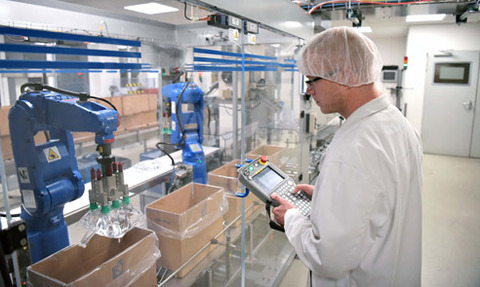
Investing in better equipment and learning from other sectors boosts predictive maintenance but there’s more chance of adoption when it’s aligned with commercial objectives.
Offshore oil and gas may seem far removed from the world of the modern factory-based process world but it’s the harshness of that environment and its interconnection with downstream that makes it worth observing.
The pressures it faces are a combination of the ongoing and the game changing. In a UK context, more demand for a diminished and dispersed supply, coupled with a global move away from fossil fuels and exacerbated by lockdown’s limitations on the human labour force.
As Diethard Fent, manager sales partner EMEA at global computer tech company congatec observes, the International Energy Agency estimates that digitisation can reduce production costs in the oil and gas sector by up to 20%.
According to auditing and consulting firm PWC, he points out, there is great potential for savings through more efficient maintenance and better operation of assets.
“Both the upstream and midstream oil and gas sectors, for example, are characterised by distributed assets and infrastructures in harsh environments. They therefore require ultra-robust embedded platforms for the digital transformation challenge that offers a huge potential for cost savings,” he explains.
“There is also further potential for savings in the supply chain, through the use of artificial intelligence and integrated platforms that connect organisations with external partners.”
Tough testing
Unsurprisingly the nature of all offshore operations lends itself well to the potential benefits of embedded computing and digitisation, says Martin Frederiksen, managing director of Recab UK.
Even the fast growing offshore wind industry, traditionally a laggard in this area, is investing in edge servers for remote monitoring and predictive maintenance, he points out.
Harsh circumstances such as sea water, weather conditions and reductions in staff and internal competencies have underlined the benefits of digitisation in terms of reduced production costs, improved maintenance efficiency and lower capital expenditure. And it helps to emphasise the central role of effective prediction in sectors where there might otherwise be more room for delay.
There is also further potential for savings in the supply chain, through the use of artificial intelligence and integrated platforms that connect organisations with external partners
Diethard Fent, manager sales partner EMEA, congatec
Elemica is an established force in the chemical industry with its digital supply chain networks. Now, it is branching out into the related pharmaceuticals sector – a logical step, explains chief technology officer Arun Samuga.
“Chemicals are a prime input to the pharmaceutical industry. In addition, these industries share synergies in supply chain challenges. This makes Elemica’s solutions a natural extension for pharmaceutical manufacturers,” he states.
With an estimated 90% of the leading pharma companies connected already to its network thanks to the electronic purchase orders they send to Elemica clients, connection is not difficult.
The firm’s Digital Supply Network solution captures real-time event and transaction data from formulation and raw material suppliers to customers. Partners can react to supply and demand changes, while digitised orders, advance shipping notices and invoice documents reduce supply chain risks. Plus, the allimportant just-in-time delivery is improved through insights regarding timeliness of deliveries, distribution costs, sales and customer satisfaction.
But while the benefits of better predictive maintenance are there for all to see, the perspective is perhaps very different for the potential purchaser who prioritises keeping his or her process operation afloat as a going concern over pushing the boundaries of innovation.
It’s a standpoint that Rashesh Mody [pictured], vice president of AVEVA’s monitoring and control business, is aware must be foremost in the minds of suppliers. His company’s newly launched Aveva Insight OMI seeks to embed real-time artificial intelligence into an operator’s decision making and boost operational agility.
Its predictive early warning and automatic detection of unusual operational behaviour provides early notification before issues become critical business risks. But he is wise to the fact that IIoT and data collection have caused challenges as well as solutions.
“Operators face alarm overload and often cannot effectively react to or distinguish between process-critical situations and false positive alarm conditions, resulting in the loss of operational time and resources,” says Mody. Technology needs to adapt to the needs of the business rather than vice versa. This is as much a matter of training artificial intelligence as the human version.
Tailored approaches
“A simple management interface enables operations, maintenance and production teams to quickly train the AI engine to adapt to the enterprise’s specific implementation. An intuitive thumbs-up or thumbs-down confirmation ensures AI-driven notifications are relevant to the needs of the user and support overall enterprise objectives, with no programming or data science knowledge required,” explains Mody.
“This closed-loop feedback improves the accuracy of the AI prediction engine over time and enables users to see what matters. As anomalous patterns are identified, they can be captured and presented by the app within an organisation’s on-premise HMI/SCADA solution, delivering insights directly where operators need it.”
Turning the issue on its head, Sulzer reminds us that the imperatives that ruled out better quality prediction no longer apply. Automation of measuring instruments was at one time prohibitively expensive, hence the abiding preference for manual measurement of less critical equipment.
Operators face alarm overload and often cannot effectively react to or distinguish between process-critical situations and false positive alarm conditions, resulting in the loss of operational time and resources
Rashesh Mody, vice president, monitoring and control business, AVEVA
The problem, cites Sulzer, is that manual approaches provide a snapshot that may not accurately represent activity over time and may put staff at unnecessary risk. Plus data capture is not only far more limited but what little exists may not be entered or analysed effectively.
This is not to suggest however that staff cannot be effective agents of improved predictive maintenance. Swagelok senior technical services engineer David Ross points out that the humble pressure gauge is one case where a little extra attention goes a long way.
“A pressure gauge not functioning accurately may lead to lower quality system output due to the loss of valid data and the resulting effects of too much or too little system pressure. A gauge that fails can also release system fluid into the environment, cause system damage and lead to lost output and profits,” advises Ross.
He pinpoints five factors to focus upon:
Overpressure – Select a gauge with a range rated to two times the expected system operating pressure to provide a larger window of measurable pressure or include overpressure protection (i.e. a relief valve) in the system preceding the gauge
Pressure spikes – Evaluate your system design to eliminate unpredictable pressure spikes and their resulting strain on system components. Alternatively, select a gauge with a larger pressure range
Mechanical vibration – Using a liquid case fill will dampen the movement and can eliminate or reduce the avoidable system vibration Pulsation – Redesign your system to reposition the gauge to reduce the cycling speed it sees and maintain its measurement integrity. If that is not possible, use a gauge with liquid fill, a gauge orifice restrictor, or a snubber
Excess temperature/overheating – Select a gauge with a different temperature rating that accommodates the system
Adds Ross: “Recognising the indicators of pending gauge failure and the causes will help you recognise that the pressure readings are no longer accurate, helping you avoid these undesirable outcomes.”