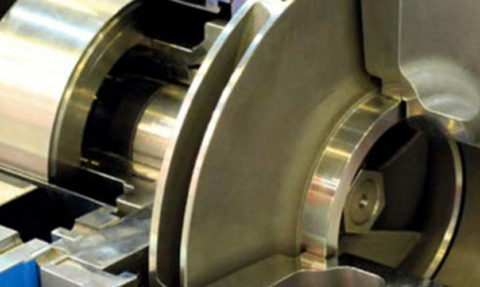
The post-Covid industrial landscape will increase the need for incremental gains in the chemicals sector. There’s no shortage of products and systems trying to make a difference.
The facts speak for themselves: the UK chemicals industry accounts for nearly 10% of our exports, EU trade accounts for nearly 60% of chemical exports and almost three quarters of chemical imports.
Brexit alone would constitute a headache. Then factor in the unforeseen impact of the Coronavirus pandemic. The message: every penny spent needs to reap added benefits and, if pumping systems comprise a significant part of costs, they can significantly drive value or undermine it.
Within the chemicals sector, the key areas in which pumping processes, systems and products can contribute to driving competitiveness are those relating to safety, efficiency, analysis and precision.
The ability of pump suppliers and technical experts to collect, analyse and act upon data collection from pumps will be crucial to improving the performance and optimisation of pumping systems
Lesley Eaton, SEEPEX
Lesley Eaton of Seepex stresses that choosing the correct pump is vital to ensure that product transfer occurs efficiently and safely without changing the characteristics of the pumped media. Allied to this, the need to embrace 4.0 approaches will only grow, she advises.
“Remote monitoring , data holding and interpretation by experts and control and optimisation are all part of Industry 4.0. The need for these will increase as a result of remote working and fewer site visits,” she explains.
“The ability of pump suppliers and technical experts to collect, analyse and act upon data collection from pumps will be crucial to improving the performance and optimisation of pumping systems.” One area in particular to watch is the liquid ring vacuum market. Its recent and project worldwide growth has been fuelled significantly by the chemicals industry, says analyst Persistence Market Research.
With a global value that already topped $2 billion in 2018, demand had been predicted to expand at an estimated 5% compound annual growth rate.
Growing demand for liquid ring vacuum pumps from chemical and general process industries plus investments from down- stream oil and gas is expected to drive increases, says the company.
Multifunctionaility doubtless plays a part in this and ought to insulate the market from longterm effects of the pandemic: in addition to the standard pumping and vacuum applications, liquid ring vacuum pumps can also function as gas compressors.
While adaptability is a key component for modern chemicals pumping systems, so too is the issue of saving on waste and unnecessary expense – especially anything that engenders downtime.
Plugging the leak
Michael Smith Engineers’ focus on magnetically coupled centrifugal pumps reflects industry interest in tackling one of the great sources of waste – leakages.
“A key benefit of the magnetic coupling design is that it results in a sealless pump and because mechanical seal failure is sometimes regarded as the ‘Achilles heel’ of other types of pump, these potential problems are eliminated,” says a spokesperson.
“This minimises the potential for downtime and lost production along with no cross contamination of the pumped liquid, less wastage, no environmental hazards due to leaks and increased operator safety.”
Such factors are critical when the process involves corrosive, toxic, explosive or other hazardous liquids. MSE’s DICKOW KM series range of sealless, single-stage, volute casing pumps offer a maximum flow rate of 70m3/hr maximum differential heads to 65 metres and maximum operating temperature up to 200oC.
These handle liquids with viscosities between 0.1 cP and 200 cP and are available in materials including cast iron, cast steel and stainless steel. The vertical configuration option with the motor mounted on the top eliminates the need for a base plate so is ideal when space is limited. Single elements of the multipolar magnet coupling are manufactured from Cobalt-Samarium with unlimited lifetime durability while the magnets in the driven rotor are completely encapsulated and not in contact with the liquid.
We’d be the first to admit that the lockdown forced us to think differently. The more we looked into what we could offer, the more ideas we saw to support our global business
Thorkild Maagaard, export director, Landia
Sometimes the issue is less about explicit waste or downtime, more about process inefficiency; systems work but not at optimum levels. It may be that very specific and localised adaptations reap significant benefits overall.
GEMU addressed the challenge of deadlegs between valves when coping with the need for cleaning and sterilisation in the chemical production of ointment.
