Vigilant monitors ensure continuous power
23 Nov 2022
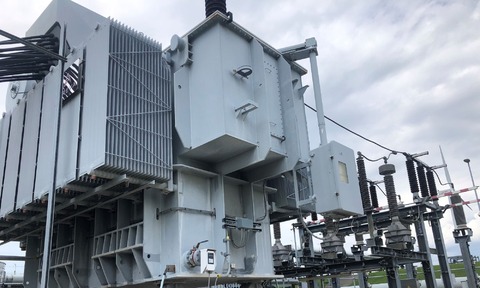
Deteriorating transformers can undermine power output. To prevent this, one biomass plant found a solution with continuous monitoring...
Owned and operated by energy company Eneco, the Bio Golden Raand plant in the north of the Netherlands produces steam for local industry as well as power, with a capacity of approximately 135 MW thermal and 49.9 MW electrical.
Transformers play a vital role in the transfer of electrical energy to power processes but transformer materials can deteriorate over time, resulting in the potential for costly faults, repairs and downtime. Such faults result in the accumulation of dissolved gases in the transformer oil, so this oil is routinely tested as part of a preventative maintenance program.
Eneco project manager and maintenance specialist Freriksen said the firm sought advice on a solution from service provider Flux Transformer Services. They recommended Vaisala online monitors “to support the planning and optimisation of preventive maintenance…extend the lifespan of our transformer, and reduce the risk of unexpected and costly outages.”
Vaisala’s MHT410 which monitors a single gas (hydrogen) was chosen to provide continuous data and reduce the requirement for periodic oil sampling and laboratory analysis. It continuously measures three key parameters in transformer oil: moisture, hydrogen and temperature
Explained Freriksen: “If the transformer indicates a fault through increased hydrogen levels, it may also be necessary to deploy a multigas monitor such as the [Vaisala] OPT100, in order to obtain a full fault diagnosis.”
Data from the MHT410 continuously feeds into the Eneco digital control system, which Laurens is able to access from his laptop. This allows him to track transformer load on the same screen as the MHT410 measurements.
“The digitisation of assets is an important issue. Remote access to live data informs decision making, lowers risk and was an enormous benefit during the Covid lockdown, because it meant that we could check the transformer at any time, from anywhere,” explains Freriksen.
Digitisation also reduces unnecessary site visits, especially with a Vaisala monitor that does not incur an extra service requirement.
The MHT410 has been set to raise a high level alarm at 100ppm hydrogen and a very high level alarm at 150ppm. In addition, an alarm will be issued if there is a sudden increase in the readings for hydrogen, moisture or temperature. However, during the first year of operation, there were no alarms, with hydrogen readings typically ranging between 2 and 15ppm, plus no significant effects during periods of high load.
The MHT410 takes measurements with an in-situ probe, removing need for pumps or membranes. With no consumables or moving parts that could fail, the instrument is encased in an IP66-rated metal housing equipped with a weather shield. Every unit is individually tested for a pressure of at least 10 bar and also withstands vacuum conditions and the MHT410 tolerates short-term power outages.
Says Freriksen: “The key advantage is that it buys us time – time to plan an effective strategy if oil conditions deteriorate - to optimise the performance of the transformer and to extend its working life.
“We have benefited from online measurements for around one year now, and it has been very reassuring to see low hydrogen levels in the transformer oil, irrespective of the transformer load.”