Optimising equipment to extract the best AD performance
1 Jun 2022
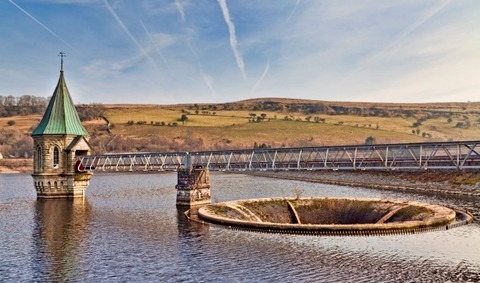
Anaerobic digestion plant performance depends on reliability and getting the most out of the feedstock. Improved efficiency can be achieved by optimising sludge handling equipment says Sulzer’s Gabriele Casella
Waste streams that feed into a treatment plant can vary enormously, depending on the surrounding industry. Agriculture, abattoirs, breweries, food waste all pose their own challenges in terms of particle size and fiber content, and for the anaerobic digesters, this mix of sludge content has a significant impact.
All sludge handling plants should use some form of macerator or chopper pump in the supply stream. They have two main purposes, to minimize any damage to equipment downstream and to increase the surface area of the solids, maximizing biological process efficiency while reducing the total time required in the digester
If the feedstock supply pump fails due to a blockage then the process starts to fail shortly afterwards. Bacteria responsible for breaking down the sludge and producing the methane will decrease, reducing productivity while fibres in the sludge can cause problems in the pipework and pumps as well as result in the clogging of heat exchangers.
Macerators and grinders can minimise these issues by reducing the length of the fibres and thereby solve the problem.
Review the options
Macerators typically have high energy consumption, whereas grinders use gearboxes and smaller motors, which have a much lower power requirement. Macerators are widely considered as being expensive in terms of running costs and maintenance.
A grinder can deliver significant savings and enable a digester to increase throughput allowing a treatment plant to handle increased sludge volumes without expanding the existing site.
Specification of the most suitable design can be achieved through support from an experienced manufacturer, such as Sulzer, to ensure optimum performance of the digester and equipment downstream. ATEX certification, IP68 rating for complete submersion can also be specified to meet application requirements.
By installing a grinder upstream of the digester, a sludge particle size of less than 10 mm
(in one direction) is expected, giving a greater surface area available for biological activity during digestion. This can lead to a double-digit increase of the methane production rate.
Sludge treatment plants that already have a macerator in place can take some of the load off this equipment by installing a grinder upstream. This can also enable a cutting screen with smaller diameter holes to be installed, reducing the average size of the solid particles even further.
Improved performance from the aerobic digester means greater gas production, which increases the energy generated. This double benefit means a considerable net saving for the treatment plant as well as efficient and effective handling of the sludge.
These improvements can be enhanced with modifications to the equipment upstream of the digester. AD plants require a storage/buffer tank for the feedstock that needs to be kept thoroughly mixed to ensure a homogenous supply to the digester. Mixers can be mounted on the sides or the floor of the buffer tank and the digester itself to keep the solids in suspension, optimising productivity and efficiency.
For any sludge handling process, reliability along with efficiency are crucial factors and both of these can be influenced by careful consideration of the existing installation.
Gabriele Casella is sales manager MEA for Sulzer Water BU