Getting your eggs in one basket the fast and accurate way
2 Dec 2020
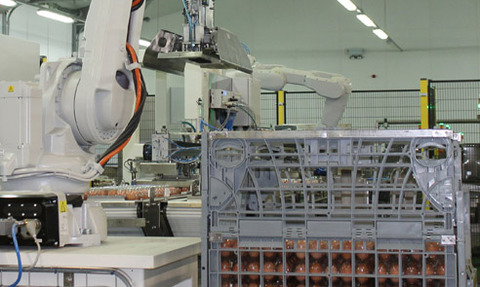
Robot palletising technology is transforming industry and as CKF shows, it can even cope with the delicate job of packing eggs fast.
Supplying goods to UK supermarkets is a demanding and highly competitive arena with the focus on producing faster and better.
When it comes to something as delicate as a chicken egg, greater speed can impact the number of breakages that occur with a knock back effect on costs.
One long-standing and major supplier of eggs to many of the UK’s leading supermarkets needed to reduce the number of its eggs that were damaged, increase throughput and reduce the amount of manual handling involved, reducing costs and increasing safety.
The firm turned to CKF which was commissioned to automate their packing at one of the client’s two sites.
CKF designed and manufactured a cutting-edge egg packing and palletising systems that aimed to dramatically improving their customer’s operations.
“We encountered a number of issues through the planning and implementation of this project due to the variety in pack materials,” explains Chris Young, project engineer, CKF Systems.
If the lid is not closed or the date is incorrect or missing, the product is rejected and sent to the reject conveyor for removal
Their existing out-feed egg packing system fills cartons of various sizes and materials and closes their lids. It previously fed the eggs to a manual packing station.
The new system, installed into the existing system, was made to feed the filled and closed cartons onto the out-feed conveyor. The set-up is determined by their current production requirements.
This solution includes a vision system which verifies that the use-by date has been included and that the lid is closed. If the lid is not closed or the date is incorrect or missing, the product is rejected and sent to the reject conveyor for removal.
Automating this process means faulty product is removed swiftly from the line, preventing it reaching the customer and ensuring the quality of the end product. If the product passes the test then the egg carton is transferred onto the collation infeed conveyor unit which transfers and orientates the product correctly, ready to be conveyed to the box splitter unit.
Where two packs of six-egg cartons are joined and need to be split, the box splitter unit is used to split the cartons using a blade without damaging the eggs. The box splitter can cut both pulp and plastic. The solution has a product spacing unit which uses pneumatic stop gates to ensure there is a set amount of space between the cartons of eggs or group of egg cartons to allow for pack orientation or for repositioning into the correct lane.
Palletising the egg cartons
A low back pressure chain roller conveyor moves the egg cartons through to the robot sorting collation conveyor. The sorting modular belt conveyor encoder is used to track the cartons’ positions, enabling the sorting robot to reposition the packs thus creating the required collation.
The system utilises an ABB IRB1200 sorting robot system to arrange cartons into specific patterns on the sorting modular belt conveyors. The type of carton and the type of container determine the collation pattern, says Young: “Being able to handle different materials was absolutely vital.”