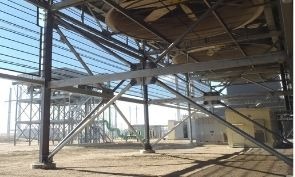
While it may be a traditional aspect of every process industry sector, heating and cooling is moving in step with the demands of sustainability, digitalisation and lifetime investment.
“I don’t think COP26 has had any direct influence on the market. Legislation and price are the big drivers of change, so something like the recent huge spike in natural gas prices will have directly impacted energy consumers’ decisions with regard to their energy and equipment suppliers.”
So said Bernard Dawson, technical director at heating experts Riello Ltd, around the conclusion of the world’s great environmental conference this year.
It’s a salutary reminder that those who do the making may have more immediate commercial and regulatory concerns. Dawson does, however, acknowledge that the influence of the Glasgow event may be seen in a few years, if effective international legislation and initiatives result.
And he is unequivocal about how technological challenges and changes in manufacturing are impacting the heating and cooling sector. Not least digitalisation.
“We expect to see wider use of digitally controlled burners, replacing traditional electro-mechanical burners. This is because of the major improvements that digitally controlled burners deliver in terms of efficiency and performance,” he states.
From Riello’s perspective, he adds, it is apparent that traditional electro-mechanical burners, for example, are now often replaced by the digitally controlled variety.
This shouldn’t obscure the reality that the former has still by far the larger market share/ uptake, points out Dawson, but the direction of travel is obvious.
“As electronics become relatively lower in cost and the mechanical systems relatively more expensive, digitally controlled equipment will eventually become the norm,” he predicts.
As with heating systems and products, so it is too for their cooling counterparts. Rittal product manager for climate control Karl Lycett says the need for seamless communication between cooling units and associated Cloud-based systems is opening up opportunities for new applications via IoT-capable devices.
This is an especially welcome advance, given that for example, the costs incurred for energy, maintenance and service during the lifetime of an enclosure cooling unit are usually much higher than the initial investment in the unit itself, points out Lycett.
Optimisations carried out during maintenance can help reduce workload and thus lower costs, for example through predictive or needs-based maintenance, he says.
If there is historic information available to plant operators about a cooling fan’s running time, the difference between its expected and actual speeds, and its power consumption, then it is possible to identify a gradually developing fault or an impending failure.
Thus vital components can be replaced early on, increasing the overall system’s availability, emphasises Lycett.
“As electronics become relatively lower in cost and the mechanical systems relatively more expensive, digitally controlled equipment will eventually become the norm
Bernard Dawson, technical director, Riello Ltd
Of course, awareness of Industry 4.0-era enhancements to equipment is one thing, but affording it is quite another when a company has a host of legacy assets that it must maintain rather than afford to replace.
Even so, points out Riello’s Dawson, there is always capacity for improvement. “Better control of the energy utilised in a process is always a good starting point, thereby ensuring no energy is needlessly wasted due to poor control,” he states.
Information such as energy consumption, component condition and even the level of soiling on a filter mat can also provide useful data, and practical opportunities to optimise maintenance and energy efficiency, adds Lycett. But recent advances have taken things far beyond human physical limitations.
“The sight of maintenance technicians walking from one cooling unit to another, jotting down information with a clipboard and pen, is a thing of the past,” he adds.
Using the new IoT Interface, Rittal units can network with customers’ in-house monitoring and energy management systems so data is continuously evaluated. Plant operators can identify potential malfunctions early, improving reliability, says Lycett.
“Needs-based maintenance is cheaper than carrying out maintenance work at fixed intervals and raises system availability.
“Our solution also calculates the shortest routes between calls for service engineers, which eliminates wasted journeys at facilities with a large number of machines. Live data on each unit means staff can bring the right spare part with them straightaway.”
Diagnostic software allows more energy saving throughthe optimum operation of their cooling units with relevant information provided by the new RiDiag III data cockpit.
Its Energy Efficiency Ratio display tracks how the cooling unit performs under specific environmental conditions and with the benefit of specific settings. Analysing the data enables efficiency improvements and lower costs.
The influence of technology upon efficiency is all-pervading. DHD Cooling technical sales director Gary Dicker explains how Computerised Fluid Dynamics (CFD) has boosted the effectiveness of industrial fabrics as an alternative to cladding systems for larger and exposed structures – providing wind and ice protection yet permitting light.
“Winds can affect the reliability of air cooled condensers, leading to mechanical failures. CFD modelling can help to determine the right position, and porosity of fabric protection screens, and provide accurate predictions for expected improve- ment,” says Dicker.
“The sight of maintenance technicians walking from one cooling unit to another, jotting down information with a clipboard and pen, is a thing of the past
Karl Lycett, product manager for climate control, Rittal
Such improvements play well to industry’s twin concerns of efficiency and environmental responsibility. In the cooling market, HydroFluoroOlefin (HFO) refrigerants are making increasing impact as an alternative on account of their low GWP (global warming potential) values.
Temperature control solutions firm ICS Cool Energy recently installed a new system at a major UK dairy processing plant. This delivered 1.2MW of process cooling for two production areas employing three of the company’s Cool Energy Imperium chillers with R-1234ze refrigerant boasting a near-zero GWP.
ICS major account manager Ben Young said the client agreed to switch from its traditional, ammonia-based system.
“Many industries and businesses are favouring a HFO like the R1234ze over ammonia due to its non-toxic nature. The HFO also offers very low GWP value of less than one,” he said.
“By utilising the latest technology innovations, process cooling systems with HFO refrigerants can create a safer, more trouble free, energy efficient option with equally low environmental impact as ammonia.”
Pollution concerns are no less important in the heating sector. For Riello’s Dawson, the big issue is minimising emissions of pollutants in flue gases, something that has become a significant factor in burner design spurred by the need for environmental responsibility and the maintenance of a competitive edge.
Cool and calm
Meanwhile, in the cooling industry, one solution gaining increasing traction is the matter of tackling noise pollution.
Global cooling tower manufacturer SPX Cooling Technologies turned to the Cooling Technology Institute (CTI) for guidance. Company global product manager Scott Maurer explained it is difficult to verify whether a cooling tower was entirely compliant once installed because of the lack of a single, governing sound test criterion across the industry.
Regulatory bodies and purchasers variously use sound pressure or sound power levels as their measurement, he pointed out.
“Manufacturers intending to sell globally should incorporate sound reduction technology into tower design configurations. Cooling tower sound issues can be resolved by adopting a universally accepted standard that is regulated and administered by an independent third party,” he advised.