Ensuring components are mixed correctly and sterile is vital and achieved via a vacuum process system including two sequentially switched mixing tanks with speed-controlled agitators.
These mix the fully automated process media gently at constant pressure to emulsify them. In order to guarantee consistency, the mixture is withdrawn from the pre-mixer and fed into the final mixer via a sophisticated pipe system to prevent concentration gradients and guarantee constant high quality before transport to storage containers.
Stainless steel aseptic multi-port diaphragm valve blocks are selected for controlling the sterile media, feeding into a bypass pipe system for removal of the final product.
Cleaning and sterilisation of the production line is integrated into block valve functionality with Steam in Place valves machined into the blocks.
A third ingredient in contributing to a more competitive process approach is precision. Given the impetus to grow the sector’s export markets, it could form an important guarantee for the industry’s continued health.
Foreign clients too are keen to tap into the opportunity provided to grow their export potential, as Watson-Marlow Fluid Technology Group (WMFTG) discovered.
South Africa’s Acorn Group is benefiting from dosing accuracy and consistency for its sunscreen lotion provided by a Watson- Marlow 530 peristaltic pump at its Johannesburg production plant, where it is being used to transfer bulk sunscreen lotion.
While neither viscous or shear sensitive and with no extreme temperatures involved in production, there is a heavy requirement for precision. Using the pump with a 520R2 pumphead and silicone continuous tubing, it is capable of dosing with +/-1% accuracy.
Robert Verseput, responsible for expanding Acorn’s distribution network globally, explains: “Bulk sunscreen is drawn from a 100-litre stainless steel holding tank with constant head height, and transferred via the Watson-Marlow 530 pump into aerosol tins. The accuracy and consistency of dosing via the pump is thus critical. Thereafter, a valve is added and crimped, and propellant introduced via the gassing plant.”
The 530 pump offered flow rates up to 3.5 l/min at 2 bar pressure, four drive and five pumphead options, plus a range of tube sizes and materials. Running for approximately seven hours a day, it transfers around 400 litres of sunscreen.
States Verseput: “They are accurate, easy to clean and versatile over a variety of applications and product viscosities. In addition, this pump type allows for a reverse cycle at the end of the fill cycle, minimising post-fill drip.”
Underpinning all innovation and development within the chemical pumps sector is, as elsewhere, the growth of digitalisation and 4.0 models. For example, GEMU’s valve system referenced above is enhanced by the addition of fully automatic control and monitoring, using fieldbus-supported switchboxes.
Watson-Marlow meanwhile announced in March that all Qdos Universal and Relay chemical metering pumps will henceforth feature four changeover relay outputs, with either 110VAC 4A or 24VDC 4A contact rating – to help users cut down on the need for additional PLCs and provide extra flexibility when communicating with SCADA or other external monitoring systems.
These outputs with software modified to allow for easy configuration will sit alongside the current 4-20mA, providing a total of five outputs and giving improved communication regarding pump perform- ance and function status.
And there’s a further factor now underpinning change. Global lockdown has forced companies to embrace online and question why they failed to realise the logistical and financial gains. One such is Landia which claims 90% reductions in the cost of recent commissions in Hong Kong.
“Online commissioning might not become the new normal,” said Landia’s export director Thorkild Maagaard, “but our new eServices are here to stay.”
Previously the firm had to send an engineer to China to go through the installations and carry out a pre-start up check dry test, a pre-start up check wet test and education of service staff on site before receiving a commissioning approval certificate.
“If we’d had to send over one of our engineers from Denmark, the cost would have been in excess of $5,000. Online commissioning is a fraction of the cost,” explains Maagaard, adding typical time- consuming delays such as the contractor having to wait for a supervisor meant commissioning could take up to 10 days.
Online commissioning would take a day, with the added benefits of:
- Pre-installation meeting with the Landia Project Manager
- Supervision on demand. Minimum of one online meeting per day
- Supervised guidance during the installation
- On-line dry and wet tests
- Approved commissioning/written acceptance from Landia
Adds Maagaard: “We’d be the first to admit that the lockdown forced us to think differently. The more we looked into what we could offer, the more ideas we saw to support our global business – ideas that at the same time, mean less air travel and a much- reduced global footprint for us, our customers and the planet.”
During the recent two week lockdown on the island of Jersey, when no planes or ships were permitted, Landia was able to provide online commissioning for maintenance of its digester mixing systems. As was the case with Landia’s online commissioning for Hong Kong, costs were reduced for both parties by 90%.