Cracking contaminants to ensure optimal performance
16 Dec 2020
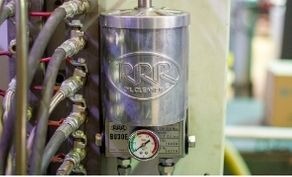
A Scots manufacturer’s determination to crack down on pumps and valves failure netted a return of £0.2 million with the help of Tris UK.
Market leader in the production of aluminium and non-refillable closures, Guala Closures was keen to eliminate unnecessary waste of energy, equipment and production at its Glasgow site.
But, says maintenance team leader Craig McCall, the manufacturing site had a historic and significant issue with injection moulding machines breaking down.
“Pumps were having to be replaced three or four times a year on the machines, valves were jamming at around the same rate, and each time a part was replaced, the machine oil had to be changed as well,” he said.
“The machine would be down for 24-36 hours while remedial works were taking place. As anyone in the industry will know, pumps cost around £5k each, and valves £2k, so the cost of replacing those alone was extremely high.
“With 25 hydraulic injection moulding machines, and 400 litres of oil each time, it was adding up to a tremendously wasteful and costly problem. We didn’t know what was causing it, so put it down to inevitable wear and tear on the components.”
MD of Triple R Industrial Services UK (Tris UK) Andrew Thoms had previously worked in the plastics industry. He knew that many plastics manufacturers operated with oil contaminated with solid particles, varnish and water in their machines – the major cause of breakdowns – and offered the company a free trial of Tris UK’s Triple R bypass oil filter.
“It made total sense that it was the oil that could be causing the pump and valve failures, so we gave it a try,” explains McCall.
We’ve literally had no pump or valve replacements in 10 years. They’ve saved us over £200,000 over the past 10 years, countless production hours, and prevented remedial works
Thoms’ laboratory tests of oil in the injection moulding machine revealed it was ISO Code 23/21/17 (or NAS 12) – extremely dirty oil for the application. Tris UK installed the Triple R System (which required less than 30 minutes of machine downtime). After three months, the oil cleanliness had improved to ISO Code 16/14/10 (or NAS 5).
“Normally during that time, a valve or pump would have gone on the machine. The oil went from thick, black, nasty stuff to clear, light brown liquid,” says McCall.
Guala Closures subsequently installed Triple R filters on all of its 25 hydraulic injection moulding machines.
The filters remove all three forms of contaminants; solid particles, resins and water, thanks to a design which forces oil through a 114mm thick filter mass, comprising three different layers that remove 99% of solid dirt particles (filters down below two microns), eliminate the development of oxidation and resins and reduce the concentration of free water to below 100ppm.
“We’ve literally had no pump or valve replacements in 10 years. They’ve saved us over £200,000 over the past 10 years, countless production hours, and prevented remedial works,” he concluded.