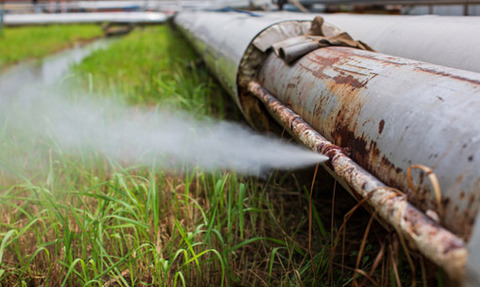
For pipes and connector equipment one of the biggest issues is corrosion, not least when it occurs out of sight. Fortunately, says Michelle Knott, there are plenty of cost and time saving tools now available.
The creeping problem of corrosion under insulation (CUI) is an issue for all process industries, but it is oil and gas operators that feel the impact most acutely. Long, inaccessible pipelines coupled with a potential for serious consequences when a pipe springs a leak mean that CUI is a major headache in oil and gas.
The Oil & Gas Technology Centre says that, out of the 137 major oil and gas accidents reported within the EU since 1984, over 20% have been associated with CUI. What’s more, current estimates are that CUI incurs between 40 and 60% of the process plant maintenance costs within the UK Continental Shelf and the value impact to the industry for better inspection techniques could be in the region of £130 million per year.
The stakes may not be quite as high in other process sectors, but CUI can strike anywhere. “There are obviously quite different risks for a high-pressure gas pipeline compared with a water or sewage pipe, even though the challenge is the same,” says Frode Wiggen, senior principal engineer in charge of CUI at risk management specialist DNV GL. “That’s the same across industries including chemical, process, pharmaceuticals and food and beverage, as well as oil and gas.
”CUI can take the form of localised external corrosion in carbon and low-alloy steels, or external stress corrosion cracking or pitting in austenitic and duplex stainless steel. Operators currently use a variety of methods to identify the presence of CUI. Until recently, there has been surprisingly little guidance about what constitutes best practice but DNV GL is looking to change that.
DNV GL has recently developed a systematic, risk-based approach to help companies apply best practice. Its structured approach to CUI, developed in collaboration with several regulatory bodies, international oil and gas operators and major players in the supply chain, is set out in a new Recommended Practice titled DNVGL-RP-G109.
The new standard helps to quantify the risk posed by CUI by systematically assessing the factors that contribute to the overall probability of failure. It combines this with the possible consequences to come up with an overall risk. The guidance then considers how that risk can be mitigated, either by increasing knowledge or by making modifications.
In a complementary move, DNV GL has also launched a digital visualisation tool to help manage CUI. This should make it easier to identify at a glance when and where maintenance efforts should be directed to mitigate the risk of a CUI-related failure. The risk assessment model that the CUI Manager uses to make its assessment is based on the same measures set out in DNV GL’s new guidance.
“At the moment the tool is available as a standalone, Cloud-based solution based on the Microsoft Azure platform,” says Wiggen. “We’re currently working with SAP to integrate the CUI Manager with their Cloud-based Asset Strategy and Performance Management solution to provide users with seamless and efficient access to the advanced calculators and processes in the tool. We will have a minimum viable product ready by summer 2020 and would like to meet with key customers to demonstrate the benefits of the integrated solution.
”The new tool uses traffic light visuals that make it easy for users to understand the risk currently posed to their pipelines and other assets by CUI. According to estimations the tool can reduce the cost of CUI-related maintenance by up to 50%.
Other organisations have been busy developing improved detection technologies for CUI… Investigators at the University of Lancaster have been reporting success with a technique inspired by bats
But Wiggen says that what really makes it unique from a user perspective is its ability to model ‘what if...’ scenarios: “CUI Manager has the ability to say ‘if you do this today you will need to address this object in ten years, but if you do something else you will need to address it in one year’. Costs are embedded in the tool so it can tell you the effect if you spend €10k this year, compared with spending €3k this year, €3k next year and €3k the year after that.”
Elsewhere, other organisations have been busy developing improved detection technologies for CUI.
For example, investigators at the University of Lancaster have been reporting success with a technique inspired by bats. Whereas bats use the backscatter from ultrasound at different wavelengths to map objects in their surroundings, the new technique uses a combination of two types of radiation – fast neutrons and gamma rays – to ‘see’ through insulating materials such as concrete of polyethylene to the metal pipe wall underneath.
The new system has been developed by engineers from Lancaster University, the National Physical Laboratory (NPL) and a spin-off tech company, Hybrid Instruments. “It’s certainly not in the field yet but it’s much more than a theoretical model,” says Professor Malcolm Joyce, a nuclear engineer at Lancaster. “The measurements were done with a prototype at NPL.”
The idea is to map the boundaries between different structures by recording how radiation bounces back to detectors as it meets materials of varying density. The investigators used californium as their radiation source. A system based on this approach should enable users to spot where sections of pipe wall are pitted or thinning as a result of CUI, without the need to remove any insulation.
Operators currently use a variety of methods to identify the presence of CUI. Until recently, there has been surprisingly little guidance about what constitutes best practice but DNV GL is looking to change that
Frode Wiggen, senior principal engineer in charge of CUI, DNV GL
Neutrons interact mainly with low-density materials like plastics, and fast neutrons have a high penetrating power, so they are suitable for probing thick materials. Gamma rays interact mainly with metals and are not always able to penetrate very thick materials of high density. The two radiation types each produce a different electronic signal, which researchers can monitor using a novel instrument called a ‘Mixed Field Analyser’, which was previously developed by Lancaster University and Hybrid Instruments.
The radiation might struggle to penetrate the full width of a large pipeline. However, that is not an issue with the backscatter technique, because the signal only needs to reach the inner wall of the pipe. Joyce explains that the detector is designed to pick up the backscatter and not the original signal. This is analogous to the way that bats ‘clench’ their ears so they are not confused by their own chirps.
Tests so far have taken place using samples of insulating materials and carbon steel in different thicknesses. The next stage will be further lab tests using sections of insulated pipe. The investigators say that more research is needed to speed up the neutron detection process before a commercial system can be launched.
In another project, start-up company CorrosionRADAR is planning field trials of a remote sensing technology that can screen the onset of CUI and pinpoint the most vulnerable sections of a pipe or other structure. The key innovation is a long, thin, flexible sensor.
The CorrosionRADAR sensor acts in a similar way to a conventional corrosion coupon but without removing and weighing. Instead it sends coded electromagnetic signals through the sensor permanently installed under the insulation alongside a pipe. Signals are interpreted using proprietary algorithms and various configurations can be installed.