ingham.
A shaft under rotary load will twist very slightly along its length, in proportion to the magnitude of the load. TorqSense measures this twist in real time and its electronics converts the reading into a torque value.
TorqSense transducers use two surface acoustic wave (SAW) devices, which are attached to the surface of the shaft. When torque is applied to the shaft the SAWs react to the applied strain and change their output. The SAW devices are interrogated wirelessly using a radio frequency couple, which passes the SAW data to and from the electronics inside the body of the transducer.
SAW-based torque sensors have been used in many energy related sectors as well as generators based on tidal or river flows and can be used with virtually all pump-based systems, from microdosing to flow control and coupled with giant pumps used for water management systems.
Ingham explains: “All you have to do is set up a TorqSense is glue the SAWs to the shaft, fire radio waves at them and monitor the waves that are reflected back. The SAWs are distorted in proportion to the twist in the shaft, which in turn is proportional to the level of torque. The frequency of the reflect waves is changed in proportion to the amount of distortion and electronics within the TorqSense analyses the returning wave and feed out torque values to a screen.”
As the TorqSense method does not require contact with the rotating shaft it offers complete freedom from the slip rings, brushes or other solutions found in traditional torque measurement systems. TorqSense devices also have a high immunity to magnetic forces, allowing their use in, for example, motors where other technologies are very susceptible to electronic interference.”
Sensor Technlogy’s new Bluetooth module plugs into the TorqSense’s existing 15 way ‘D’ digital lead connector. As well as collecting torque signals, the modules can provide power to the TorqSense transmitter/receiver and provides a USB output for PC.
Similarly, the automation of process valves is a long-established practice with significant benefits for energy saving but digitalisation is bringing new opportunities, says Dr. Eckhard Roos [pictured], head of industry segment management process automation at industrial automation specialists Festo. This includes the first cases in whichartificial intelligence (AI) is being used in process valve applications.
“Adopting principles from the smartphone, where the hardware and user software (motion apps) are separate, has led to a new concept in valve motion terminals. Essentially, the valve terminal is equipped with additional sensors: integrating the disciplines of mechanics, electronics and software,” he explains.
“Different pneumatic applications can be implemented on the standard hardware via apps: for example, for end position detection for on/off process valves, eliminating the need for traditional limit switches or sensor boxes for end position detection.”
The ability to download an app to solve a process valve issue reconciles the conflicts of standardisation and flexibility he adds.
Roos cites the reduction of compressed air consumption to improve energy efficiency. In the planning phase, every pneumatic actuator is designed with a higher torque than would be necessary for the actual working stroke. With the relevant app, it is possible to pare down compressed air consumption and reduce the pressure in the actuator to the minimum required for the application.
“Experience with the Festo VTEM Motion Terminal has shown that energy savings of up to 50% are possible. A further advantage is that no intervention in higher-level controllers is required and no additional communication is generated on the bus systems, since the app and its functions are decentralised.”
Adopting principles from the smartphone, where the hardware and user software (motion apps) are separate, has led to a new concept in valve motion terminals
Eckhard Roos, head of industry segment management process automation, Festo
With the relevant app, working stroke duration can initially be set digitally. The valve terminal is then initialised independently and changes the pressure build-up in the actuator so that the required time is achieved, while travel time is continuously monitored. As the switching times change during the course of the product lifecycle the system automatically adapts the values to maintain the specified duration.
“An advantage of digitalisation in actuator technology is the possibility of realising machine learning algorithms on edge rather than centrally. Decentralised monitoring of actuator characteristics enables the parameters of the actuator itself to be analysed and allows anomalies in the technical process to be detected without additional programming,” adds Roos.
“This forms the basis for implementing predictive maintenance concepts, and the data analyses can also be used to determine the potential for optimising the production process. It is therefore clear that the adoption of digitalisation and AI concepts in process valve applications have many benefits.”