The safety challenges for rubber and plastic recycling processes
30 Sep 2021
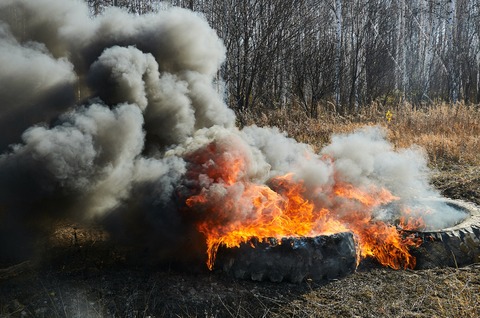
As rubber and plastic waste continues to grow, The UK is actively seeking alternative uses for these materials. Yet recycling brings significant fire risks in storage and intense processing, warns Fire Shield Systems’ James Mountain...
Modern plastics and rubber comprise a complex mix of materials, many of which are combustible. These materials are also oil-based, meaning they will often behave much like a flammable liquid once ignited, making suppression extremely challenging.
Rubber burns at extremely high temperatures, with rapid smoke and fire spread. When alight, rubber will often melt, giving off flammable vapours that can become trapped in the hot mass. This can cause fire with explosive force if not controlled quickly.
The most common type of rubber fire is a tyre fire, because waste tyres are regularly stored in stockpiles for long periods of time before being recycled. These piles have a potential for high heat output. When recycled, tyres are shredded into smaller chips, which can be highly susceptible to self-combustion if not monitored closely.
As rubber naturally repels water, and rubber tyres often release large quantities of oil when ignited, water alone will often not be an effective suppression solution.
Drastic plastic
Like rubber, plastic fires can spread rapidly, and when alight, plastic will melt and run, causing fires to often spread in unpredictable ways.
Plastics are commonly used in the production of alternative fuel sources, such as solid recovered fuel (SRF) and refuse derived fuel (RDF). This process carries a number of fire risks. Subcoal technology is now also being used to upgrade these fuels into pellets to power lime kilns, for example. These pellets are extremely susceptible to ignition due to their high calorific value.
Waste tyres are regularly stored in stockpiles for long periods of time before being recycled. These piles have a potential for high heat output. When recycled, tyres are shredded into smaller chips, which can be highly susceptible to self-combustion if not monitored closely
So here are some tips for mitigating these risks:
Bulk storage of raw materials
- Regularly review the materials’ sub-surface temperatures
- Control moisture levels
- Ensure sufficient ventilation
- Reduce pile sizes where possible
- Separate stockpiles (either physically or with fire walls)
- Monitor stock to avoid extended storage times.
As plastics and rubber are water-repellent, compressed air foam systems will often be more effective than water in suppressing fires in these materials.
Processing
- Conduct regular maintenance on machinery to prevent friction and mechanical failure.
- Clean machinery and equipment to prevent the buildup of combustible particles released during shredding.
Individual elements of the processing machinery may need localised application protection. Detection systems, such as video flame detection or infra-red flame detection, can also help to identify flames or sparks.
Storage of recycled materials
- Turn high-risk stockpiles at regular intervals
- Monitor below-surface temperatures
- Control moisture levels
- Review material risks, eg exposed metal content.
As SRF and RDF have high calorific values, water alone is not an effective suppression agent. Often, Class A penetrating foam systems, using deluge, cannon or hose reel systems are more effective.
Your fire prevention system should be informed by a full fire risk assessment, ensuring it is tailored to your individual site and its risks.
James Mountain is sales and marketing director, Fire Shield Systems
Photo: tengyart@unsplash