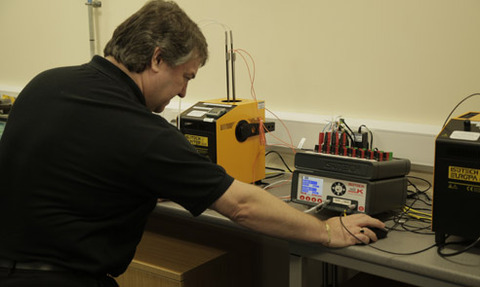
Evolving demands on industry require a more holistic approach to support a greater emphasis on traceability in flow measurement and control, coupled with regular inventory checks.
Measurement technology has been a feature of human life since the earliest eras of civilisation.
Its longevity and permanence in our world may indicate a rootedness in the distant past but its enduring role is also proof of its continuous evolution to adhere
to altered circumstances and new possibilities that build on innovation.
As economic activity becomes increasingly global in scale, effective measurement functions as an essential currency underpinning trade and manufacturing.
Martin Hanton is technical director at TÜV SÜD National Engineering Laboratory, world renowned for technical consultancy, research, testing and program management services, as well as a global centre of excellence for flow measurement and fluid flow systems.
Metrology underpins trade and market confidence; if you can’t quantify something, then you can’t sell or trade it. This control of quality, standards, agreements and ultimately wealth is what gives a national measurement system importance
Martin Hanton, technical director, TÜV SÜD National Engineering Laboratory
As the UK’s Designated Institute for Flow and Density Measure-ment, the organisation appreciates the value of its work impacts far beyond the laboratory alone.
Explains Hanton: “Metrology underpins trade and market confidence; if you can’t quantify something, then you can’t sell or trade it. This control of quality, standards, agreements and ultimately wealth is what gives a national measurement system importance.”
The UK’s National Measurement System’s effectiveness derives from its network of laboratories and processes that provide measurement standards, calibration and testing facilities, he outlines. Delivered through the Government’s Department
for Business, Energy & Industrial Strategy, the annual investment supports a range of industries worth billions to the economy.
However, the system also relies upon work done on the ground, within the workplace, reminds Dr Jonathan Farrington, technical manager – service at ABB Measurement & Analytics. Attending to this aspect not only boosts the trustworthiness of the system as a whole but is also an essential for ensuring the maintenance of good business and manufacturing practice.
“It is easy to take the efficiency of your installed instrumentation for granted. Yet the reality is that not only could you be losing potential revenue through lost production, but an impaired measurement could affect your ability to comply with environ-mental and safety legislation, exposing the organisation to legal action and financial penalties,” explains Farrington.
While many companies including ABB offer specialist consultancy services, Farrington recommends a number of steps firms can take to ensure maximum efficiency via effective maintenance and monitoring.
He offers a five-point checklist to help assess whether an instrument may be in need of a health check. Firstly, correct instrument calibration. This is vital for accurate and repeatable measurement performance, he advises.
“Standards such as section 7.6 of ISO 9001:2015 oblige companies to maintain and calibrate their measurement instruments on a regular basis. Additional requirements
include the need for instruments to be clearly labelled with information including calibration status, the date when the next calibration is needed, and the need for protection against accidental damage and deliberate interference.”
Furthermore, says Farrington, instruments must also have been calibrated by a qualified testing and calibration laboratory. ISO/IEC 17025 stipulates key management and technical requirements for ensuring that laboratories are operating the correct quality management systems and that any tests and calibrations are performed to the correct accuracy and reliability.
While the advent of Industry 4.0 has meant an increased rate and volume of data provision, it is necessary for users to question whether their instruments provide them with the data they actually need.
Developments in communications offer new possibilities for gaining quick and easy access to an expanded range of instrument data including maintenance requirements, says Farrington.
Problems with instrumentation may also be due to the characteristics of the installation environment. High vibration, extreme ambient temperatures and continuous exposure to the weather, can all impact on instrument performance
Jonathan Farrington, technical manager – service, ABB Measurement & Analytics
Smart instrument can pinpoint potential issues before they develop, by assessing every aspect of an instrument’s performance. And, of course, such technology can help enable deployment of engineering resources.
Less obvious perhaps is to consider whether one’s measurement devices might be creating problems elsewhere in the process.
“Frequent or unexplained plant breakdowns can often be symptomatic of a measurement problem. Although an instrument may appear to be in good working order, it may actually be generating spurious information that can impact on equipment or processes further down the line,” adds Farrington.
“Problems with instrumentation may also be due to the characteristics of the installation environment. High vibration, extreme ambient temperatures and continuous exposure to the weather, can all impact on instrument performance.”
Reading the situation
Subtler problems may arise too with equipment which appears to have functioned well but may be less accurate than assumed. Accuracy can be determined by comparing the measuring instrument against a device with a known accuracy, advises Farrington. This may be a device specifically for verification, or an identical ‘mirror’ device that can be set up to temporarily measure the same process, with the readings being compared.
Ultimately this process reinforces the importance of credible national and international standards, as Hanton outlines.
“Measurement traceability plays a vital role in national infrastructure and is the technical proof that a measurement device has the appropriate pedigree, normally through calibration records, back to a national standard,” he states.
“Reference standards and materials are used to calibrate devices, but these references must themselves be verified, through a chain that eventually leads back to a Physical National Standard, as the ultimate ‘authority’.”
Where flow measurement specifically is concerned, this is essential to the viable operation of systems across numerous sectors, points out Hanton, ranging from the infusion of medication at very low flow rates to operation of industrial processes and oil fields at the opposite end of the scale.
Historically, flow measurement has been crucial to industries such as the water sector and oil and gas, and it remains so, but the demands of industry are evolving, indicates Hanton [pictured].
This involves movement away from fixed interval, physical calibrations towards continuous performance tracking using condition-based monitoring, reducing costs and improving confidence in real time.
“In part this is enabled by digitisation and in part by application of data science and artificial intelligence, with these techniques now providing new insights across a diverse range of applications from water networks to gas distribution networks, industrial processes, and intercontinental pipelines. Such measurements
and techniques now allow immediate decisions on flow control, system status and distribution.”
Today, the decarbonisation agenda ensures that flow measurement will be a critical technology to the use of hydrogen and carbon capture, utilisation and storage.
In effect, predicts Hanton, flowmeters will be the ‘cash registers’ that determine how much of these materials is sold and traded.
For flow metrology to operate as a global currency, other nations’ own National Measurement Institutes and Designated Institutes will be no less important, feeding into international bodies such as BIPM, EURAMET, CIPM, ISO etc that ensure cooperation via Mutual Recognition Agreements.
Drill down to the level of the individual plant and factory and you arrive at the final item on Farrington’s checklist: are you complying with the latest legislation and standards?
So, he says, consider whether instrumentation is fit for purpose and certified for use in the application; is the best available technique; and its verification and maintenance is documented.
Concludes Hanton: “Recent developments in flow metrology... highlight that metrology remains as important, if not more important than ever, in this age of Big Data and associated decisions. If algorithms are not fed accurate data, they will not make accurate decisions.”